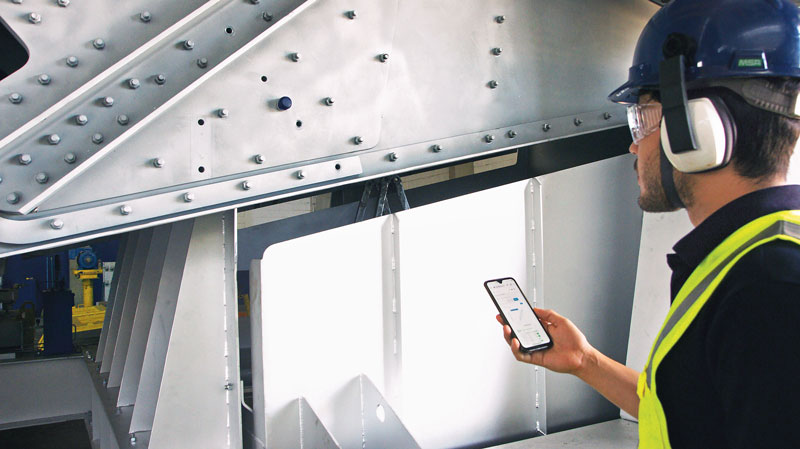
Many companies have thrown their hat in the ring with a condition monitoring system to gain the business of producers.
Some of these companies specialize only in technology with no direct aggregate or mining connections. Others are OEMs that serve the industry but have limited coverage or service capabilities after initial installation.
Those who rise above are manufacturers with a complete package: the equipment and extensive industry knowledge, an experienced team that offers insight and service to customers, and a condition monitoring system with the features those customers need to stay competitive.
Part of the value of condition monitoring systems is in the service producers receive from OEMs. Even the best systems require a human element when questions arise. Considering the history and experience of a manufacturer when selecting a condition monitoring system can save time and prevent future headaches.
Start by looking at whether the company has industry experience. Then, determine how long they’ve been involved in the industry, what their customer service commitment is like and their territory coverage.
Having a deep bench and industry expertise is half the equation, but the technology and condition monitoring system itself plays a vital role, as well. The best manufacturer will not just sell you the system but will partner with you to offer a comprehensive evaluation experience for your production plant.
In these cases, an in-depth inspection can be provided to thoroughly assess the efficiency of your operation. Diagnostics are often the first step, and this can involve impact tests, vibration analysis and condition monitoring.
Impact tests ensure each machine is properly calibrated to avoid operating in resonance, which can diminish productivity, incur damage to vibrating screens and pose safety risks. Vibration analysis examines the real-time health of vibrating screens by detecting irregularities.
Condition monitoring elevates these results by not just identifying and fixing current issues, but emergent ones. The remaining steps of the inspection can involve using the manufacturer’s expertise in processing equipment, engineered screen media, original parts, rebuilds and upgrades, services, plants and process engineering to inspect customers’ screening processes in order to recommend best practices for processing proficiency.
Don’t let production problems boil over
While a pot on the stove does require an occasional glance, mineral processing equipment needs more immediate attention.
Smaller issues like wear or damage to a vibrating screen that are not caught quickly can lead to bigger production headaches – and losses – later on. This is why monitoring systems in line with the latest industry advancements in smart technology are vital for the health of any efficient operation.
Finding the right system and manufacturer to partner with can provide the strongest ROI and ensure keeping up with – or beating – the competition.
Thiago Henrique Buoso is a project and sales engineer in Haver & Boecker Niagara’s Diagnostics & Aftermarket Department.