Maintaining air breathers is more important than you think.
Ignoring air breather maintenance can lead to a nasty situation, which can be described as lubricating your crusher with “sandpaper-laced” oil. Superior Industries’ Curt Theisen, for example, advises operators to inspect air breathers weekly, as well as clean out dirt and debris. Then, replace air breathers with a new one every month or two.
“Unfortunately, the air breather is a commonly neglected component,” says Theisen, who serves Superior as crushing technical support engineer.
Theisen is part of Superior’s rockface to loadout solutions team, helping producers to achieve greater efficiencies throughout their plants. With cone crushers, Theisen says proper air breather maintenance is one key to maintain effective performance.
At a recent crusher service training class, Theisen says a participant wondered why his facility consistently had problems with dirty oil in the crusher lube system. The participant swore up and down that his crew was managing everything on the maintenance checklist.
But when a fellow trainee offered to look at the crusher, it took only seconds for him to say: “I can tell you right now that you haven’t been checking your air breathers.”
The trainee pointed to the accumulation of thick, hardened dirt and debris sitting on top of the air breather itself. Obviously, no one had removed the air breather cap to inspect it in quite some time.
Lesson learned.
Air breather 101
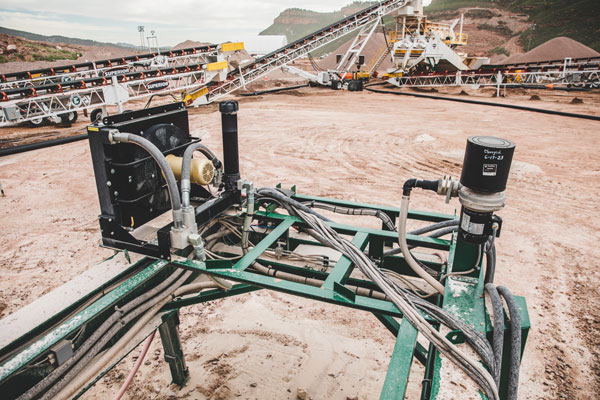
According to Theisen, the countershaft box air breather and the oil tank air breather work together to maintain atmospheric pressure in the crusher, as well as in the ancillary lube and hydraulic units.
Their proper operation generates a positive airflow through the machine, keeping dust and debris out and away from the head sealing arrangement.
If a crusher runs with a dirty air breather, that positive air flow becomes a negative air flow that sucks dirt and dust into the machine, causing potential contamination to the head seals and lube drainage line.
With dirty oil in the system, expensive internal components such as bronze bushings and crusher bearings will incur premature wear and potential failure.
Along with a weekly air breather inspection, Theisen advises operators to take an oil analysis sample after every 200 hours of crusher operation. If a high amount of silica is present in the oil, he says it is likely there will also be a higher content of tin, lead and copper, as those are the three materials contained in a bronze bushing.
Preventive maintenance
Because the air breather is out of sight, operators often forget about it.
Sometimes, air breathers are in enclosed areas, like behind a door. But make sure air breather inspection is on your mental checklist, and take the necessary time to complete the task. The application and environment will determine how often an operator replaces an air breather.
Dry, dusty applications are the hardest on air breathers. If a crusher has a very tight discharge area, such as on a portable plant – or if the crusher is running at an extremely low rpm – an operator may want to add a blower with an air breather.
In any event, don’t let the often-forgotten air breather remain out of sight and out of mind.
Carol Wasson is a veteran freelance writer for the aggregate and construction equipment industries.