Autonomous hauling is slowly, but surely, making its way into the aggregate industry.
While the technology has a presence in mining, there are several factors preventing it from fully transitioning to aggregates. Perhaps one of the top obstacles is downsizing the tech to “fit” onto the smaller haulers utilized in aggregates.
Currently, autonomous hauling tech is largely designed for use on trucks with payloads of 100 tons or more – the sizes often used in mining. In quarries, however, 100-ton trucks are often the largest size utilized, with many operators opting for smaller haulers ranging from 25 to 70 tons.
And while Luck Stone detailed plans early last year to outfit its Bull Run Plant in Virginia with the infrastructure necessary to autonomously run Caterpillar 777G haulers, autonomous tech is still a ways away from being a norm in quarries.
“If you think about a quarry application where you may have many fewer trucks, the heavy touch from an automation perspective is not required,” says Denise Johnson, Caterpillar group president of Resource Industries.
“So how do we scale in a way that makes all of the infrastructure that’s required and the operation much more seamless?”
Hauling case study
Although autonomous hauling has not yet found a full-time home in aggregates, the benefits of the tech for such an application are already being proven.
A recent case study conducted by Whittle Consulting for Pronto, an autonomous hauling systems provider, took a deeper look at the benefits. The study, titled “Autonomous Swarm Haulage: The Economics of Autonomous Haulage with Small Trucks,” looked specifically at optimal life-of-mine and net present value (NPV) produced in a simulation of a fictional yet realistic mining operation.
With a base case operation using manned “medium” equipment, the simulation looked at three other cases: autonomous “medium” equipment, autonomous “small” equipment and manned “small” equipment. The medium equipment involved a 31-ton excavator and a 100-ton heavy rigid mining truck while the small equipment involved a 13-ton excavator and a vocational 40-ton truck.
As for NPV, it is defined in the study as the net value of dollars of the mine over its life, considering future cash flows discounted at a certain rate.
The study found manned small trucks produced the smallest NPV ($356 million), followed by manned medium trucks ($390 million), autonomous medium trucks ($479 million) and autonomous small trucks ($510 million).
Going from a manned medium truck to an autonomous medium truck resulted in a 23 percent increase in NPV, while going from a manned small truck to an autonomous small truck resulted in a 43 percent increase.
From the base case (medium manned truck) to the final case (small autonomous truck), NPV increased 31 percent.
“We went into this thinking this would be the outcome,” says Christian Kurasek, CFO at Pronto. “There has been a lot of talk in the industry over the years about how autonomy should shift the economics of truck sizing to smaller trucks. The outcome was surprising in that the impact of moving to small trucks under autonomy was as large as it was.”
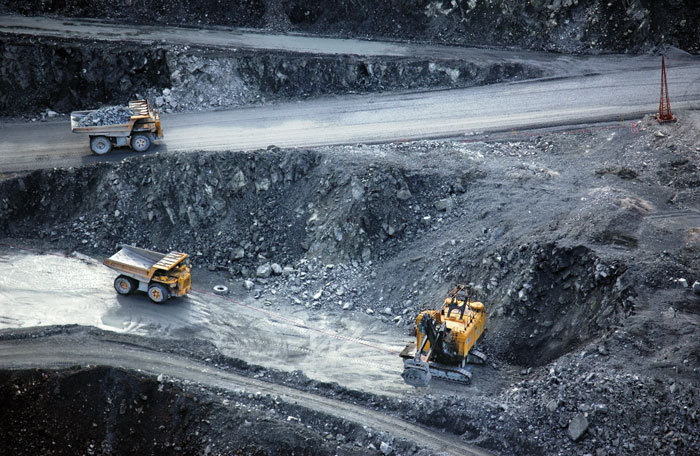
Autonomous small trucks provided several benefits, according to Nick Redwood, author of the study.
“In addition to the increased effective utilization provided, autonomy at a low cost-per-vehicle rate is the key to unlocking the benefits of the small equipment modeled here – reduced truck capital, reduced truck maintenance and improved haul speeds,” says Redwood, senior technical services specialist at Whittle. “These benefits are supplementary to other potential benefits of small vocational trucks, which include electrification and short lead times.”
Compared to manned medium trucks, both small truck cases showed large improvements in drive count and cost, setup cost and uphill speed. Additionally, the small autonomous case showed a large improvement in available time of trucks.
Both cases did, however, show large increases in excavator drive count and cost, while also showing small decreases in truck life and small increases in excavator capex and opex. The manned small truck case had a large increase in truck driver count and cost. That factor did not change for the small autonomous operation.
Going into the study, it was hypothesized that congestion problems would have been more common with an increased number of small trucks compared to fewer medium-sized trucks. The opposite was found, with both the manned small truck and autonomous small truck showing less congestion than the manned medium truck.
“We were very pleasantly surprised to see that, in the simulation, congestion did not become an element that limited the benefits of autonomy,” Kurasek says.
Looking ahead
Rather than attempt to scale down autonomous tech that larger trucks are using, Pronto’s goal is to design an autonomous hauling system based around smaller trucks and then scale up as needed. The company is seeing this technology put to use at a quarry in Santa Rosa, California.
“It’s transformed their operations, it’s economic and it’s making them more money,” Kurasek says. “So, we’ve been focused on solving that scaling-down issue from the beginning, because that’s just a much bigger market in terms of number of trucks out there and number of operators.”
Kurasek sees the future of hauling in mining and quarrying being made up of small autonomous trucks. It isn’t going to happen overnight, though.
“We aren’t aware of a situation where [40-ton vocational trucks] have replaced big trucks – yet,” he says. “But we think that’s where the industry is going. It’s always going to be site specific, and there may be different variables that push the equation one way or another. But in the right applications, that’s where we think the industry is heading.”
According to Kurasek, factors that will contribute to deciding when and if to make the shift from larger autonomous haulers to smaller ones include if smaller trucks will provide a higher NPV and the age of the current fleet.
Regardless of how soon small autonomous trucks are implemented into mining and aggregates, Kurasek believes they will eventually find a home in both.
“In an industry that’s increasingly being squeezed to do more with less, a fleet of small autonomous trucks is one way to move more with less upfront capex and less ongoing opex,” he says. “Not only do we think that that’s the future, but we’re starting to see it. I think 30 years from now, every mine will be designed for small autonomous trucks.”
Related: How mining operations are adopting autonomy
Editor-in-chief Kevin Yanik contributed to this article.