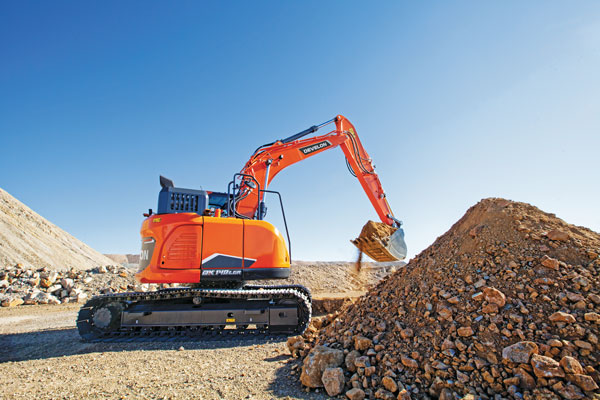
Working at quarry operations in the summer months poses distinct challenges.
Construction equipment must handle tasks like drilling, blasting and moving material on these sites.
Equipment is subjected to extra stress due to high temperatures, dust and uneven terrain.
Inadequate maintenance in this environment can accelerate wear and result in unplanned downtime, necessitating repairs and compromising safety for operators and others in the quarry. Given the demanding nature of these tasks, it’s essential to mitigate potential hazards through proactive maintenance practices.
Here are a few key summer maintenance considerations for crawler excavators operating at quarries.
1. Maintain the cooling system
The cooling system is essential for regulating an excavator’s engine temperature and preventing critical components from being damaged by excessive heat.
“Radiators should be inspected for damage, corrosion or debris buildup that could obstruct airflow and cooling efficiency,” says Jacob Sherman, product and dealer marketing manager at Develon. “Coolant levels should also be monitored regularly and topped off as needed with the appropriate coolant mixture recommended by the excavator manufacturer. The coolant should be at the correct concentration to provide adequate heat protection, especially in regions where temperatures can fluctuate.”
Inspect an excavator’s hoses for signs of wear or damage to prevent coolant leaks that can lead to overheating or engine damage. Any worn or damaged hoses should be replaced.
Cooling fans and fan belts should also be checked regularly to ensure optimal performance.
“Over time, fan belts can become worn or loose, affecting the efficiency of the cooling fan,” Sherman says. “Replacing worn fan belts and adjusting belt tension as necessary can help prevent cooling system failures and ensure consistent airflow.”
Monitor engine temperature gauges and be aware of signs of overheating, such as steam or coolant leaks. In the event of such indicators, shut down the excavator and allow it to cool down before addressing the issue.
As a general rule, it’s advisable to wait at least 30 minutes to an hour to allow an engine to cool down sufficiently.
2. Minimize dust levels
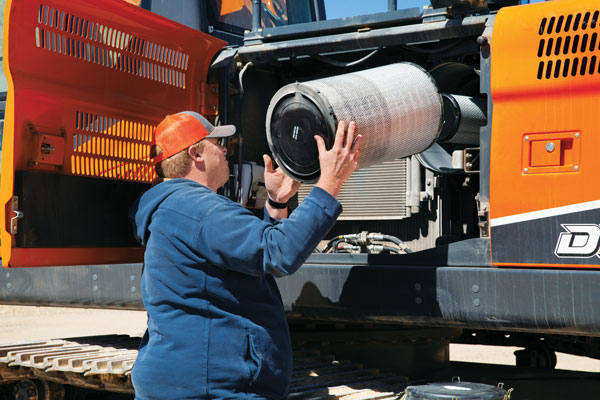
Dust is a common occurrence at quarries, posing a risk of buildup that can impair the performance of excavators and their internal components and systems.
“Clean the excavator’s air filtration system regularly to help prevent dust buildup and maintain optimal airflow to the engine and other critical components,” Sherman says. “Be sure to inspect air filters, air intake systems and engine compartments to prevent clogging. If these systems become clogged, it can lead to reduced engine performance, overheating, increased fuel consumption, potential damage and safety risks.”
Dust accumulation can adversely affect bearings, joints and other moving components, resulting in increased friction, heat and accelerated wear. To prevent the accumulation of dust particles, it’s important to lubricate moving parts regularly.
“Applying appropriate lubricants and greases according to the manufacturer’s specifications can help minimize friction, guard against corrosion and prolong the service life of critical components,” Sherman says. “Adhering to recommended lubrication schedules is essential and, when necessary, utilizing high-temperature grease can further extend the lifespan of components.”