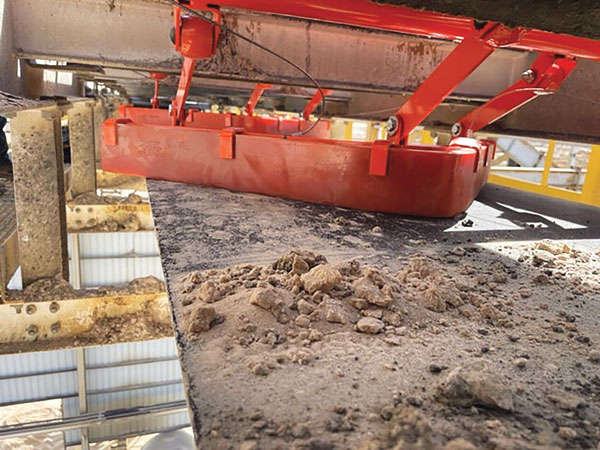
Anything that clings to the return side of the belt and travels with it is considered carryback, which can seriously damage a system.
Not only is it a major source of fugitive dust and fines, but it migrates easily into return rollers and take-up pulleys, fouling the bearings, drives and the face of the roller. The grit grinds down roller bearings and leads to excessive friction heat, causing them to misshapen and seize.
Like spillage, carryback can migrate to the non-carrying underside of a belt. These chunks travel all the way to the tail pulley. The intense pressure between the pulley and the belt causes the hard, sharp mass to damage the vulnerable side of the belt and the pulley face – with each cycle delivering more damage. Dust and fines can get into these blemishes and foul the pulley face, as well as lower the life of the belt.
When a roller or a pulley face is fouled, it is caked with abrasive grit that can degrade and damage belting over time. In some cases, fouling causes slippage that can disrupt the smooth operation of the belt and promote mistracking.
If adequate space is available, install secondary and tertiary cleaners to ensure the belt is clean on the return. To improve safety, consider units that allow a single worker to pull them away from the stringer for faster external servicing.
Also, consider a diagonal or v-shaped plow underneath the loading zone – right before the tail pulley – that rides on the underside of the belt to remove loose traveling material.
For more effective cleaning and to reduce friction damage, consider a plow with torsion arms rather than one held in place by chains. Install belt trackers or crown rollers along the upper and low belt path to ensure alignment.
Safely addressing bulk handling clogs
A clogged transfer chute or hopper is one of the most dangerous situations in bulk handling.
Untrained and uncertified (enclosed chute entry certification) personnel should never enter a clogged chute or bin under any circumstances. A sudden discharge can be deadly, as an unknown void engulfs and crushes a worker. Material adhered vertically to the sides can loosen and send a sheet of debris falling onto anyone occupying the vessel.
Buildup points in chutes include:
• Exit gates or doors. As these help control flow, they are prone to clogging.
• Sloped points. Under the secondary cleaner, chute grades or located at choke points.
• Metal surface grain. The metal grain of chute plating should match the flow of cargo.
• Exposed surfaces. Surfaces where moisture can collect and cause buildup.
• Damaged surfaces. Surfaces that have scratching, denting, creasing or divots.
Misguided practices for addressing buildup are banging on the sides of the hopper with a mallet or loosening the obstruction by poking at it from below.
In some operations, clogs are so frequent that spots for pounding are marked and mallets are left in the area for convenience.
This is hazardous because it reduces the structural integrity of the vessel or chute and causes it to buckle. Ripple damage from pounding creates a situation where material build is more likely, shortening periods between clogs while leading to more unscheduled downtime. Poking from below is even more dangerous, because a sudden discharge sends tons of material in a surge that can injure anyone in the vicinity and break equipment below.
To avoid these unsafe approaches, air cannons can strategically be installed around the chute and have nozzles pointed in the direction of the material flow. Powerful shots of air can be distributed across the surface inside the vessel, dislodging material and preventing buildup.
Air cannons are supported by vibration units that ensure gates and narrow spouts on hoppers and chutes retain proper flow before bridging starts. In many cases, vibration alone can handle most dry material flow, but changes in humidity raising the stickiness of cargo and chute surfaces, along with fluctuations in production volumes, are much better handled by air cannons.