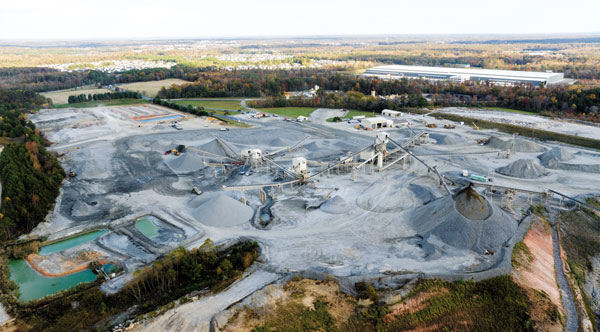
Chris Branham, a pit foreman at Luck Stone with 11 years of service, cites an array of improvements – including drilling and blasting accuracy, reduced oversized material, better floor conditions, increased safety, reduced wear and tear on equipment, and increased production.
The SmartROC D60 with HNS decreased load time by 21 seconds, totaling 2.5 hours per week. The black belt went from 18 percent to 13 percent in the pit, and the overall tons per hour run increased by 114 percent.
Compared to manual methods, 17-year veteran Joe Palmer, a senior blasting technician at Luck Stone, says the rig provides more accurate measurements on the face and in designing shots – as well as while drilling to hit the precise azimuth needed. Between the use of drones, digital photos, computer-planning and GPS-guided drilling, the whole process was transformed to fit on a thumb drive.
Luck Stone blasting manager George Field, a 24-year employee, says the system “makes the job easier by giving the blaster quite a bit of confidence” thanks to the precision in lining up the shot. David Harper, a pit lead manager at Luck Stone who also has 24 years of service, says the HNS helps to execute accurate burdens on the face.
According to Epiroc, the SmartRoc D60 had a trickle-down effect for the entire operation. Griffin Lober, a Luck Stone pit loader operator, says he’s seen significantly more consistent diggability, less oversized material, reduced cycle times, better truck flow, higher production, smoother treatment on equipment, and an easier and more productive day overall.
What’s next
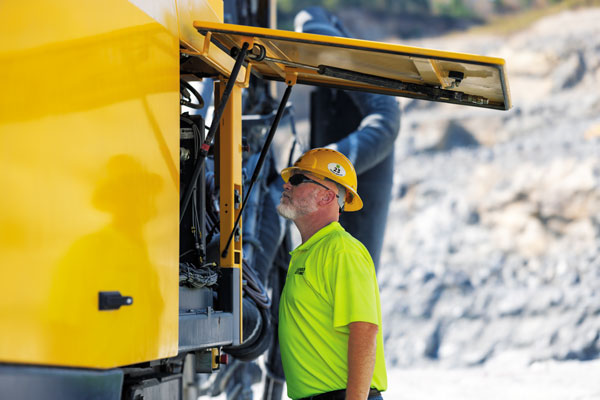
As the market marches toward more automated, autonomous and smart equipment, Scott and Shawn Miller, brothers and co-owners of Northern Virginia Drilling, double down on the need for technology – and not just in quarries and mines, but across public and private construction.
Thanks to the results at the Spotsylvania Plant, the SmartROC drills with HNS are now capturing MWD data that will enable Luck Stone to do further analysis and continuously improve its drilling and blasting processes.
In fact, Luck Stone is already making plans for taking Epiroc-powered machines into more hazardous highwall conditions and difficult blast zones thanks to the MWD data, which includes multiple readings in every drilled hole, capture of the penetration rate of the drill bit, feed pressure, rotation pressure, flushing air pressure, and calculated rock hardness.
End of day
When 4 p.m. arrives, the hum of the drill slows and then stops. Stewart powers off the rig control system, performs his safety checks and climbs out of the climate-controlled cab. It’s time to rest and start again the next day.
Information for this article courtesy of Epiroc.