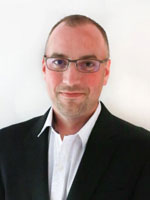
Welcome to the first “Going Home Safely, Every Day” column.
I’m Steve Fuller, and I’ve led operational and safety teams for more than 20 years. I’ve found that a boots-on-the-ground approach to communication is the most impactful. So, check this space out each month for a safety spotlight you can share with those on your team to ensure they’re engaged in their safety culture.
Shifting modes
Let’s tackle seasonal maintenance to start this column off.
In the North, many pits and quarries have been working all season to keep up with customer and internal demands. These put teams into a mode of keeping stockpiles up and keeping up with sales.
When the season begins to relent, winter maintenance usually takes center stage. Whether we know it or not, this changes our perspective from operational to maintenance. And when we change modes, the likelihood for human error increases.
The first item teams should consider when shifting to maintenance is communication. When routines are shaken up, teams should take the time to properly communicate. This can look different, depending on your company and strategy. But it often includes toolbox talks, tailgate talks, daily or weekly huddles, or something similar where teams talk about upcoming assignments, risks and controls.
The key to effective communication is making sure everyone involved is engaged. Don’t just read off assignments and get to work; chat with your team and make sure people understand their work scope, risks and hazard controls.
Most incidents have an aspect of compromised communication. During my time coaching teams in our industry, I’d encourage them to “take five,” meaning take five minutes whenever something seemed off or a work scope changed.
The next thing teams should consider is the safety protocols they may need during maintenance – ones they would not need during regular operations. A slew of new hazards arises when we disassemble, repair, inspect and maintain equipment. This entails confined space protocols, lockout/tagout (LOTO) and fall protection – the big three that presents the potential for the most harm and must be controlled.
Useful acronym
The hazards your team faces will most likely vary. The point is to be cognizant of what new hazards emerge so you can control them.
Often, when I’m in the field, I’ll coach site leaders to remain vigilant of “GEMS.” This is an easy acronym to remember:
• Gravity. Falling from heights – or even tripping from poor housekeeping or ground obstructions – is one common hazard our industry contends with. During seasonal maintenance, sites should check out all guardrails, self-closing gates and walkways to ensure they do not pose a hazard.
If seasonal maintenance requires working from heights, teams should make sure they are protected from falling to a lower level. For example, work out of manlifts with fall protection, use proper staging and, if ladders are absolutely needed, make sure they are used properly.
• Electrical. Maintaining, repairing and upgrading equipment involves controlling electricity. Always follow company expectations on LOTO. The most important aspect of LOTO is to ensure you “test” or “try” to make sure all energy is controlled.
When it comes to LOTO, remember the energy we are controlling may dominantly be electrical. But it can also include pneumatic, stored energy, thermal or any other type of energy that may cause harm.
• Mechanical. Two things come to mind when talking about mechanical hazards in the industry: machine guarding and tool use.
Machine guarding can take a beating, so make sure to bring all of it up to par – and fix any items that may cause problems (i.e., machine guards plugging up).
Additionally, tool use increases during maintenance activities – including using some we may not use during the season. Make sure your team is trained in the tools being utilized and that everyone uses the proper PPE. Most tool use triggers the need for eye/face protection, gloves and potentially hearing protection.
• Space. Confined spaces may need to be entered more in the maintenance season. It is critical to follow the confined space procedures your company has in place. These likely include testing the air, filling out permits and having a rescue plan.
Although some spaces may seem safe at first, the air can be compromised by way of welding, chemical use and grinding when activities are added.
Related: P&Q University Lesson 13: Safety & the Environment
Steve Fuller has worked over the past 20-plus years with a variety of industries – including aggregates – in operational and safety leadership roles. Now representing Steve Fuller Company, he can be reached at steve@stevefullercompany.com.