The following transcript was edited from one of two concurrent discussions that took place June 3 at the 2021 Pit & Quarry Roundtable & Conference. A second discussion on industry regulation can be read here.
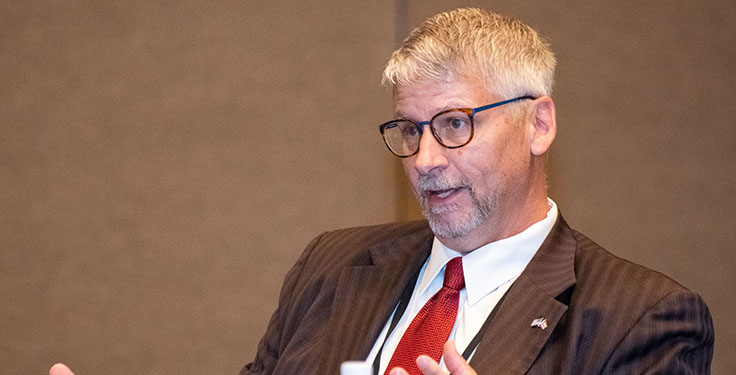
P&Q: Are you experiencing any change in approach by the Mine Safety & Health Administration (MSHA) since the Biden administration took office, or do you expect any change to come soon? Do you have any expectations on new MSHA rules, including respirable crystalline silica? What has your experience with MSHA been like regarding COVID-19?
PAT JACOMET (OHIO AGGREGATES & INDUSTRIAL MINERALS ASSOCIATION): I got a phone call with one of our educational field service representatives in Ohio. Unfortunately during the lockdown we saw enforcement continue, but the educational field services that provide the assistance side of MSHA have been on lockdown – and they’re still working from home. We’ve approached the administration about releasing those folks to go in the field and help our folks. I think compliance assistance is something that is very beneficial to our members.
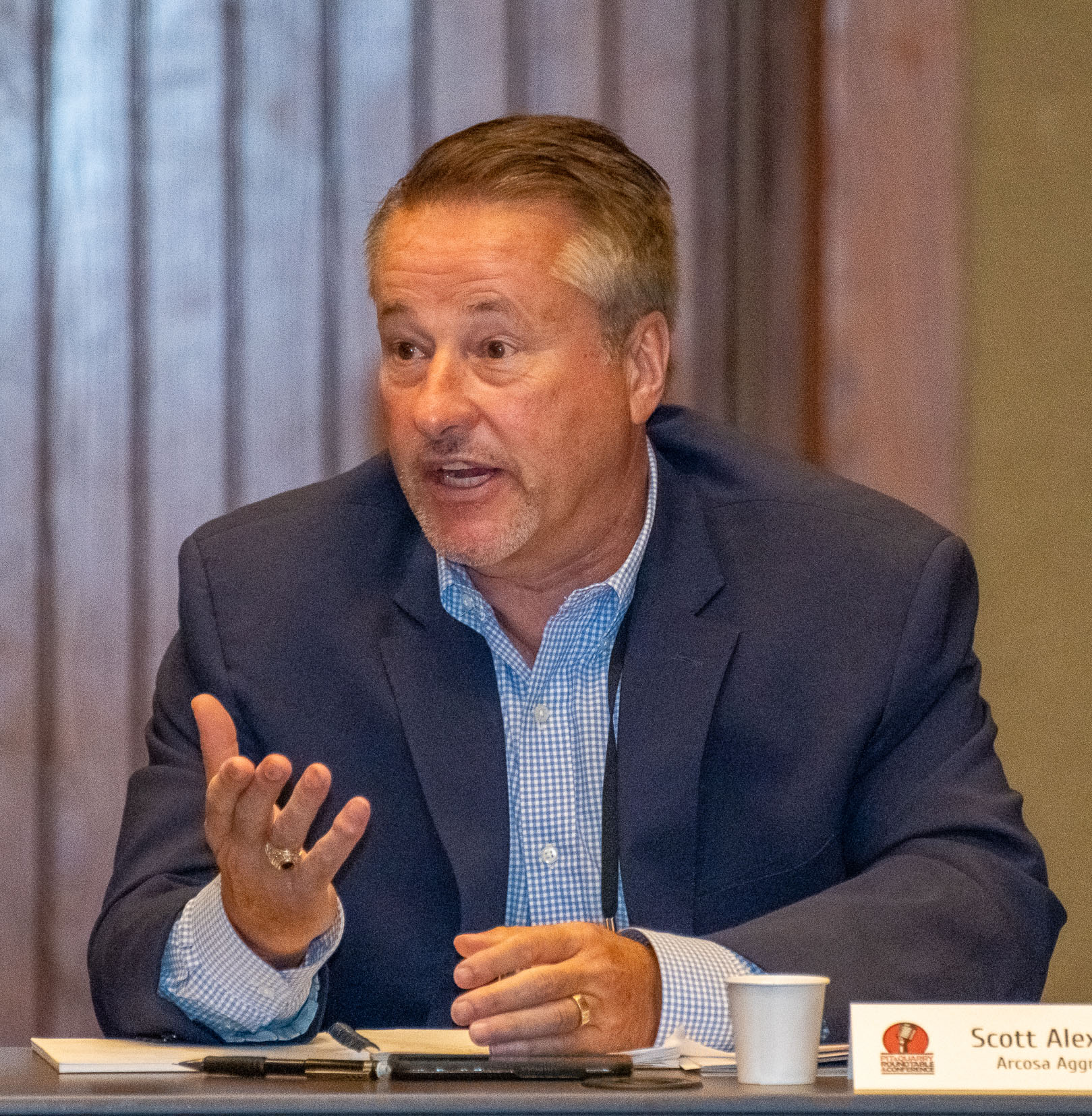
SCOTT ALEXANDER (ARCOSA AGGREGATES): Of the probably 40-plus active aggregate mines we have across the country, we get an MSHA inspection once a week. I get the notifications when that happens. I really haven’t noticed a bit of difference this year versus last year or the year before. It seems like they’re still out there on a regular basis. They’re still writing citations like they always do.
KEATON TURNER (TURNER MINING GROUP): We have operations across the country, and we didn’t really see MSHA slow down – even during COVID. They made the same number of visits. The citations didn’t go up or down either way. I think the only change that will be interesting to see is, because coal is potentially going the other way, how many coal inspectors are coming to service nonmetal sites. Those guys think of mining totally different than a cement producer or a quarry. Sometimes, our guys are educating the coal guys on how a Part 46 site operates – or at least they think they’re educating them.
