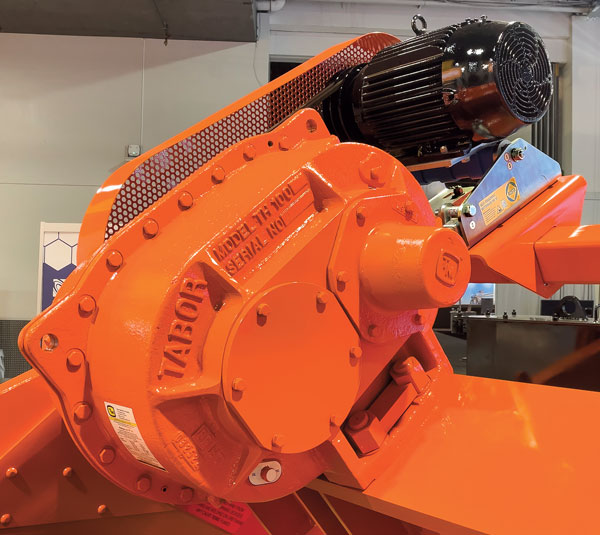
Vibrating screens are indispensable components in aggregate-processing plants, serving critical functions such as preparation, material sizing and dewatering.
To guarantee the efficiency and durability of these systems, consistent maintenance is imperative. This article offers insights about maintaining vibrating screens in aggregate processing plants.
Exciter oil change
To uphold the performance and longevity of vibrating screen exciters, adhering to a regular oil change schedule is imperative. Changing the oil every 800 hours of operation or in accordance with the manufacturer’s guidelines is recommended. This practice ensures optimal exciter performance, minimizing the risk of costly breakdowns and repairs.
Using the manufacturer-specified oil type is critical for effective lubrication and protection of the gearset and bearings within the vibrating screen exciters. Manufacturers select oil types tailored to their equipment’s specific needs, and deviating from these recommendations can jeopardize performance and longevity, potentially leading to damage.
When replacing oil in vibrating screen exciters, proper procedures must be followed to ensure complete drainage of old lubrication. Start by opening the drain plug to allow the exciter to fully empty the oil. In some cases, releasing pressure by opening the fill plug may be necessary for thorough drainage. Thoroughly cleaning and securely fastening the drain plug before adding fresh oil is essential to maintain the system’s integrity.
Elevated temperatures within the exciter housing during operation serve as an indicator of required oil changes. Exhausted or degraded oil loses its lubricating properties, causing increased friction and heat generation.
Operating exciters with depleted oil pose a significant risk to the gearset and bearings, potentially resulting in costly repairs and downtime.
Suspension springs
Suspension springs play a pivotal role in vibrating screens, mitigating g-force vibrations and preventing their transmission into the screen base and plant structure.
To ensure efficient operation and prevent premature wear, regular inspection and maintenance of these springs are indispensable. Routine inspection of the suspension springs and immediate replacement upon detecting any signs of breakage are advised. Continuous vibrations and heavy usage can lead to wear and breakage over time.
Regular inspections enable operators to identify damaged or worn springs promptly, ensuring optimal performance.
Cleaning the area surrounding the suspension springs is equally important. Accumulated material can prematurely wear the springs and impede their proper function. Regular cleaning prevents such issues, ensuring that the springs remain free of debris or substances that could compromise their performance.
When replacing suspension springs on one corner of the vibrating screen, it’s imperative to replace the springs on the opposite corner simultaneously. This practice maintains screen balance and stability, guaranteeing proper support and function. Pairwise spring replacement ensures continuous performance as intended.
If suspension spring failures occur frequently, the levelness of the plant’s floor steel should be examined. Over time, ground settling or consistent vibration forces may lead to uneven floor steel. Such conditions can adversely affect vibrating screen performance and cause increased wear on the suspension springs. Operators can assess floor steel levelness using tools like a transit or water level to identify and rectify any issues.
Final thoughts
To maximize the performance and lifespan of vibrating screens in aggregate processing, regular inspection and maintenance are paramount.
Implement a consistent inspection schedule and provide operators with proper training on essential maintenance tasks to minimize downtime and optimize performance.
By adhering to these tips presented in this article, operators can achieve efficient operation and extend the vibrating screens’ longevity.
Raymond Pietramale is director of marketing and brand management at Elgin Separation Solutions.