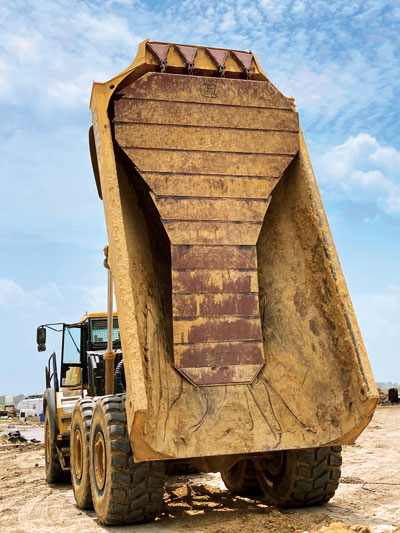
We all know what it feels like to be put in a sticky situation.
Most of us easily relate to scenarios with too many moving parts, unexpected or unforeseen challenges, and an increase in pressure to still complete all tasks with unrivaled efficiency.
For construction operations, a sticky situation – literally – is carryback. Operations face more pressure than ever before to increase efficiency to meet rising demand across the world. Carryback works against that goal by reducing payload in the haul truck, as residual material is left sticking to the sides and bottom of the truck and decreasing haul capacity for subsequent loads.
Custom haul truck solutions, however, offer an effective solution for carryback while addressing other operational inefficiencies.
The obstacle of carryback
Carryback creates a variety of problems when overlooked.
As material sticks to the sides and beds of haul trucks, piling up load after load, operations suffer from decreased efficiency in two ways.
First, each trip sees a reduced payload as the truck hauls the same material back and forth on every pass, reducing the overall capacity. Operations can accumulate up to 10 tons or more of material carryback a day.
In some cases, this means 10 percent of each load is lost. When considered for just one load, this may seem small. But when operations look at the big picture, this 10 percent can quickly add up and result in more hauling, an increase in fuel costs, additional wear and tear on equipment, and, ultimately, a decrease in profit.
Second, when the cost of carryback becomes too great, the operation must shut the haul truck down to manually remove the built-up material – once again hampering productivity. When this occurs, it requires operations to divert an excavator and a handful of crew members to shovel the raw material out of the truck – a dangerous and tedious process that can take at least 20 minutes several times a day.
This, of course, equates to lost truckloads of payload. For maximum efficiency, every minute matters, and the ones that are lost can quickly turn into an expensive problem.
Fortunately, viable options exist to eliminate carryback. Two haul truck solutions that address carryback are load ejectors and rear-eject bodies. When weighing the options, one consideration is whether carryback is the primary issue an operation wants to address or if it is wants to improve efficiency in other ways.
Whether choosing load ejectors or rear ejects, it’s important that the solution not include a “one-size-fits-all” approach, but rather one that takes into account the full picture and is tailored to the operation to achieve better productivity, safety and profits in the long run.
Load ejectors
Load ejectors installed in existing haul truck bodies provide an effective solution for tackling carryback.
Specifically engineered to address the problem of sticky material such as fly ash or clay dirt clinging to certain areas of an articulated or rigid-frame truck’s body, load ejectors feature tailor-made designs to precisely fit an operation’s make and model of truck with a keen focus on the main areas prone to buildup.
Material buildup typically begins at the front slope to floor transition of the body, and it creeps down the floor, up the front slope and up on the body sides as time progresses.
Load ejectors clear out material before it can build up on the sides. The design of each load ejector consists of a series of overlapping, jointed plate lattices – comparable to mini blinds in a window – that attach to the top of the front slope plate and drape down the truck body floor.
When the body raises to dump material, the load ejector plates slide down and out of the body, hanging vertically on chains, to remove the sticky material. The ejector hangs away from the floor, so the process can be compared to picking up a kitchen rug and shaking it out.
The carryback material falls off the load ejector through gravity and motion as the truck bed raises. As the truck body lowers, the load ejector plates automatically fall back to their default position and lay atop the body floor of the truck, allowing the full capacity for the next load.
Operations boost haul capacity even more by pairing load ejectors with a tailgate. While sometimes viewed as a simple piece of equipment, a tailgate provides a better loading target and additional capacity by closing off the back of the truck. This allows operators to fill haul trucks up to their full rated capacity – typically 10 to 15 percent more than the amount filled without a tailgate.
Rear ejects
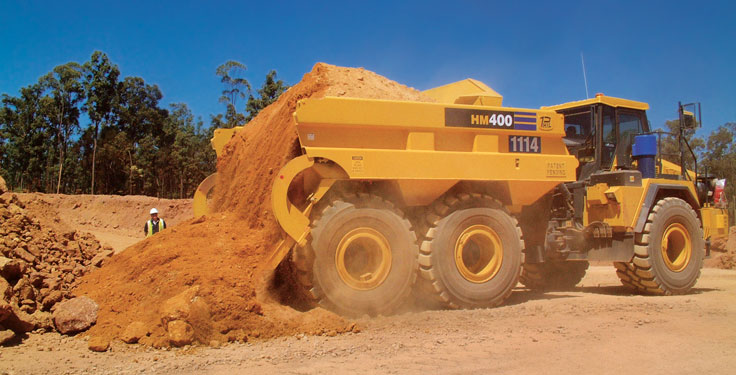
For those operations with concerns that include carryback but go beyond it, another custom solution provides an even more advanced option.
Rear ejects take the efficiency challenge to the next level. To make an analogy, a load ejector can be compared to a Phillips-head screwdriver. It accomplishes one function – reducing carryback – extremely well, and efficiency improves by using one rather than trying to accomplish the task without the proper tools.
A rear eject would be more like a Swiss army knife. Not only does it address carryback because it includes a Phillips-head screwdriver, but it includes other tools, making it a custom solution to improve hauling capacity, increase safety and stability for off-highway operations, as well as drive overall operational versatility.
Rear-eject bodies are engineered to fit a specific chassis and replace the standard end-dump truck body. A rear eject features an ejector blade that pushes material toward the rear of the truck while the tailgate mechanically lowers, completely ejecting material and virtually eliminating carryback. The truck no longer relies on the force of gravity for dumping, but rather the blade pushes the material out, completely cleans the body and eliminates the potential for carryback.
Rear ejects also enable trucks to haul their full rated capacity, and they improve efficiency in other areas, as well. Operations with traditional end-dump bodies waste time by stopping to raise the truck bed, dumping material and waiting for the body to completely lower back down before driving away.
Conversely, rear-eject bodies dump material while the haul truck continues to drive, as the ejector blade retracts while driving away from the dump site. They also allow trucks to dump on unstable and uneven terrain, including slopes, safely and without worry of overhead clearance. Although the cost of a rear eject is higher, the initial cost is quickly offset by the time savings and additional capabilities the design offers.
Finding a solution that sticks
Load ejectors and rear-eject bodies help operations out of sticky situations. Whether addressing carryback alone or improving haul truck efficiency in other ways, operations can rest assured there are custom solutions to help them improve operational efficiency in their haul truck fleet.
Josh Swank is vice president of sales and marketing at Philippi-Hagenbuch.