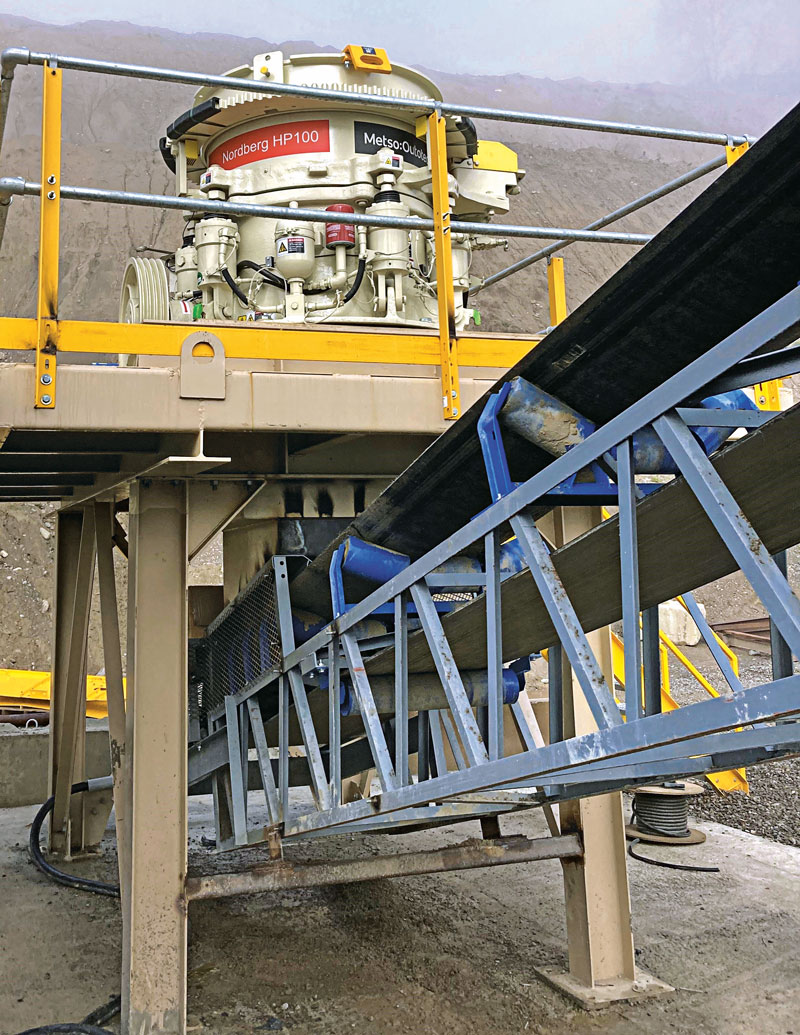
During crushing and toward the end of a shift, check the closed-side settings of all crushers.
This can be accomplished by a high-tech and technologically advanced method: with aluminum foil balls. For us, we would take a decent grade of aluminum foil and roll it in a way to produce two appropriately sized foil balls. (Note: The size should be comparable to the median size of the feed material going into the crusher).
Once the feed material to the crusher emptied out, we would drop the foil balls into the crushing chamber. This was done immediately after the feed material was cut off and cleared out to avoid increased head spin that could destroy the foil balls.
The foil balls would drop through the crusher onto a belt that should be shut down. We would then have the operator bump the belt up until the aluminum foil balls could be removed from the belt and measured.
Most of the time, we had two people dropping foil balls and two people retrieving them. So, we could complete the measurement all at once. If you don’t, then you would have to measure the standard crusher and repeat the steps for the short head crusher.
Once the foil balls were dropped and retrieved, we would measure them. We would do this with a set of outside diameter spring or dial mics. The foil balls would have a distinct flat spot across the face that was noticeable, and this would measure the “thickness” of the compressed materials to determine the closed-side measurement.
When the foil balls were dropped, the plant operator would shut the crushers down and initiate a stopwatch to measure the coast downtime. This is the amount of time it takes for the head to stop spinning and come to a stop. During the coast downtime measurements, we would also measure the head spin/rpms.
All these measurements would be noted in the daily observation log of the crusher. The info would be reviewed by the foreman, as well as anyone else who wanted to monitor the crushers.
The plant foreman would make decisions pertaining to the closed-side settings, determining how much the crusher needed to be adjusted to optimize production. The plant manager would often review the info to ensure the crusher was being appropriately inspected and adjusted to his liking.
Once the crushers were adjusted and all the inspections requiring the operator were concluded, I would go down and lock out/tag out – then try the crushers, the screens feeding them and the discharge belts. This left the most fun part of my working day.
Other inspections
I would grab my flashlight and start at the top of the crusher. I would check the crushing chamber, making sure all large material cleared the head. I would inspect the mantle, bowl liner, feed plate, feed plate adapter and any other wear surfaces that could be seen from the top of the crusher, looking for damage, missing parts and missing hardware.
On the way to the bottom side of the crusher, I would check over my lube system. I would look for leaks, frayed lines and any signs of impending issues.
I would also check my return oil screen to look for foreign matter such as locking compound, backing compound, brass or metal shavings. Each of these could be indicative of issues either happening now or those that could arrive soon.
Next, I would go under the crusher. I would check base bolts, the frame for cracks and look for any other signs of damage on my way under the crusher.
I would look over the drive system, checking v-belt guards for excessive rubber shavings and dust; checking the direct-drive systems for signs of grease in the coupling; and do a shaft walk for any possible out-of-the-ordinary signs.
I would then go under the crusher and check the bottom of the head skirt for damage and wear. I would check the bottom of the bowl liner for wear and damage.
I would also check the mainframe liners for wear and damage. And I would check my arm guards and counterbox protection saddles for wear damage.
Additionally, I would pay special attention to the oil galley of the frame, looking for “wet” spots. Oil and rock dust always seem to tell you about issues if you take the time to look and see what’s there.
Looking for anything out of the ordinary was part of this routine, as well. A good rule of thumb for crushing is if you haven’t “seen that before,” there is something you need to study and find out why.
Many machines have been crushing longer than some of us have been alive. With that, they should have a “normal” wear pattern. So, if something looks atypical, do yourself a favor and investigate further. Many issues can be handled in a timely manner if they are discovered quickly enough.