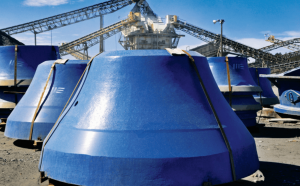
According to ME Elecmetal, it produces crusher liners using an optimal blend of high-performance alloys and never taking shortcuts in the heat-treating and quenching processes. ME Elecmetal premium crusher liners are available with M1-14 percent, M2-18 percent and 21 percent manganese content. The long-wearing liners can help reduce a producer’s overall cost per ton of crushed rock processed.
Liners deliver extended service life
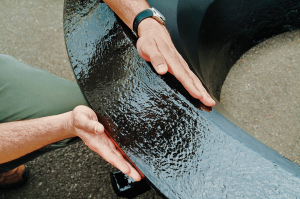
Columbia Steel’s newest alloy advancement, the L7 Alloy, delivers improvements in cone crusher service life compared to the original equipment manufacturer (OEM) offering, according to the company. Created when a customer sought to improve ROI on OEM MP800 liner sets, Columbia Steel says the L7 Alloy nearly doubled the service life of the customer’s liner sets by reformulating the original L78 Xtralloy high-manganese alloy, modifying the heat treatment of parts cast in L7M to reduce internal stresses, redesigning the liners’ geometry, casting a mantle thickness of 7.27 in. (DIS) and casting a bowl liner thickness of 6.32 in.
Parts ready when operators need them

Wear consistency allows operators to plan changeouts and maintain healthy equipment. If parts wear too quickly, they can cause damage down the line to screens, conveyors, jaws and rotors – every component of the plant. With tens of thousands of dollars of product on the line, manganese is serious business. According to Unified Screening & Crushing, its castings come from an ISO foundry with extensive quality control. The company maintains a large inventory of wear parts on the ground that’s ready to ship.

Blow bars feature added strength, durability
AMCAST’s MasterCeramic blow bars have special ceramic particles with a modified shape to permit increased adhesion to the surrounding steel. This, in combination with a 60 percent thicker inlay and a tailored design, allows blow bars to maintain their original wear profiles throughout the entire life of the part.