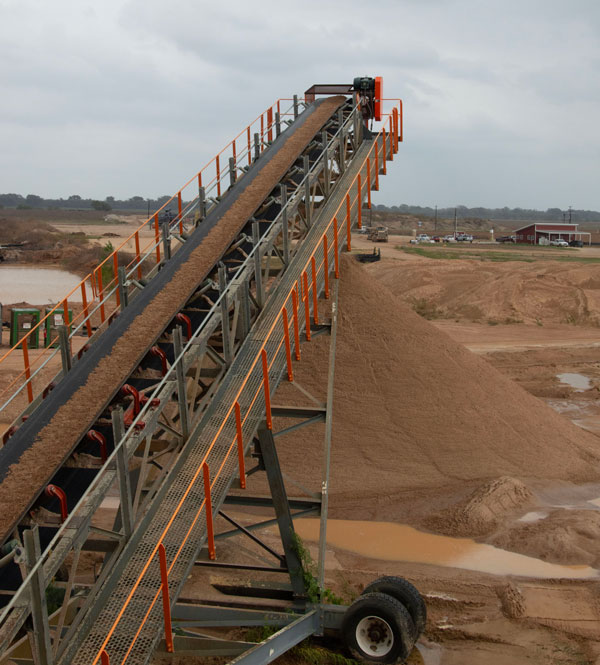
Another vendor who was instrumental to the full-plant arrangement in Caldwell was Nor-Tech Fabrication, which is based in Kelso, Washington.
Nor-Tech built a drive-over feeder and an overland conveyor that helps to marry the very front of the plant to the back end.
“CDE and Nor-Tech worked really well together so we could integrate the two systems,” Carlson says. “We have a Nor-Tech scalp screen over top of CDE’s conveyor. Those two had to meld together really well.”
The nature of the material in Caldwell dictated some of Knife River’s decision-making.
“This is mostly a sand deposit on the really fine end of things,” Carlson says. “But we get some petrified wood or big chunks of clay now and then. We’ll pull those out, and then it goes to the wash plant.”
The clay requires special handling, though.
“It doesn’t really break down unless you let it sit, slake or dry out a bit,” Carlson says. “We basically stack the product off with a radial stacker and let it sit for a couple of days. Then, we have a feeder refeed it to the plant.
“The feeder is nice in that if the material happens to be cleaner and the clay breaks down easy enough, we can swing that radial stacker straight over, feed it to the core side of the plant and run it through. But much of the time we’re letting that stack off, dry for a little while and then feeding it back to the plant to wash it.”
Carlson is especially pleased with the design of the feeder.
“Nor-Tec did a really good job on the feeder,” Carlson says. “Normally, those aren’t done well. People typically want to put valley angles in them. The valley angles are where it has the flattest slope, so typically you’d have the sidewalls tilted out and it all comes together.
“Well, that’s where bridging, plugging and things like that come in,” he adds. “When you do the sides vertical, you eliminate the valley angles. So, you have much better material flow. It’s a nice arrangement.”

The wall system around the feeder is another detail into which Knife River put careful thought.
“The wall system you see here is a little unique,” Carlson says. “That’s standard Texas K-rail that they use on projects, and it’s actually a geotextile system that holds it back. The wall is facing, and it’s similar to what the Federal Highway Administration is using on a lot of their bridge projects because it’s low tech and it doesn’t require special equipment or skilled labor to build it.”
As Carlson further describes, alternating layers of fabric and rock make up the wall system.
“Every wall piece has a layer of geotextile fabric,” he says. “That’s what really holds the thing together. It’s a really sturdy wall setup that could be relocated if we need to.”
Knife River may opt to move the feeder as its source material gets farther away.
“We may want to move this feeder to reduce the number of haul trucks required to keep costs down somewhat,” Carlson says. “Haul trucks are expensive to own, operate and buy.”
Worth mentioning
Another factor Knife River considered as it prepared the Scamardo Plant was maintenance: the less, the better.
“We’re trying to make things last and touch them less,” Carlson says.
One case in point is a hopper following the primary feeder that utilizes rubber liners.
“The idea was to set this up so we’re doing as little maintenance as possible,” Carlson says. “We’ve got a modular rubber lining system where it has bolt-in 1-ft. x 1-ft. square panels that are easily swapped out and replaced if there’s wear. The rubber wears better than steel and lasts a long time.”
The minimized maintenance approach applies to Knife River’s wet processing system, too.
“We were definitely looking for a customizable setup,” Carlson says. “Typically, CDE has the log washer integrated into a module, but we wanted things incorporated that would give us access for maintenance. They were very accommodating to all of that.”
Related: Hawaiian Cement making the most of waste material