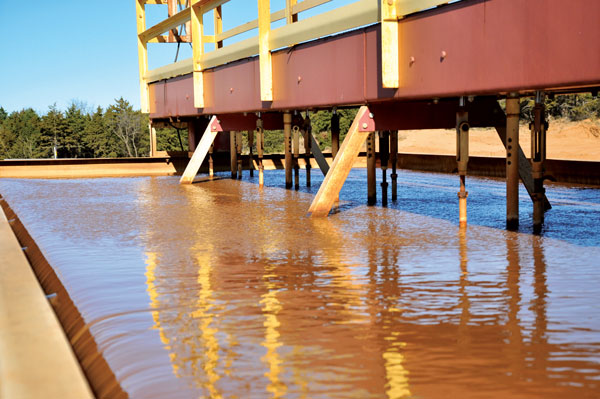
Sand must be washed and possibly classified to meet most specifications for end use in concrete and asphalt products.
Specifications only allow for a minimal amount of minus-100 and minus-200 mesh material. Many sand deposits and crushed stone sands have excessive amounts of these fine materials, which include silts, dust and clay that can effectively be removed with the correct washing process.
About classifying tanks
Classifying tanks are commonly used for washing and classifying sand.
In addition to removing silts to produce an in-spec product, classifying tanks are used to scalp off excess water from the feed and to make multiple products from a single feed. They also process high tonnages to keep construction-grade sands economically and efficiently in spec.
Classifying tanks contain six to 11 valve stations, depending on the size of the tank. Each station includes a paddle-sensing device and valves – the latter of which are operated by hydraulic cylinders located in a bridge running the length of the tank.
When a sand slurry enters a classifying tank, the larger, heavier particles in the feed settle out in the first stations. Successively smaller sizes settle out in the remaining stations.
Once the sand in each station reaches such a point, it stalls the sensing paddle. The valves are actuated or open via a PLC that receives a signal from the sensing paddle’s stall motor.
The sand discharges from the respective valves into three separate collecting-blending flumes beneath the tank. The flumes recombine the fine and coarse sand fractions discharging from their valves for each product, channeling them to the dewatering equipment below the classifying tank. Typically, fine material washers or dewatering screens are used.
As with any piece of processing equipment, maintaining a classifying tank is critical to optimize its function and reduce unexpected downtime. With this thought in mind, here are some maintenance and operation tips to assist with your process:
Keys to remember
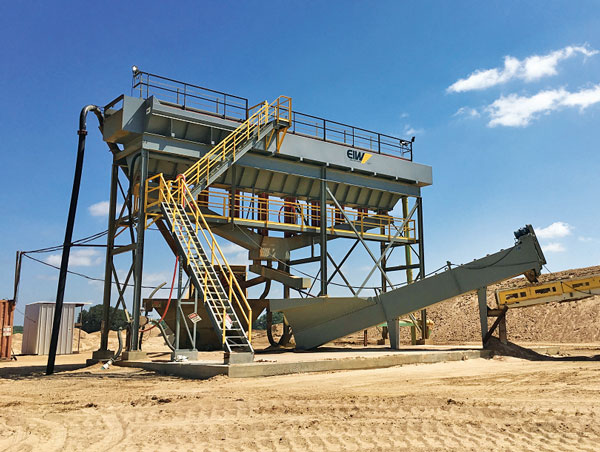
1. Ensure you have enough water. There are two rules of thumb to determine how much water is needed for a classifying tank.
For starters, a classifying tank requires 100 gpm of water per stph of silt feed. So, if you are processing 200 stph of sand and 10 percent of that is minus-200 mesh silt, you need 2,000 gpm of water to effectively remove most of the silt.
Also, classifying tanks require 10 gpm of water per stph of sand solids feed. If, for example, you have 300 stph of sand, you need 3,000 gpm of water to classify effectively.
Water can be added to a classifying tank from three sources: with the solids feed entering as a slurry, in the rising current classifier manifold or with a recirculating pump.
Most water enters a classifying tank with a sand slurry, but water can also be injected through a rising current classifier manifold located in the first three cells of the tank to aid in classification. In some instances, when sufficient water isn’t present, a recirculating pump that recirculates a portion of the overflow back to the feed area can be utilized.
Still, the ideal scenario is to have enough fresh water available without recirculating overflow water containing dirt and silt back into the tank.
2. Consider adding rising current. Rising current water injection aids in the best classification of coarse, intermediate and fine sands. To improve the efficiency of the hydraulic classification in the classifying tank, optional rising current classifiers can be installed in the first three stations of the tank.
By implementing rising current classifiers, the tank’s classification is greatly improved. Rising current classifiers keep the lightweight, smaller sand fractions in suspension while heavier, larger particles settle out at the infeed end of the tank. This helps producers achieve greater control over their final product gradations more efficiently.
While rising current classifiers will improve the separation of coarse- to fine-mesh sand fractions, they do not replace the need for mechanical screening to gain effective top-size control of a product.
It is important to balance the amount of water coming in with the sand slurry feed with the water coming into the rising current classifier. Generally, one-quarter to one-third of the total water needed can come from the rising current, with the remainder of the water coming in the sand slurry. This is an ideal combination that helps the classifying tank work more effectively.
3. Leveling weirs. Leveling or setting the weirs allows for good sand classification and silt removal. If you need to remove more minus-200 mesh to the overflow, you might raise the side weirs and drop the back weir to keep those ultra fines suspended and overflowing the tank. Adjustable weirs should be set level so each side has equal overflow depth.
4. Sensing paddle height setting. Usually, the paddle height setting should be the highest in the first three stations and slightly lower in the latter stations of the classifying tank. This is because coarse sand readily flows very fast as opposed to the ultra-fines sand –nominally at minus-50 mesh.
When the paddles are set closer to the bottom of the tank in the fine sand sections, the valve is able to discharge concentrated sand and not an excessive amount of water.
5. Performing routine maintenance. As with any piece of equipment, routine maintenance is important for proper classifying tank operation. Following a maintenance schedule and performing routine inspections can help reduce unexpected downtime with equipment.
It is also important to keep spare parts in stock such as hydraulic cylinder rebuild kits, solenoids and mercury switches so you are always prepared for any necessary maintenance. Also, remember that instructions for various maintenance procedures, such as replacing key components, can be found in the machine’s manual.
Properly maintaining and operating a classifying tank will help it function at its highest level and reduce unexpected downtime. Following the maintenance tips and best practices presented in this article will help you more effectively operate your classifying tank.
Information for this article courtesy of EIW (Eagle Iron Works).