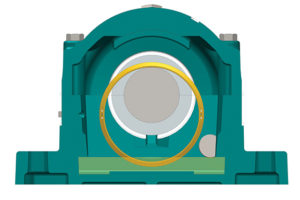
Hydrodynamic journal bearings, also known as oil film bearings, are frequently used in critical applications such as fans, pumps, motors, crushers, conveyors and high-speed gearboxes, where they are required to run for long periods of time.
Advantages of hydrodynamic bearings include long service life, minimal maintenance requirements and damping that can significantly reduce vibration.
Several methods of lubricating these bearings can be found in various applications. They include oil slinger discs, gas lubrication, oil rings or forced-feed circulating oil. The benefits of circulating oil in ring-lubricated hydrodynamic bearings are plentiful.
Background
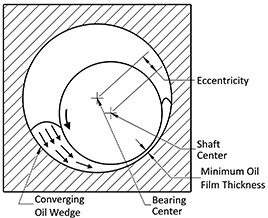
In hydrodynamic journal bearings, the shaft rides on a thin film of oil, which separates the shaft from the Babbitt bearing surface. The clearance between the shaft and the bearing bore, the bearing load and the shaft speed determine the thickness of this film.
When the shaft first begins to turn at slow speeds, there is very little lubricant between the shaft and bearing. This is known as the boundary lubrication regime. During this period, the asperities, or microscopic imperfections, on the shaft surface come into contact. Nearly all of the wear that occurs in journal bearings happens during boundary lubrication. In this condition, the bearing is vulnerable to damage from contaminants such as dirt or ash that may be larger than the oil film.
As the shaft speed increases, the oil film forms between the two surfaces. At first, the film is thin enough that the asperities still come into contact, which is known as the mixed film lubrication regime. Once the film is thick enough to fully separate the surfaces, it is known as the full film lubrication regime. During this regime, there is no wear of the shaft or bearing, and the bearing is generally safe from contaminants smaller than the oil film.
Still, if insufficient lubrication is provided, then the bearing will run in boundary or mixed film regimes and risk accelerated wear.
Oil ring lubrication
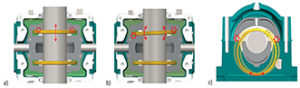
Hydrodynamic journal bearings in low-speed (up to about 150 ft. per minute) to medium-speed (up to about 4,000 ft. per minute) applications are often lubricated by one or more oil rings that ride on the shaft and dip into the oil sump below. As the shaft turns, friction between the shaft and the oil rings causes them to turn as well, bringing oil from the sump to the shaft and lubricating the bearing.
Key benefits to oil ring lubrication are that it is cost effective, allows the bearing to be fully self-contained and, if sized properly to the application, can provide sufficient lubrication to the bearing at the required operating speeds.
But there are situations where oil ring lubrication alone is not ideal. At startup, there is no oil available to separate the shaft and bearing. This results in metal-to-metal contact and bearing wear.
Oil ring lubrication is also not ideal during slow speed operation. When the shaft speed is low, the oil film between the shaft and bearing will be much thinner than during normal operation, and the bearing may operate in the mixed film or boundary lubrication regimes and risk accelerated wear.
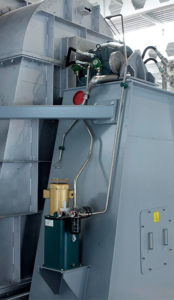
Likewise, at high speeds (about 4,000 ft. per minute or greater), oil rings struggle to deliver enough oil to fully lubricate the bearing. A large difference in shaft and oil ring rotation speed prevents the oil rings from delivering adequate oil to the bearing, resulting in mixed-film or boundary lubrication. This can cause the bearing to fail at high speeds due to temperature.
Oil rings can also begin to oscillate at high speeds due to vibrations in the system. This not only reduces oil delivery but can also cause the oil ring to come in contact with fixed structures in the bearing and cause damage.
Benefits of circulating oil in ring-lubricated bearings
There are several benefits to using an external circulating oil system on hydrodynamic bearings that can improve bearing performance and reliability. These benefits include sufficient oil flow at all times; continuous oil filtration, easy monitoring of oil quality and temperature; cooling; and redundant lubrication.
- Sufficient oil flow at all times. Circulating oil, or force-fed lubrication, is when an external pump directs oil directly to the shaft before, during and after operation. Ideally, the oil flow to the bearing is sufficient for operation at all potential operating speeds, including at startup and in slow-speed turning gear applications. By reducing the amount of time spent in
Bearing and shaft surfaces during boundary lubrication (a), mixed film lubrication (b) and full film lubrication regimes (c). Photo courtesy of ABB Motors & Mechanical Inc. boundary or mixed film lubrication, adding circulating oil can significantly reduce bearing wear.
- Continuous oil filtration. Second benefits of using circulating oil lubrication is that the system is being continuously flushed, and harmful contaminants are removed. This is critical because contaminants can cause damage to both the shaft and bearing, especially during boundary lubrication. Another concern is that contaminants can partially embed into the oil rings, which are usually a semi-soft metal such as brass or bronze. At slower speeds where there is no film between the oil ring and shaft, these partially embedded contaminants can damage the shaft.
- Easy monitoring of oil quality and temperature. With a circulating oil system, there is a steady flow
Shaft damage due to contaminants in the oil rings. Photo courtesy of ABB Motors & Mechanical Inc. of oil into and out of the bearing, and the circulating oil system usually has a significantly larger reservoir than the oil sump. This makes it easy to safely take live samples of the oil going into and coming out of the bearing. While it is possible to take a live oil sample directly from the bearing, this would require getting very close to spinning, potentially hot machinery and is not recommended.
- Cooling. In lightly loaded and low-speed applications, hydrodynamic bearings can operate without any external cooling. However, many applications generate too much heat for either the bearing material or the lubricant and require external cooling. Bearing manufacturers have used water, compressed air and sometimes air over the bearing housing to remove heat. By using a circulating oil system with a heat exchanger, customers can obtain all of the reliability benefits of circulating oil while also eliminating the need for external cooling.
- Redundant lubrication. Due to the nature of hydrodynamic bearings, loss of lubrication – which can be caused by an oil leak or by failure of the oil rings – causes the bearing to instantly begin operating in the boundary lubrication regime, followed quickly by total bearing failure. For this reason, it is very important to have redundant lubrication systems for the bearings in critical applications.
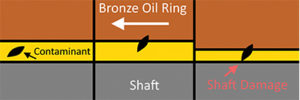
When used in conjunction with oil rings, a circulating oil system provides redundancy that can allow an operator or automatic system to shut down equipment before the lubrication failure becomes a catastrophic bearing failure.
Final thoughts
The use of circulating oil is always beneficial for hydrodynamic bearings. Bearings in both new and existing applications can see improvements in performance and reliability with the addition of circulating oil, reducing the risk of unplanned downtime.
Steve Pasternak serves as manufacturing engineer at ABB Motors & Mechanical Inc.