No two dealer businesses are the exact same in model.
Selling and servicing equipment, of course, are at the core of most dealer offerings – including those of Goodfellow Corporation. But Goodfellow, which operates out of five locations in Nevada, California, Utah and Arizona, is big on fabrication, as well.
As the dealer representing Astec in those states, Goodfellow regularly buys crushing, screening and conveying equipment from Astec. Goodfellow isn’t merely flipping equipment into the market, though.
As Goodfellow’s Chris Baron describes, nearly every piece of Astec equipment that his company purchases is incorporated into a Goodfellow design. Ultimately, each design is driven by Goodfellow’s customers, who collaborate with the company’s engineers to develop equipment that meets specific needs.
“We may buy a cone crusher or a screenbox from Astec, but 90 percent of the time it’s going to go on a Goodfellow-engineered and -built chassis or stand,” says Baron, vice president of sales at Goodfellow. “Even with overland conveyors and your standard stackable conveyors, the majority of conveyors we sell are designed, engineered and built by Goodfellow.”
Unique approach
Nowadays, more customers have equipment requests that cannot be met with a standard factory design. That’s where fabrication comes into play.
“We get a lot of requests for stationary screens that are custom designed,” Baron says. “They want blade mills to feed screenboxes, custom feed heights, catwalks, discharge points [and] transition points. Everything is custom from there. We get a lot of requests for custom chassis [and] a scalping screen on a jaw plant. We’ve had a request for a cone plant that has a bin feeder on it to feed a cone.
“We get requests for custom designs constantly,” Baron adds. “That’s the foundation of our business. If you guys can dream it up, we can provide it.”
While other dealers in the company’s territory may be doing some fabrication, Baron says no one is doing it to the degree of Goodfellow. And there’s a good reason for that.
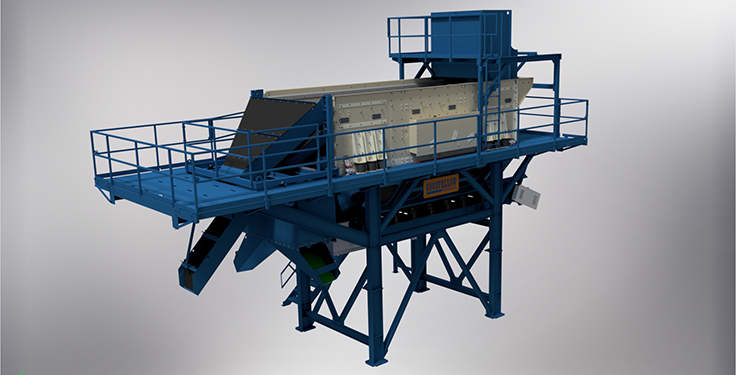
“Truth be told, it takes an enormous amount of resources and expertise to get into that business,” Baron says. “It certainly can be done. But the Goodfellow family are all engineering brains – and this business was built on their ideas. It’s evolved from there.”
Goodfellow has a long history of custom fabrication, too.
“I think custom designs are the reputation of Goodfellow,” Baron says. “If we look back to the 60-year history of this business, they’ve been building custom structures, chassis [and more] for 40 to 50 of those years. The foundation of this company is built on that high level of customization and working with the customers to meet those needs.”
Where & how it’s being done
According to Baron, Goodfellow currently fabricates equipment at three of its locations: Boulder City, Nevada; El Mirage, Arizona; and Lindon, Utah.
“Boulder City is our largest,” Baron says of Goodfellow’s fabrication facilities. “Arizona is runner-up, and third would be Lindon with their crew.”
The majority of Goodfellow’s stackable conveyors are built in El Mirage. The facility there also handles structures and smaller fabrication jobs.
“Everything large – stands, big chassis, jaw chassis, cone chassis, screen chassis – is built in El Mirage,” Baron says. “We just have enormous capacity there. That crew does a fine job. They’re very experienced, and we’ve got 25-year employees there who just know how to do it.”
Skilled employees are essential to making the fabrication part of Goodfellow’s business work, he adds.
“We’ve got some very well-rounded, seasoned expertise here dedicated to product development,” Baron says. “They work directly with manufacturing, so if there are challenges along the way, the engineers are pulled into it, they make adjustments and we move forward.
“There’s constant feedback from production back to engineering, and then engineering back to production,” he adds. “That system works very well. It allows us to constantly improve and evolve those products.”