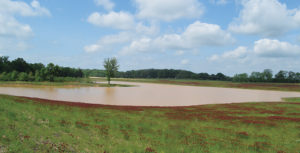
Successfully locating, proving and developing aggregate resources have never been simple tasks.
In fact, depending on whom you ask, these efforts have become monumentally more challenging in recent years for aggregate producers. Spend a day with Alan Parks, vice president at Memphis Stone & Gravel Co., and you’ll quickly gain a basic understanding of the many hurdles producers like him must leap to establish a brand-new site.
“When I first started in this business, we’d hear from producers in Florida and California that it would take 10 years to get a permit,” says Parks, who’s responsible for directing Memphis Stone & Gravel’s mine exploration and planning efforts. “I thought then that I’m glad it’s not our problem.
“Now it is.”
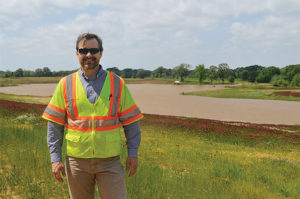
Memphis Stone & Gravel, which supplies a variety of aggregate products to Memphis, Tennessee, and north Mississippi, is by no means the only producer facing local opposition as it pursues growth. As Parks plainly puts it, “something changed” over the last several years with the local permitting process.
Opponents of crushed stone, sand and gravel sites have always been around, Parks contends, and producers faced many of the same issues a decade ago that they do today. But local governments were more willing to work with producers back then than they are now, he says.
Years ago, local officials might have worked aggregate producers over a bit, but producers were ultimately awarded the permits they coveted. The same cannot be said of the permitting environment today.
“There’s been a diversion somewhere,” Parks says.
Perhaps the process is more daunting now because opposition groups can organize easily online. Their reach is greater and voice seemingly larger because of tools that simply weren’t there not too long ago.
The opposing arguments to aggregate sites are really one and the same in every community: that pits and quarries are loud, dusty and create high-traffic environments, and that they have detrimental impacts on water quality and property values.
A producer can enact measures that exceed regulatory compliance requirements and go beyond reason to ease the concerns of those in the community, and a permit still won’t be awarded despite the producing company doing everything – and more – that was asked of it. Months of eagerly awaiting a permit can drift into years or a decade of despair, not to mention hundreds of thousands or millions of invested dollars without the desired result.
Maybe this narrative describes circumstances surrounding your company. It’s certainly a familiar narrative for Parks, who’s experienced a good balance of permitting wins and losses in his career.
“I don’t see signs it’s going to get easier,” he says.
Parks’ mettle, like a number of other producers across the nation, has undoubtedly been tested. Fortunately, some of the more trying times provided him with useful knowledge to prepare Memphis Stone & Gravel for its road ahead with local authorities.
Wins and losses
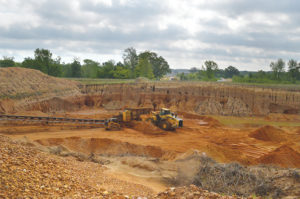
A prospective site where Memphis Stone & Gravel was once approved to mine is a good example of how strenuous the permitting process can be.
As Parks describes, his company pursued a mine permit for a North Memphis metro area property spanning two counties. That meant appealing to two different entities for permits, creating a rather unique situation from the outset.
The company’s permitting pursuit in that North Memphis area is now going on 12 years, and the end isn’t exactly in sight.
“We’ve not given up on it yet but we feel like it’s even more of an uphill battle,” says Parks, who is involved in all phases of Memphis Stone & Gravel’s resource development, including investigation, property negotiation and acquisition, feasibility studies, permitting, public relations and long-range mine planning.
Memphis Stone & Gravel’s now-up-and-running plant in Southaven, Mississippi, on the other hand, is an example of how the permitting process should work – at least in the eyes of an aggregate producer. The two-year-old DeSoto Plant, situated on 178 acres, includes a 25-acre plant site and 108 acres of reserves that can be mined.
The plant replaced the company’s retired Anderson Plant in nearby Nesbit, Mississippi, but the 2016 launch came long after Memphis Stone & Gravel first targeted the property.
The company tried to acquire the property in the early 2000s, but the property’s owners had a partnership opportunity that was expected to put a series of warehouses on the site. No warehouses, however, were ever built there.
When the economy tanked, the warehousing plan was scratched, opening a window for Memphis Stone & Gravel to jump in and, ultimately, provide tax revenue to a budding area south of Memphis.
“We lost it at the beginning to the warehouses because they were dropping big coin to get that land,” Parks says. “There was no way we were going to be able to compete on that. But once the market crashed, they didn’t need the land anymore. The property owners had to rethink it.”
Parks estimates that the DeSoto Plant was awarded its local permit in about 90 days, and its state mining and stormwater permits came in after about nine months.
