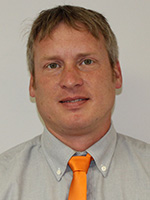
Several hazards are top of mind when Durex’s Chad Hackett steps onto a jobsite in a pit or quarry environment.
Hackett certainly keeps an eye on the mobile equipment crossing his path, and he is particularly mindful of the many moving parts present throughout an aggregate-processing plant.
Elevation is yet another safety consideration for Hackett, whose company’s products include wire cloth and specialty screen media, wear parts and accessories that are sometimes present at heights within tall structures. Elevation, of course, is a natural hazard, but Hackett makes a point to do a visual assessment of a structure before setting foot on it, too.
“All of this [equipment] is fairly high in the air on structures,” says Hackett, who serves Durex as president. “Those tend to be slippery and don’t allow you to see where you’re going. A fall from up there – 20, 30 or 40 ft. – is significant. Structures are generally well-built and well-maintained when they’re new. As things age and you have rocks popping out, hitting guards and all that, it can result in failures.”
Regular vibration can cause a structure or its parts to fail, Hackett adds. It’s not something producers and those climbing onto structures should take for granted.
“Welds and fasteners break,” Hackett says. “Some of these structures aren’t as well-maintained and aren’t as sturdy as others. So when I’m walking on them, I’m looking at how this thing is attached. I’m paying a lot of attention to those kinds of things.”
On wire screens
As a screen media manufacturer, Hackett is also well aware of the hazards associated with screen media and handling it.
Wire screen media, for example, presents all producers with a few common challenges. Parts of the media, of course, have sharp edges that can cause an injury.
“If something slips, that sharp wire can slice right through even fairly decent leather gloves,” Hackett says. “In our manufacturing operation, the guys handling the edges of those woven screens – shearing and bending them – are using double-palm leather gloves, and they shoot through two or three pairs a day at times. If you grab something wrong and it moves, it’s extremely sharp.”
Replacing wire screens on an elevated structure that has space constraints is no easy task, either. Hackett advises producers to take the necessary precautions when changing out wire screens, as accidents can happen.
“A lot of times, [producers] are in a hurry to change out media because it shuts down portions of their production line,” Hackett says. “The wire screen media panels aren’t relatively heavy compared to other things in the industry, but they’re still 300- to 350-pound handles.
“Between that weight and the awkwardness, it comes down to having enough guys there to handle these screens,” Hackett adds. “They’re up in the air, so it’s making sure they have equipment or cranes to put those screens up into the area rather than trying to haul them up decks.”
For P&Q’s full conversation with Durex Products’ Chad Hackett, click here.