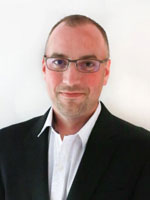
I put myself through college in the early 2000s by working for my father-in-law as a mason tender.
If you’ve ever cut stone, brick or blocks – or worked with an old-school Vermont mason – you know it’s tough work.
I spent days near clouds of dust that emanated from whatever rusty mixer I was using to mix the next batch of mud. The diamond blade block saw spit out a cloud of dust that resembled a NASCAR burnout – so much so that dust clouds billowed from the seat of a truck when I sat down.
The brick saw we used had a built-in water suppression system, and it was much better to work with. Twenty-plus years later, technology is more prevalent to help knock that dust down.
Readying for regulation
Silica, also known as respirable crystalline silica – or “quartz dust” – is an occupational hazard that can be generated when performing any activity disturbing content containing silica.
Long-term, uncontrolled exposure can cause silicosis and other respiratory diseases that are not reversible. These diseases can be fatal.
Many activities generate silica dust, including crushing, cutting, chipping, grinding, excavating and hauling materials that contain silica. To know if your organization has silica exposure, you must perform sampling so you know what you’re working with.
As you may know, the Mine Safety & Health Administration (MSHA) recently revised the regulations surrounding silica. Safety, legal and operational teams across the industry are creating plans to comply with the advanced expectations, including stringent sampling; tighter exposure limits (i.e., a 50 percent reduction); medical surveillance, if exposure limits are tripped; and an industry push toward engineering controls.
Any company crushing rock should have this on their radar and be poised to act. These plans will take time to create, but they will help to reduce exposure and increase total worker health.
In the meantime, teams should assess their existing controls.
Managing exposure
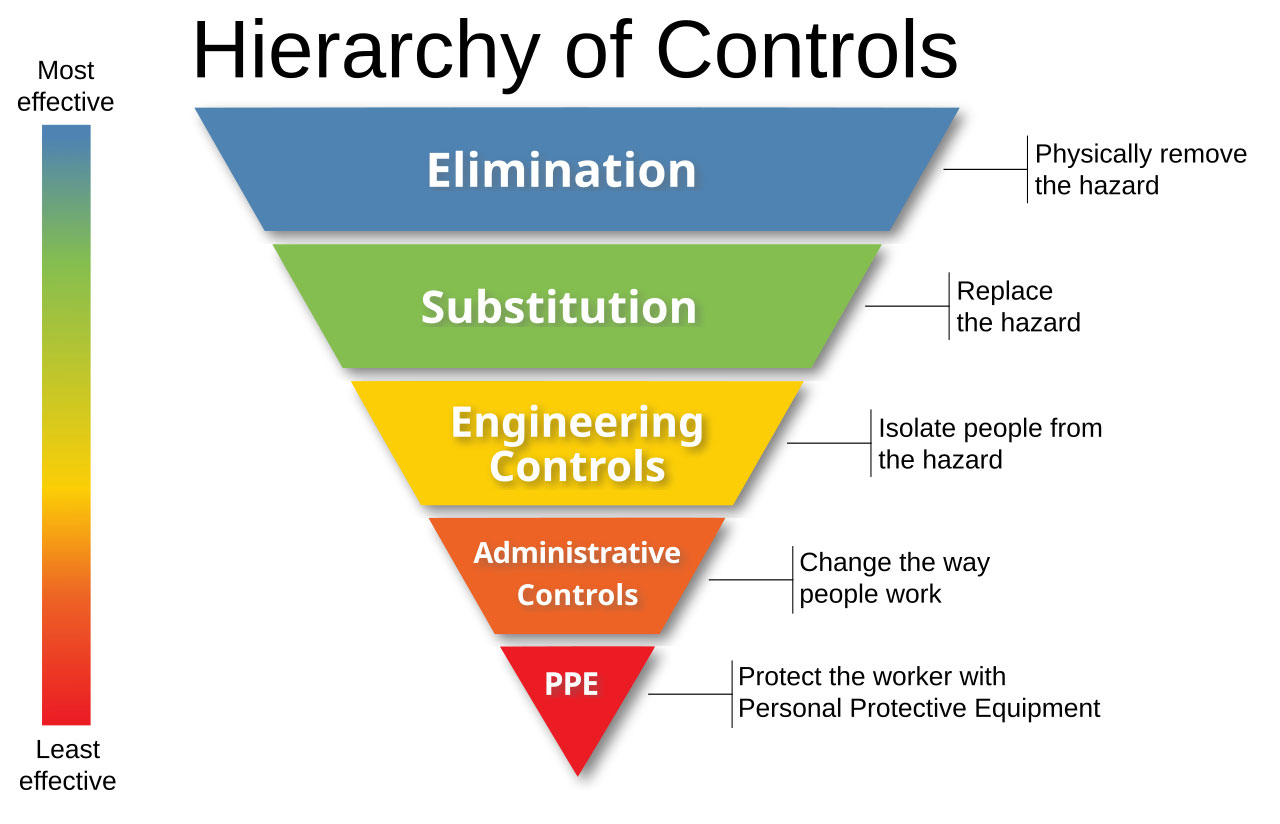
A great way to assess controls is to refer to the upside-down triangle commonly known as the hierarchy of controls.
Controls near the top of this pyramid (i.e., elimination) will be more effective than the controls near the bottom (i.e., PPE). Can you think of an example for each type of control as it relates to silica exposure?
Here are two engineering controls that are incredibly effective when combined:
• Wet methods. Using water to knock down dust is extremely effective. According to Occupational Knowledge International, wet methods are 60 to 86 percent effective.
• Isolating workers. Staying out of dusty areas can be the most effective, potentially eliminating exposure altogether. Enclosed cabs with filtration systems, staying in the control house during crushing operations, or simply being cognizant of positioning can help drastically.
These two items should be front and center as you develop plans to comply with MSHA regulations. If you can manage the exposure through these methods, you may be able to avoid respirators and medical surveillance.
Another tip for organizations is if they have not added silica awareness to their MSHA refresher training, they should consider doing so.
Recently, I supported an organization performing preemptive sampling to see where it would land with the new standards. Although the organization’s sampling came back below the new MSHA action thresholds, it proceeded with some best practices that included wet methods and isolation controls.
Regardless of dust’s silica content, you don’t want to be breathing in anything other than clean air.
Steve Fuller has worked over the past 20-plus years with a variety of industries – including aggregates – in operational and safety leadership roles. Now representing Steve Fuller Company, he can be reached at steve@stevefullercompany.com.