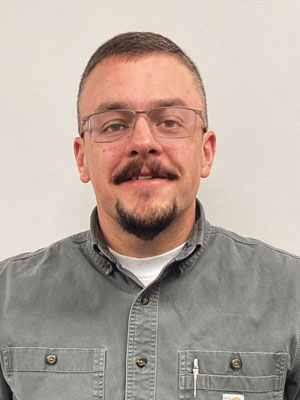
There are many ways to achieve a final product beyond a cone crusher.
Impactors, mills and roll crushers are a few alternative options. But in my area of operation, cone crushers are the most common solution.
I learned on the tried-and-true Symons/Nordberg 7-ft. standard and short head crushers. I was fortunate enough to learn a manual controlled system – no automation there – and the man who trained me, a 20-plus-year veteran at the time, would often say he was a firm believer that he could out-crush any automated plant.
I was transferred to a plant in 2009, right after a time of economic turbulence. To say we were shorthanded is putting it mildly.
I was transferred to run the secondary plant, and I had no experience running any plant at the time. I came from an automated plant where the jaw house operator also ran the secondary by his computer, and it seemed all he had to do was look at it from time to time.
I had limited exposure to the plant control side of things. That jaw operator wasn’t a very welcoming kind of guy, either, and anyone who has ever been to a quarry knows a jaw house is usually rather snug. So the last thing I wanted to do was climb into that “tin can” and ask him a bunch of questions.
To say I had no clue what kind of job I had accepted when I agreed to transfer is an understatement. I did, however, luck out with the new group of guys I worked with.
The foreman was a stern but fair senior employee with at least 25 years of experience at the operation.
Like me, he had grown up around the industry because his father had retired from that same operation. He was the type of leader who would take time to explain the how and why of things and not just tell you to “go do something.”
Getting to know cones
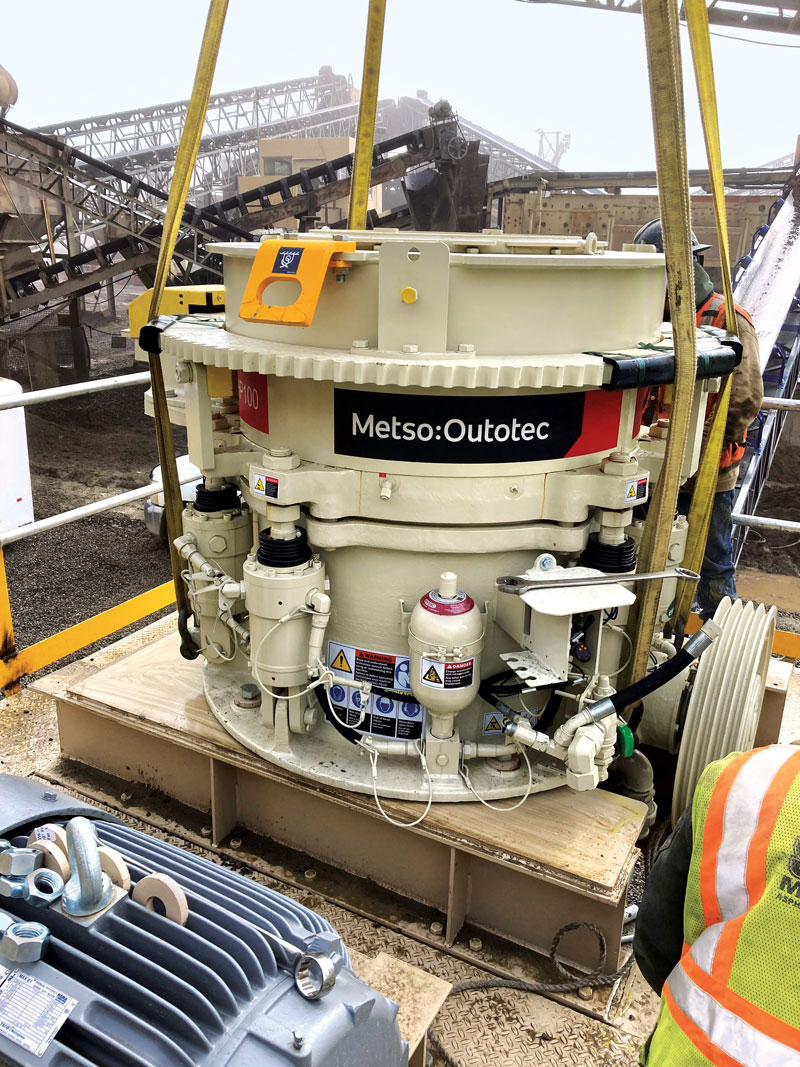
Cone crushers are the delicate dinosaurs.
To some, that statement may seem like an oxymoron. How, after all, could a dinosaur be delicate?
For starters, cone crushers are consistent in their operation. You put big rocks in and get little rocks out. That’s a basic description of the process, but there is much more than that to one cone crusher.
From the Symons/Nordberg 2 ft., 3 ft., 4 ft., 4 1/4 ft., 5 1/2 and 7 ft. all the way up to the newer high-speed machines such as the Omnicone series, HP series and even the GP series, I will primarily discuss the old Symons/Norberg design line with mentions of newer designs.
Symons are relatively simple machines with a few critical focal points. They seem to be forgiving machines up to the point when they’re not – and that’s when things quickly get expensive.
It takes a little time to dive into these machines. But once you understand what they need and what they’re trying to tell you, you will know how to run them consistently and faithfully. That is because so much relies on routine.
• Pre-daily operation. Be sure to properly train new employees on how to do their work safely and correctly. Production starts with your people, as they are your most essential piece of the production puzzle.
• Everyone should have oil tank heaters. And these should be operational. Consistency is everything to these delicate dinosaurs. Starting them every day with the fewest number of variables will lengthen the life of these machines.
Oil temperatures will vary. Ambient air temps, humidity levels and wind speed will all play a huge part in the oil temperatures – and the tank heaters can only do so much.
The Metso manual states: “Thermostatically controlled electric heaters are suggested to enable oil flow in cold weather. Heaters are recommended when lubricant temperatures in the oil tank drop below [60 degrees].” Where I am from, this applies to everyone.
• Check the oil level before starting the oil pump. This is to ensure there is enough oil present to prevent damage to the system before starting the pump. It is also a good practice to glance at the oil tank temperature gauge at the same time to ensure the oil is above 60.
• Scan the area for oil leaks or standout issues. Always keep your head on a swivel and be proactive when looking for obvious problems.
• Start the oil pump prior to starting the crusher. Obviously, this only works if you have a remote oil supply pump. There are still a few countershaft-driven oil pump machines out and about.