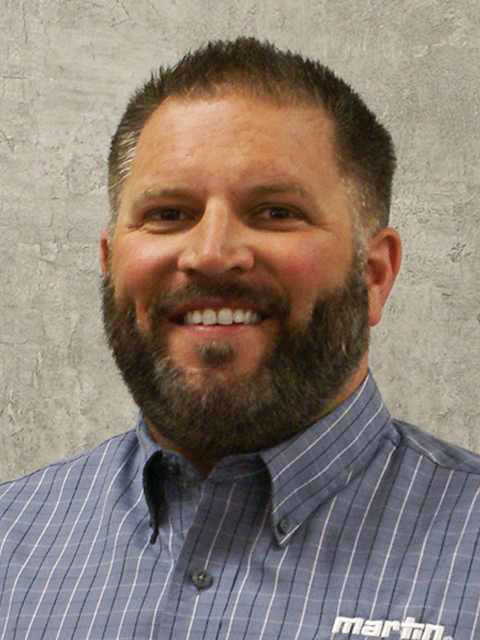
Safety should be at the forefront of everyone’s minds during long outages.
Conveying systems should be clear of all material, and lockout/tagout procedures should be observed. Test all safety devices – including stop switches and start-up alarms – and inspect conveyor guarding for broken latches or holes in the mesh.
Dust is a major concern across all bulk handling industries, so downtime provides an excellent opportunity to examine skirtboards and chutes for proper sealing. This ensures a controlled flow of turbulent air-carrying dust through the discharge and loading zones of belt conveyors, which, in turn, reduces emissions.
An experienced mine leader once told me: “If we’re not running, we’re training.” Training and development of your staff in preparation for spring might be the most beneficial downtime activity. This is particularly critical if an outage involves equipment upgrades or system design changes. Downtime is also an opportunity to review any Mine Safety & Health Administration rule changes.
Before start-up in spring, inspect the structural alignment of all belt conveyor systems. Ground freezing and thawing can impact belt tracking. Wear parts such as rubber skirting that seals transfer chutes against dust and urethane primary cleaners that scrape carryback from the belt should be closely inspected.
Replace worn components right before start-up rather than at the beginning of an outage. This ensures freshness of the wear part for optimum performance.
Conveyors are the sum of the parts. Communicate with service providers and manufacturers, and only partner with companies you can rely on to ensure each component will start up in spring safely.
Related: Conveying the importance of keeping belts clean
Jerad Heitzler is program manager and lead instructor for Martin Engineering’s Foundations training workshops.