“The whole process to get it permitted was probably a year,” Parks says. “I won’t say it was easy, but it was less controversial than we anticipated. That’s how it ought to be.”
How drivers affect permitting
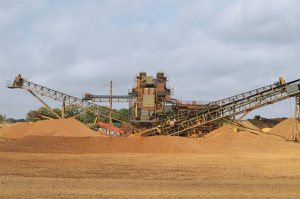
The typical mine permitting process takes a minimum of 12 to 18 months, Parks says. Then again, there are those instances that stretch on for years.
Therefore, it’s vitally important that producers take the proper steps ahead of time to position themselves for success.
“Your reputation has a lot of value in these proceedings,” Parks says. “You’re going to work hard to be a good neighbor. It’s important, too, that you have a record with how you deal with complaints.”
The producers who show how they successfully managed complaints – about noise or dust, for example – will be best positioned for victories.
“Anytime a citizen comes in with a concern, you have to assume that will come up again at a permitting hearing,” Parks says.
Managing complaints and taking action once they come in is easier said than done, and keeping detailed records about complaints and how they were handled is no easy task, either.
Still, it can be done if producers approach complaints systematically. Memphis Stone & Gravel handles complaints in this fashion.
“The scale house operator is usually the first point of complaints,” Parks says. “It’s usually with trucks.”
At Memphis Stone & Gravel, complaints about customers’ drivers are communicated up the chain of command to a plant foreman. A general manager is informed, as well, so the issue can be investigated.
Memphis Stone & Gravel also reaches out to the driver to share the detail.
“When we get a complaint, it becomes a priority,” Parks says. “We have to show we’re going to be a good neighbor.”
Documenting complaints illustrates that Memphis Stone & Gravel not only takes them seriously, but that, in many cases, no violation actually took place.
“We’re trying to get stronger at the documentation of that process,” Parks says. “We make sure the same people are involved.”
These measures are good reactive steps when complaints come in, but Memphis Stone & Gravel is also very proactive to keep complaints about trucks to a minimum. The company rolled out its Good Neighbor Trucking Policy nine years ago to address issues associated with trucks moving to and from its operations.
Responsible, professional and courteous drivers are critical to the success of Memphis Stone & Gravel’s operations, as they are to all aggregate sites. To that end, the company asks all drivers to sign an agreement acknowledging they will comply with rules Memphis Stone & Gravel has drawn up.
“Probably the number one complaint we hear from the opposition is that ‘you don’t own them, you can’t control them,’” says Parks, referring to customer trucks. “This gives you some leverage to say they’re going to follow rules.”
Having such rules in place minimizes the number of complaints Memphis Stone & Gravel takes in and, ultimately, better positions the company for permitting hearings.
“People identify ‘that company’ with Memphis Stone & Gravel,” says Parks, again referring to customer trucks. “We try to explain that your actions affect us down the road.”
The role of reclamation
An aggregate producer’s reclamation record becomes a factor in permitting proceedings, as well. Producers are more likely to be awarded permits if they successfully exhibit how they restored mine properties to effective uses.
For Memphis Stone & Gravel, Methodist Olive Branch Hospital in Olive Branch, Mississippi, and Campbell Clinic Orthopaedics in Southaven are two examples of former mine sites being put to productive secondary uses.
“We’ve had subdivisions built on mined land,” Parks says. “It can all be returned to productive use, and it really is a win-win because property owners benefit. They’re able to recover some value out of their resources; we benefit because we’re able to keep people employed; we supply the construction economy; and when we’re done we get it reclaimed and that land can be returned for future development.”
Memphis Stone & Gravel currently has two ongoing reclamation sites in DeSoto County, Mississippi, where Parks brings decision makers to show them different ways mine properties can be restored.
“We’ll bring the board supervisors out, show them the operation (DeSoto Plant) and then show them what it’s going to look like when it’s done, how the land is returned to other use.”
Memphis Stone & Gravel’s former Love Plant has one site that’s currently being reclaimed for a premium land use. The company partnered with the property owner to develop a Bill Dance Signature Lake that will encourage bass fishing.
The signature lake concept was a new one for a former Memphis Stone & Gravel site that required some additional costs. In the end, though, Parks says that specific project sends a great message to all.
“We had to tweak the way we do things and it slowed the process down a little bit, but in the end we hope it’s worth it because of the tangible value that it’s going to give to a property owner,” Parks says of the lake project. “It says, ‘Hey, if you do business with us, this is what you can end up with.’”
Successful reclamations can lead to future mine permits, too.
“A lot of it is educating the public and board members, and opening up our facility to young people,” Parks says. “We notice there is a lot of fear and anxiety about these future operations, but we know we can be successful.”