Editor’s note: The following is a selected portion from the upcoming 2025 Edition of the Pit & Quarry University Handbook. The full handbook is slated for release this November, at which time additional content will also be published online. Be sure to check back for more content as it’s made available!
Efficient material handling is essential to maintain productivity and profitability in the construction aggregate industry.
Conveyor systems, which automate the movement of materials like crushed stone, sand and gravel, play a critical role in streamlining operations from extraction to processing and, eventually, to transport.
This beginner’s guide explores the key types of conveyor systems used in aggregates and how they ultimately contribute to operational success.
Advantages of conveyors
Handling large volumes of materials efficiently is central to the production of aggregates.
Whether transporting raw materials from a quarry to a processing plant or transferring crushed stone to a stockpile, conveyors offer advantages over manual or vehicle-based transport.
Conveyors provide continuous material flow, minimizing interruptions and production bottlenecks. They are also more cost-effective compared to rolling stock methods of material handling, as they reduce the need for trucks and heavy equipment, lowering fuel and maintenance costs.
Moreover, conveyors enhance workplace safety by eliminating the need for workers to manually move heavy materials, reducing the likelihood of accidents.
Additionally, conveyor systems are more environmentally friendly than truck transport, producing fewer emissions and less dust.
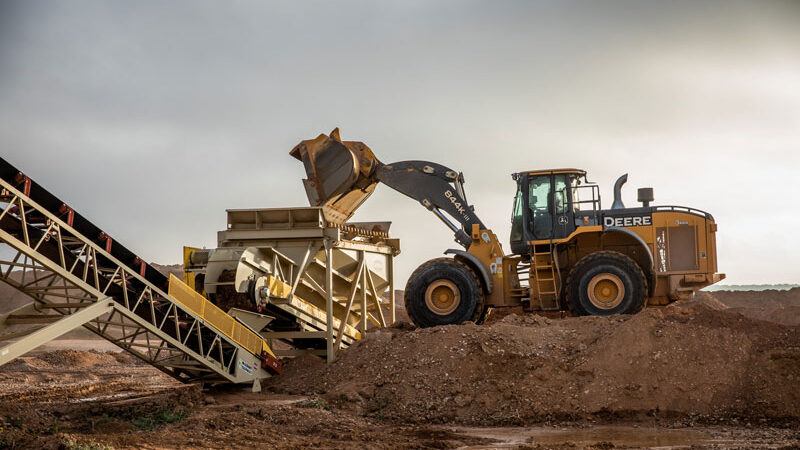
Common conveyor types
Several types of conveyor systems are used in aggregate operations, with each serving specific functions based on the nature of the material at hand and the layout of the site. Let’s explore the most common conveyor types:
1. Feed conveyors. Feed conveyors are typically positioned at the beginning of the material handling process. They transport raw aggregates from hoppers or bins to the initial stage of processing, such as crushers or screens.
Designed to handle heavy loads and large volumes of material, feed conveyors are the first step to ensure a consistent flow into processing equipment, preventing delays or downtime in operations.
2. Transfer conveyors. Transfer conveyors are essential to move material between different stages of the production process, acting as links between feeders, crushers, screens and other processing equipment.
Their role is to keep material flowing smoothly through each step, enabling a seamless transition from one piece of equipment to another. Transfer conveyors come in various lengths, configurations and mobility, depending on an operation’s specific layout.
3. In-plant conveyors. In-plant conveyors are used within processing plants to transport material between equipment and various stages of production. These conveyors are typically shorter, designed to fit into the plant’s layout and ensure efficient internal movement of materials.
In-plant conveyors are vital to maintain a streamlined operation within the processing plant, helping to move materials smoothly from one processing stage to the next.
4. Overland conveyors. Overland conveyors are used for long-distance transport of materials, often from the extraction site to a processing plant or stockpile. These conveyors can span several miles, and they’re ideal to move large volumes of material over varying terrain types.
