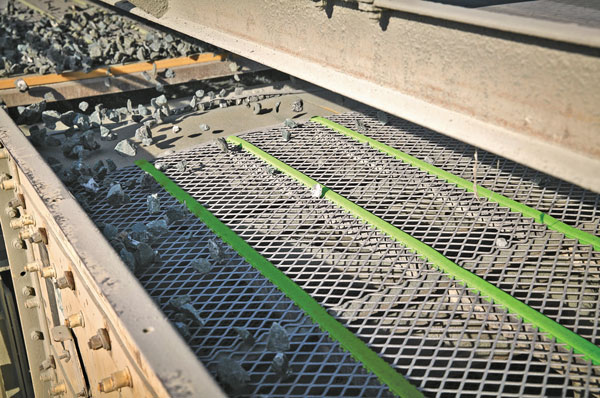
Many synthetic panels are made up of relatively soft polyurethane, which means they can be up to 10 decibels quieter than wire screens. Lower noise levels reduce occupational noise exposure for plant personnel and the associated potential for hearing damage.
One downside, however, is that less noise can mask underlying performance and maintenance issues. Tears in the panel are not visible, which means performing quick visual checks for them is not feasible.
Also, these tears can lead to larger, less precise openings over time and, therefore, out-of-spec, potentially contaminated material coming through. Operators are only alerted to an issue when performing an assessment of the panels or when the opening is large enough that the material starts to flap when in motion. And at this point, the quality of the aggregates may already have been significantly impacted.
In contrast, while it’s noisier, high-vibration screen media only requires a visual check each shift to assess any issues.
A tailor-made approach
There is no one-size-fits-all approach when it comes to screen panels and fit.
Sizing that is even a fraction of an inch off can have tons of impact in terms of quality screening. While polyurethane panels come in a variety of options for different screening needs, custom-designed high-vibration screen media can often ensure a perfect fit and more precise screening.
Whereas some custom high-vibration options are suitable for high-impact, heavy-material applications that still need a good amount of open area, others are ideal for low-impact, finer or more sticky material.
Despite their different uses, each custom-fit option is designed to strike the right balance of wear resistance, throughput, and blinding and pegging resistance to meet processing demands.
The bottom line
Just as drivers need high-quality tires that offer excellent tread for enhanced traction and safety, so too do aggregate operations need high-performing screen media that provides higher throughput alongside reduced downtime, maintenance and replacement costs.
When it comes to making the best purchasing decision for your operations, added value should take the place of cost per ton. At the outset, polyurethane may seem like a cheaper alternative to many premium high-vibration wire products. In the long term, customized high-vibration screens offer a more cost-effective and high-yield solution.
It may also be that a combination of both options can help you maximize production while retaining quality. Partnering with an OEM-certified technician is a cost-effective first step toward identifying problems and solutions and selecting the screen media that fits the application and the different phases of screening in your operations.
Serge Raymond is product specialist at Major.