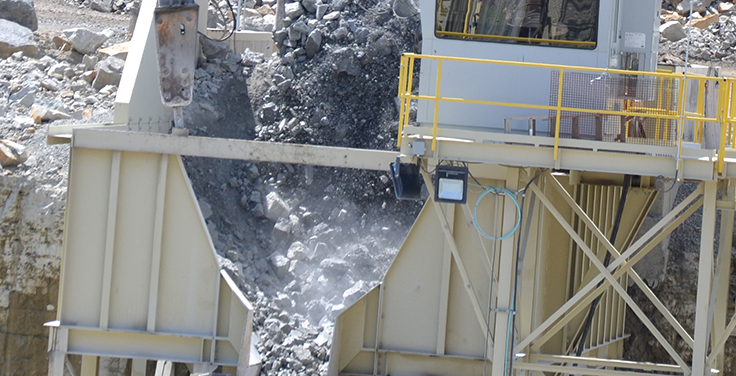
The handling of challenging materials in quarries has always posed risks and obstacles to worker safety.
From hand-arm vibration and falls from heights to explosives and heavy machinery, those working in pits and quarries are sometimes exposed to health and safety hazards. In fact, data from the Health & Safety Executive (HSE) shows that more than 3,500 industry workers have suffered an injury reportable to HSE since 2000 – with 31 of those being fatal.
Automation has long played a pivotal role in enhancing safety in aggregate operations. Machinery equipped with automation systems can perform tasks that people previously executed, eliminating the need for workers to enter hazardous areas.
Intelligent systems
One of the most significant advancements in quarrying tech is the introduction of automated crushing systems.
Crushing is an integral process, where large rocks and aggregates are broken down into smaller, more manageable sizes. Traditionally, the task involved heavy machinery and manual labor, which posed significant safety risks.
Crusher blockages can be highly hazardous and lead to costly downtime. To unblock a crusher, a plant must usually be shut down and the system isolated. Despite these precautions, a crusher can still be a serious risk to personnel due to the material that can be suspended in the crushing chamber.
In response, modern crushing technologies have brought about remarkable improvements in safety – and automation plays a pivotal role here. Advanced control systems and sensors are employed to monitor and adjust crushing parameters, ensuring optimal performance while minimizing human involvement.
Safer material separation
Screening, meanwhile, is a critical process that separates materials based on size, allowing the extraction of specific aggregate fractions. As with crushing, advancements in screening techniques have led to enhanced safety measures.
Traditional screens often required manual adjustment, increasing the likelihood of accidents during maintenance. But modern vibrating screens are equipped with automated features, such as self-cleaning mechanisms and remote monitoring systems.
Advancements in sensor technologies and computer algorithms led to the development of automated screening systems. These features not only improve efficiency but reduce the need for manual intervention, minimizing the risk of injuries.
Innovative sizing
Sizing materials in aggregate operations is essential to meet specific requirements for construction projects.
Traditionally, this process involved the manual handling of heavy machinery and increased the risk of accidents and injuries. Still, innovative sizing methods are transforming this aspect of quarrying, improving safety and efficiency.
Modern sizing techniques leverage advanced technologies such as laser scanning, 3D modeling and computer simulations. These tools enable accurate measurements and precise sizing without the need for workers to physically interact with machinery.
By minimizing manual intervention, these methods significantly reduce the risk of accidents and create a safer working environment for personnel working in the quarry.
David Strain is technical director at Technidrive, a U.K. company creating industrial drive solutions for industries such as aggregates, recycling, food and dairy.