Overland conveyors, which are also known as groundline conveyors, offer significant cost savings by reducing the need for large fleets of trucks and their associated fuel and maintenance costs. They also provide a continuous flow of material, making them ideal for high-volume operations that require efficient, long-distance transport.
5. Stockpile conveyors. Stockpile conveyors are used to transport processed material from the plant to stockpiles. These conveyors can be either fixed or mobile, depending on an operation’s needs.
Stockpile conveyors are often equipped with pivoting or radial stacking features that allow material to be distributed in even, conical piles. They play a key role in managing and storing processed materials until they are ready for loadout or further processing.
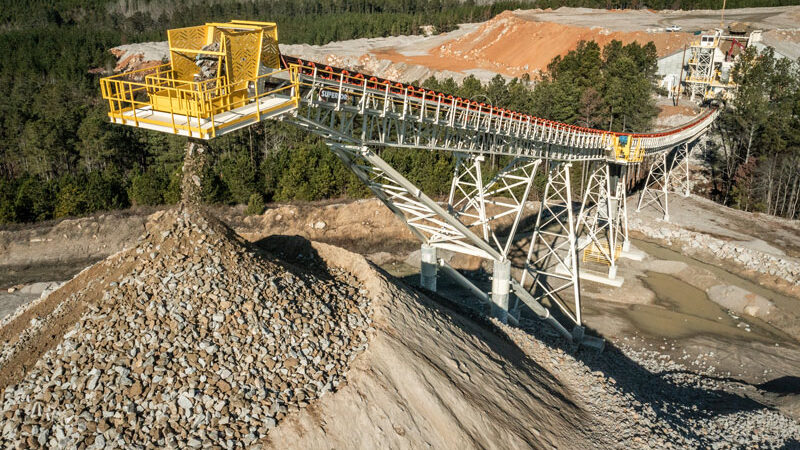
Selecting the right conveyor system
Choosing the appropriate conveyor system for an aggregate operation depends on several factors, including the type of material being handled, the volume of material and the distance material needs to be transported.
Understanding these factors will help operators select a conveyor system that meets their specific needs and ensures efficient, cost-effective material handling.
1. Material characteristics. The size, weight and abrasiveness of the material being transported are crucial considerations. For instance, heavier materials like crushed stone require more robust conveyor systems, while finer materials like sand may require conveyors with specific dust control features.
2. Capacity requirements. The volume of material being processed will determine the size and capacity of the conveyor. High-production operations may need overland conveyors to handle large volumes efficiently, while smaller operations may benefit from shorter in-plant conveyors.
3. Distance. The distance material needs to be moved is also a key factor in selecting a conveyor system. Overland conveyors are ideal for long-distance transport, while in-plant and transfer conveyors are more suited for shorter, intra-plant movement.
4. Flexibility and mobility. For operations that frequently change or move, mobile conveyor systems such as portable stockpile conveyors offer flexibility. This is particularly important for operations with temporary setups or varying production demands.
5. Site layout. Space constraints and the layout of the processing plant are important factors in conveyor selection. In-plant conveyors can be configured to fit tight spaces, ensuring efficient material flow even in plants with complex layouts.
Conclusion
Conveyor systems are the backbone of material handling in the aggregates industry, automating the movement of stone, sand and gravel while reducing the need for manual labor or heavy equipment.
From feed conveyors that initiate the material handling process to overland conveyors that transport material across long distances, each type of conveyor plays a vital role in ensuring efficient, cost-effective operation.
By selecting the right conveyor systems for your operation, you can improve productivity, reduce costs and enhance the overall efficiency of your material handling processes. Whether moving material across a site or stockpiling it for future use, conveyors are indispensable tools for the production of aggregates.
As technology continues to advance, producers can expect further improvements in conveyor systems, making them even more integral to successful aggregate production.
Related: Screening (Part 1) | Pit & Quarry University Handbook
Information for this article courtesy of Superior Industries.