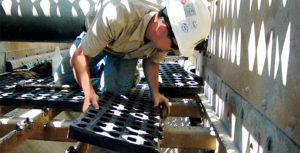
Screening equipment typically does not top the list of hazards workers must be aware of within an aggregate operation.
Still, there are some very real dangers associated with screening equipment that should not be overlooked.
“[Screening] is frequently overlooked as a main source of hazards,” says Alex Caruana, territory manager at Polydeck Screen Corp. “Anytime you’re doing a hazard analysis, your primary goal is to eliminate the hazard at the source, or somewhere along the path or address it with PPE (personal protective equipment).”
Still, PPE can fail if misused, Caruana argues, and workers – even seasoned ones – must remain vigilant to avoid becoming complacent to danger signs that may be evident along a path.
Straight to the source
“You look at most machines, and you are screening partly by gravity,” Caruana says. “The machines are high up.”
Depending on the type of media, change-outs can become challenging tasks.
“Have you ever tried to manipulate a sheet of plywood with somebody?” Caruana says. “Then consider doing it potentially 80 ft. in the air while standing on cross members with something sharp and wiggly.”
This exercise can lead to stress injuries like sprains, he adds, or, depending on the media type, cuts from sharp edges.
“The larger and heavier the media, the more likely for something like that to happen,” Caruana says.
Safety hazards aren’t only present at a top deck, he stresses. Other screening decks present hazards of their own.
“At times you are in a middle deck where you’re in a very tight, confined area,” Caruana says. “That puts you in awkward positions that can result in sprains, strains and the potential for more serious injury.”
According to Caruana, one potential solution here is modular media, whose smaller size allows only the specific worn area of the deck to be changed.
Noise originating from screens is a safety and health factor, as well. Just consider steel screen boxes and screen media and the noise they emit.
“You’re creating a great deal of noise from one of the highest points in your facility,” Caruana says. “It’s audible throughout the area and necessitates hearing protection and secondary measures to protect workers.”
The creative use of synthetic wear liners can lead to a significant reduction in noise, he adds.
“Here’s an interesting case I ran into a few years ago,” Caruana says. “I had an operator who was looking for some synthetic [media] to use as wear liners. The fellow in the nearby enclosed control room was wearing hearing protection. His two-way radio was cranked to the max because his control room was right next to two transfer points that produced tremendous noise.
“Their comment after they applied the synthetic wear liners was that the control room operator noted how he could turn the radio down and actually hear other failures. For instance, if there was a squeaky bearing: he could hear it like a normal person now. You’re not in this ‘war zone’ of production.”
Another safety concern
Another potential safety hazard Caruana addresses is fire.
“Fire is a common concern in my territory,” he says. “The truth is if you put in the wrong type of synthetic media, you can create a combustible situation.”
Say someone is cutting or welding above the screen and a bolt head falls onto the deck below. The bolt head is red hot and it’s packed with energy, Caruana says.
“That can start a fire,” he says. “All synthetics, unless they’re fire retardant, are going to flame. But some will ignite and quickly extinguish while other types will continue to burn.”
By covering synthetic media with plywood or sections of old conveyor belt beneath an area where hot work is taking place, producers can greatly reduce or eliminate the potential for media to catch on fire. Selecting the right synthetic media can also reduce this risk, Caruana says.