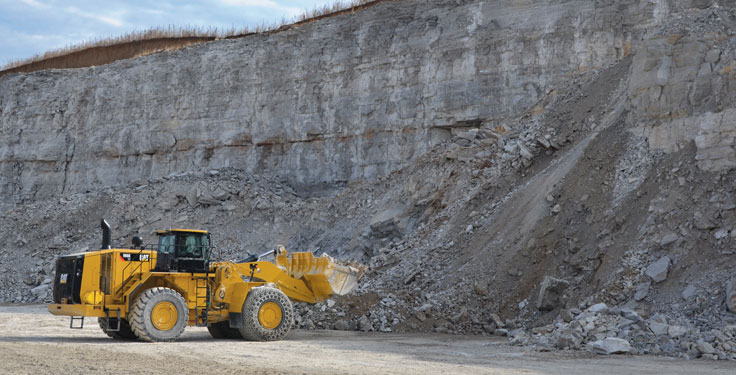
Aggregate producers are always fighting fines through the blasting, crushing and screening process to minimize the percentage produced.
Fines dramatically lower the net income margin of sites, as they often sell for a lower price. They’re processed into manufactured sand, increasing costs while selling for a lower price per ton than other products. Fines are also discarded as waste.
Most markets have a lower demand for fines and sands than other products. Regardless of how a site treats fines, they are an undesirable product leading to worse site performance.
There are, however, methods to eliminate fines production in blasting. Let’s explore.
1. Fix the spacing
Blasthole spacing is one of the most important topics when considering the percentage of fines a blast will produce. This is an often-overlooked metric, with many sites setting the blasthole spacing equal to the burden (a square pattern) or expanding it to some base ratio (a rectangular or triangular pattern).
While these have applicability in very specific scenarios, the base rules of thumb are often overapplied to every site and every blast – and they can cause significant increases in fines.
Richard Ash, a longtime professor of mining engineering at the School of Mines & Metallurgy at the University of Missouri-Rolla, previously laid out a broad range of spacing-to-burden ratios that were used. These had the spacing equal to twice the burden in some situations.
These metrics were developed by surveying a variety of sites around the U.S. and developing guidelines off their reported blasting practices. Later, Calvin Konya took this work and expanded it, studying the variations in the optimal spacing-to-burden ratio based on a blast’s stiffness ratio and hole-to-hole timing.
Konya found that the “taller” a bench, or the larger the bench height compared to the burden, the greater the spacing-to-burden ratio needed to be in order to have proper fragmentation. Konya also found that if holes in a row were fired instantaneously instead of with a short delay, the spacing-to-burden ratio had to increase.
This established two fundamental concepts in blast design. One was that the spacing-to-burden ratio must be changed based on the timing and the bench height. This added validity to Ash’s survey results, showing that the reason for the large variation in the spacing-to-burden ratio from the surveys was a result of the differences in bench height and timing – not necessarily the rock type.
Since then, I’ve taken these concepts and further developed the relationships, specifically targeting the changes to spacing-to-burden ratio compared to hole-to-hole timing in milliseconds of time per foot. This led to a clear understanding that the faster the hole-to-hole timing, the larger the spacing has to be to keep a consistent fines percentage.
This will also lead to an increase in oversize, so the methodology for designing a blast must be carefully constructed to ensure fines are appropriately reduced with variations to the timing and spacing, while also keeping oversize under control. All of this winds up taking the blasting optimization processes into a multivariable state in which multiple groups of variables are modified and optimized over a long-term period for a site to develop the optimal fragmentation profile.
One telltale sign that spacing could be optimized better: If the spacing is equal to the burden on a blast, it is likely that improvements could be made to the spacing-to-burden ratio. This does not hold true in every situation, but in the vast majority of cases this is an indicator that a discussion with the blaster is required.
2. Blasthole sequencing
The second metric to analyze is blasthole sequencing. This is a simple yet difficult design variable.
When a blast design is developed, a timing pattern is laid out that includes both the sequencing, or the order in which blastholes are detonated, and the timing, or the actual time between each hole firing in the developed sequence. Blasthole sequencing is extremely important, as changes in blasthole sequencing result in changes to the true burden and the true spacing of a blast. This is because the blast “senses” the burden as the distance to the nearest relief at the time that the blasthole detonates and becomes pressurized.
Let’s take an example of two patterns to illustrate the differences in burden and spacing based on sequencing of the blast. Assume that the blaster designs a blast and has the appropriate burden, spacing and timing for the situation. In the first blast, the blaster designs the shot to detonate with each row firing straight toward the free face. In this case, the burden and the spacing are what the blaster originally designed, and the fragmentation of the blast is appropriate.
Now let’s assume that on the next blast, the blaster decides to pull the shot from the center and expand outward and backward, with the same millisecond timing, burden and spacing as before. This time, the blaster gets a significant increase in fines and oversize.
So, what happened? In reality, what occurred is that the pattern was fired on an angle, leading to a decrease in the effective burden of the blast that resulted in the burden being significantly less than the blaster designed. This caused an increase in fines and a faster velocity face movement, which led to more material throw. At the same time, this led to an increase in the spacing of the blast, which results in oversize generated between boreholes.