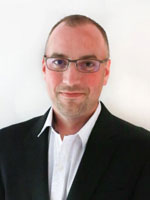
The “two G’s” – guardrails and guarding – are fundamental safeguards within the aggregate industry. If overlooked, these can result in serious consequences.
Crushing plants are continuously exposed to the elements, vibration, and general wear and tear. After a long season, guardrails and machine guards can become compromised.
While you should always be on the lookout for issues involving the “two G’s,” you should make a point to perform a thorough review of guardrails and machine guarding.
Guardrails
The primary function of a guardrail is to keep people from falling to a lower level.
Guardrails are also designed to prevent objects from falling to a lower level. No one, after all, wants to be struck by a falling drill, shovel or tool.
Guardrails are typically constructed of a top rail, a mid-rail and a toe kick, although they can be comprised of extruded metal mesh or another engineered system that meets Mine Safety & Health Administration (MSHA) expectations.
A subcategory of guardrails is self-closing gates. Crushing plants are full of straight ladders to access upper levels. For years, these transitions – from ladder to platform – have been protected by chains or nothing.
A best practice to consider is adding a “self-closing gate” to a transition. This helps to engineer out the human element of having to reinstall chains to protect falls to a lower level. Over the past few years, these have become widely available from industrial safety suppliers.
Machine guarding
Rotating, crushing and pinching are the most common hazards that machine guards are used for. They create a barrier between humans and hazards.
Be sure to protect people from both unintentional and intentional contact. Newer equipment will typically come with manufacturer-provided guarding, although the incidents that occur involving machine guarding are typically severe.
Things to consider
If guardrails and machine guarding are fundamental – and should always be in place – then why are they on the frequently cited standards lists for MSHA and the Occupational Safety & Health Administration?
The answer here is olfactory adaptation, a phenomenon that occurs when people become “nose blind” to their surroundings.
Think of it this way: Can you smell your own house? You likely can’t, because you are exposed to it every day. But if you go into someone else’s house, I’ll bet you notice the nuances to their home – the good and the bad.
The same thing happens in our facilities: When you see the same thing every day, your senses can drift. Over time, small changes can be missed.
This is why getting outside opinions can help a site “see” things they have overlooked – like missing guardrails or machine guarding. This is also why MSHA can pick up on things that were seemingly right under our nose.
Final thought
I encourage you to share this article with your operational teams. Ask your teams to “find it and fix it.”
The end of the year is a great time to clean up items that may have been compromised. That way, you can start 2025 with a clean slate.
Related: Safety hazards to watch for during seasonal maintenance
Steve Fuller has worked over the past 20-plus years with a variety of industries – including aggregates – in operational and safety leadership roles. Now representing Steve Fuller Company, he can be reached at steve@stevefullercompany.com.