The key to optimum screening is maximizing capacity without losing quality and efficiency.
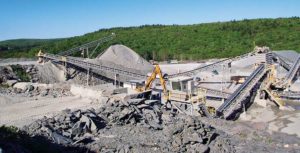
“Avoiding costly bottlenecks requires the right screening strategies,” says Joe Schlabach, vice president of marketing and sales at Deister Machine Co., a manufacturer of vibrating screens and feeders.
Schlabach stresses that vibrating screens must be properly designed and engineered, operated under defined parameters and correctly specified and applied right from the start. Maximum screening efficiency results from proper adjustments in speed, stroke, rotation direction and angle of inclination.
Each of these parameters affects an important facet of screening – proper depth of bed – which means the material bed should not reach a depth that prevents undersize from stratifying before it is discharged.
“Loading screens too heavily is a common practice, and one which leads to carryover problems and less screening efficiency,” says Schlabach, who details several bottleneck challenges in this article along with strategies that were implemented to deliver the desired results.
High-capacity design
According to Schlabach, one Maryland operation sought additional crushing capacity and screening circuits that could efficiently handle the load. The operation’s tertiary screening circuit presented considerable screening bottlenecks.
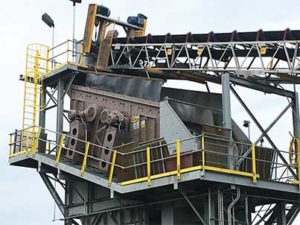
The plant utilized a combination of four vibrating screens to size and separate material discharged from both a standard and a short head crusher. Its 6-ft. x 18-ft. high-frequency screens were set up to separate dry screenings prior to introducing material to twin three-deck wash screens.
The high-frequency screens delivered inconsistent performance and were not designed to handle the larger fractions, causing a carryover problem that sent all crushed material to the twin wash screens. That meant all crushed fines were also sent to the wash screens, requiring two fine material double screw washers to process the water and fines volume.
Extensive washing created a pond fines issue, and the site had limited retention pond space. In addition, the oversize material from the wash circuit recirculated to the tertiary surge pile, creating a wet feed for the crushers.
Also, production capacity was severely limited because the circuit was initially designed for a finer separation. It could not facilitate increased load volumes.
After adding considerable crushing capacity to the secondary and tertiary circuits, the operation consulted with Deister on screening circuits that would handle the load. Ultimately, the operation replaced four vibrating screens and a wash screw with two screens – one on the dry circuit and the other on the wash circuit.
The operation installed a new three-deck, 10-ft. x 20-ft. screen in a new dry tower to receive material discharge from all three crushers, as well as the desired feed from a scalping screen that bypasses the secondary crusher. This allows a dry separation that sends oversize material back to the surge pile while removing the #10 dry screenings from the circuit prior to washing. The screen maximizes capacity, handling between 1,200 and 1,400 tph.
The results are greater efficiencies in labor, maintenance and overall productivity. The operation is realizing greater control, too, as it is efficiently pulling out the fines that do not need to go to the wash tower.
With the old plant, the operation had to deal with all of the washout and settling ponds. In the past, the operation was cleaning out the settling pond every week. Now, the operation cleans the settling pond once a month.
According to Schlabach, the operation can now put all of the product across the dry screen and through the crushers. In the past, the operation could not put crusher run in the plant, as it couldn’t screen it out. Now, it can process the crusher run, boosting the volume through the plant.
Custom engineering
To increase capacity and throughput at a New Jersey quarry, another operation upgraded its screening circuits by replacing older single-drive units with new dual-drive screens. The units were customized specifically for the plant and its applications.
Four new Deister finishing screens were added – three triple-deck 8-ft. x 20-ft. units and one single-deck 8-ft. x 20-ft. screen.
Screening upgrades were required, as the operation’s previous single-drive screens couldn’t handle the tonnage and keep a consistent stroke. The operation was getting a lot of carryover. It was tough to get material clean on the smaller-opening screens in particular, and the inconsistency could put the product out of spec. This cost some tonnage.
With the four new finishing screens, improved gradation is one of the most favorable results. The operation can use smaller openings in its screens and still get the finished material as clean – if not even cleaner – than expected. That gives the operation more options in terms of the cuts it can make, and it can adjust the screen to really fine-tune the gradation.
The bottom line: the product is cleaner and more consistent, and the operation is getting consistent tonnage across the screen.
Five additional screens were also added to the primary and secondary circuits, which include four triple-deck 8-ft. x 20-ft. units and one single-deck 7-ft. x 20-ft. screen – again, all dual-drive units replacing less efficient single-drive models. Plus, the upgrade to triple-deck screens, particularly in the primary position, allows increased throughput, as the middle deck acts as a “relief deck” between the top and bottom deck, preventing the bottom deck from overload.
Importantly, each new screen is designed as a custom fit within the plant to meet the exact specifications of the discharge and feed chutes. All of the screens were delivered on bases that would sit directly on top of the existing structures for a “pick and place” retrofit installation.
Strategic specification
For a Pennsylvania aggregate operation, the mission was boosting throughput, increasing overall screening efficiencies and maintaining stringent product specifications. To achieve this, the plan is capitalizing upon the performance of five existing screens – and adding four new screens in strategic locations.
The first initiative was the replacement of a secondary 8-ft. x 20-ft. double-deck scalping screen with a new 8-ft. x 24-ft. double-deck screen. After upgrading the secondary crushing circuit from a cone/vertical shaft impactor to a cone/cone setup, more screening capacity was needed. A double-deck wash screen was replaced with a new 8-ft. x 20-ft. triple-deck wash screen for the output of three different product specifications.
However, the most important upgrade was the replacement of older, single-deck high-speed screens with two 6-ft. x 12-ft. double-deck high-speed screens. The high-speed screens clean the material before it reaches the finishing screens.
The high-speed screens pull out the 1/8-in.-minus sand product before the material is conveyed to dual 8-ft. x 20-ft. triple-deck finishing screens. The high-speed screens run in excess of 1,200 rpm and operate with a very short 1/4-in. stroke and at a steep incline of up to 30 degrees. The double-deck approach on the high-speed screens allows greater stratification between the decks. The load is reduced on the bottom deck, which, in turn, allows more open area for greater throughput.
Seek expertise
Remember, it can be helpful to work closely with your chosen manufacturer. Tapping into solid screening expertise streamlines the process while ensuring sound operation and a solid return on investment. As Schlabach describes, screening is both art and science.
“The science is proper material stratification – and the art is fine-tuning screening circuits to maximize capacity and efficiency in a given application,” he says.
Carol Wasson is a veteran freelance writer for the aggregate and construction equipment industries.