Three aggregate producers participated in an equipment and technology panel discussion at the 2025 Pit & Quarry Roundtable & Conference in Phoenix. Those on the panel were Duff Quarry vice president Ross Duff, Luck Stone director of engineering and construction Raymond Slaughter, and US Aggregates director of operations and engineering Kristin Sweeney. The discussion here, which took place Jan. 31, was edited for brevity and clarity.
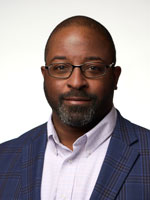
P&Q: It’s been about two years since Luck Stone announced its partnership with Caterpillar to outfit the company’s 777 trucks at the Bull Run Plant in Chantilly, Virginia. Can you give us an update on how that project is going? What have the results been like so far? Are there plans to expand this beyond the Bull Run Plant?
RAYMOND SLAUGHTER: From a learning curve, the feedback that I’m getting from the leadership at the Bull Run Plant is that they’re getting used to it. They’re getting more comfortable with their ability to direct them and set schedules, but we’re still in the early learning phase. We’ll keep expanding on that capability, and I’m sure there will be another opportunity for us as we learn more about them because we have several plants that have larger fleets that would benefit from this type of automation.
P&Q: For the others on the panel, what’s your reaction to what’s transpiring right now in autonomous hauling? Is your company considering implementing autonomous haulers? If not, what are the barriers to entry?
KRISTIN SWEENEY: We’ve looked at semiautonomous – more of a remote control – with the autonomous travel. We were working with a company based in California. It made it all the way through the ROI stage of the operation. At that point, the ROI was ‘break even’ at best.
We’re more based in the Midwest. Our labor rates are not that high compared to some other markets. If you’re in a market with higher labor rates, I think it would make a lot of sense.
The other thing that gave us a little bit of pause was this was third-party aftermarket. We are aware of the inroads Cat and John Deere have made, so we have decided to sort of ‘pause’ our approach and wait for more OEM supply options versus trying to do something that’s custom and add it after the fact.
Really, what it came down to for us is, at the end of the day, when you’ve got a limited bucket of capital and you’ve got something that’s ‘break even’ versus something that’s offering a 10 percent return, it’s pretty easy to decide where to invest my dollars. I’m hoping over time it gets more affordable and we can revisit it.
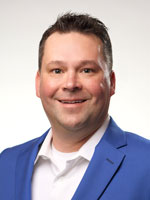
ROSS DUFF: Our company right now is holding tight. We are a small to medium-sized family business with just a handful of locations, so our budget for an autonomous vehicle is not at the scale of some producers.
P&Q: What is next for Luck Stone when it comes to adapting transformative tech like this?
SLAUGHTER: We’re looking at other opportunities around the fleet. One of our missions is to be very customer focused, so we’re looking at the teleop scenario to deal with the in-rush and peaks and valleys in some of our distribution yards that might benefit.
What’s hot for us right now is autonomous drilling. In 2018, we started on a 3D blasting program. A next logical step was to get that information into our drills with the GPS. We’ve been working closely with Epiroc.
In the 2020 to 2022 range, we had several of them running with the GPS. We did see benefits in our plant production. We had better fragmentation. It led to better throughput in our primaries. Our ability to be precise on our base production was very beneficial.
This year, we’ll probably have our fleet of drills running in that form or fashion.
P&Q: Are there any other areas of autonomy – or AI – that your company is looking into or experimenting with? If so, what’s driving your interest?
DUFF: Being that we are a small company, finding a surveyor who had a mining background was difficult. We did some sleuthing and came across DroneDeploy. We started not only using a high-resolution drone – which is nothing groundbreaking, but we added thermal to it.
We were able to see when the crops were off on a greenfield site. We had a rain event, and that allowed us when we did our mine development to determine where to place the plant and what works and what doesn’t. We were able to dictate where we put the utilities. For mine planning, this was awesome.
P&Q: In recent years, there has been an increased push from manufacturers for up-to-the-second data to be available at operators’ fingertips, and for them to be able to see the status of equipment and make decisions from their phone or tablet. What has your company’s experience with this been?
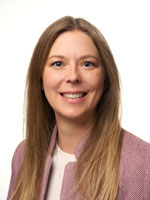
SWEENEY: We’ve been on a maintenance journey for the last couple of years. As an industry, we always used to do winter maintenance. But winters aren’t what they were 20 years ago.
Living in Indiana, we crush right up until the end of the year. But I have plants that didn’t shut down. So, we don’t have winter maintenance. We’ve taken the approach to do the right maintenance at the right time the right way.
If the right time to do the maintenance is in May, let’s plan for it, be prepared and take a week. We’ve seen quite a bit of improvement in overall morale. If I’m going to be at a plant doing maintenance, I’d rather do it when it’s 70 degrees out than when it’s 0.
We’ve really started to change the way we’re analyzing all our historical data and downtime. We’re looking at it to say: ‘What are the gaps? We know it’s broken, but what hasn’t broken, and what is most likely going to fail in the next three to six months?’
Then, we pair this with some continuous monitors of vibration and tension monitors. They’re magnetic sensors. We utilize a company out of Pennsylvania, and these are the size of a golf ball. We’ll stick it on equipment. We utilize them on large-scale motors, large bearings, big gearboxes – anything with a significant lead time that would cause us significant interruption if lost. We also use them in areas where we see frequent failures.
We were using bearings once a month on bucket elevators at one of our industrial minerals plants. We put the sensors in and found two things. One is we were overgreasing, so we changed the lubrication we’re using.
By putting these sensors on, we are now able to do condition-based lubrication. We let the bearing tell us it’s time for some grease, because the temperatures start to tick up. We went from changing bearings once a month to bearings that have been in place for nine months.
Bearings aren’t the most expensive part, but it would take two hours minimum [to address failed bearings]. If the bucket elevator was full when the bearing decided to fail, it could take a whole day.
Safety wise, our guys aren’t exposed to the hazard of having to do that work. Cost wise, it’s been significant. The technology is expensive, but we have saved what has cost us and we’re well into the six figures of savings per location where we deploy that.
Related: Ross Duff shares his market view