DAN JOHNSON (VDG): I think products over time have gotten safer. I’ll just use plant equipment as an example. In the plant, you’re crushing, screening and conveying. I’ve worked in plants where we’ve had to change crusher liners once a month.
Well, the materials change. They go to a higher content of wear metals, and then they get down to 600 hours instead of every 400 hours. So maybe you’re changing it eight times a year.
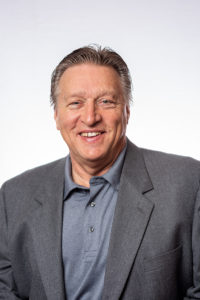
Well, that’s fewer opportunities for accidents. They’ve got hydraulic head nuts now where, instead of somebody having to weld a head nut on and cut it off with a torch and sling a sledgehammer and all that, it’s a much simpler, safer process.
With the evolution of screens, it’s all driven by the KPIs (key performance indicators) of the producers. They want to be more profitable. They want more plant uptime. They want more tons per man hour, more tons per plant hour. But in screening, the wire has been replaced in so many applications by synthetic media – albeit urethane, rubber or some other compound. Now, instead of needing to be changed out, say, once every single month or once every year, they’ve got more durable materials that might last a year and a half or two years.
On the conveying side, what you’re seeing is there’s fewer new installations that are using belt-driven conveyor power transmission products. I’m seeing more right-angle drives where they’re eliminating the belts. Manufacturers are making products that are maintenance-free, so nobody has to mess with them. There are no external moving parts. That’s driven partly by safety, but really by end-user demand for product that’s more durable and maintenance-free.
It would be wonderful if you could make your plant maintenance-free. You can’t. But cone crushers, screens, conveyors – everything involved is more maintenance-free.
Click here for Part 1 of the industry regulation discussion that took place at the 2021 Pit & Quarry Roundtable & Conference.