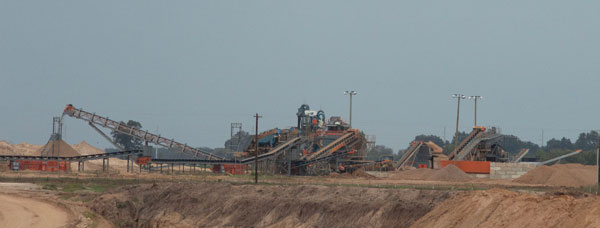
Out with the old, in with the new.
Knife River Corp. went this route over the last few years in the College Station-Bryan market in Texas, transitioning from a retiring sand production site that was operational for more than a decade in Bryan to a brand-new location in nearby Caldwell.
Knife River integrated an assortment of wet processing equipment from CDE into its new Scamardo Plant, which supplies the company’s ready-mixed concrete plants in the area along with the local customer base.
“With the way this plant’s set up, it can do all sorts of neat stuff with sand,” says Curtis Worley, special projects manager at Knife River. “It’s not only concrete sand we’re making here, but we’re making three different types of golf course sand for the United States Golf Association.”
Before selecting CDE as the vendor of their wet processing plant, leaders behind the Scamardo Plant had the opportunity to learn from their Knife River counterparts in Hawaii, who’ve run equipment from CDE for several years.
“Also, some of the executive team at Knife River made a trip to Ireland to tour the [CDE] factory and visit with [executive chairman and founder] Tony [Convery],” says Ben Carlson, formerly Knife River’s vice president of operations for the South who’s now in that same capacity for the company’s Pacific region. “We got a sense for how they were doing things. That was when we decided we wanted to do something here.”
The devil’s in the details
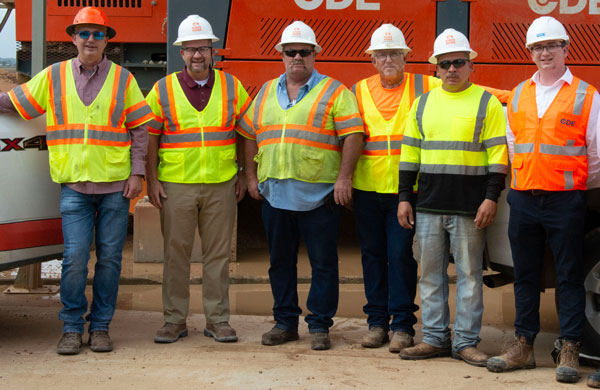
Every sand site, of course, is somewhat unique. The gradation of Knife River’s sand at the Scamardo Plant called for a unique systems approach.
“The way CDE approaches it is quite consultative,” says Andrew Bunting, customer relationship manager at CDE. “With the gradations coming in, they’ll tell us what they want to make and we’ll figure out the equipment that’s needed. It’s not necessarily ‘off the shelf.’”
The inclusion of fine screens on the front end of the wash plant makes the setup of Knife River’s Scamardo Plant somewhat different.
“The fine screens are not something you have in every wash plant,” Carlson says. “That’s because we have that fine sand, so it adds a level of complexity. You must feed that fine sand in or out of the product to keep your concrete sand in spec.”
Knife River actually installed fine screens at its old site before relocating those and building the rest of the plant in Caldwell. The experience with those in Bryan set Knife River up well in Caldwell.
“Basically, we’re taking the sand apart at roughly 30 mesh,” Carlson says. “The core side goes off for our concrete sand, and then [with] the fine side we put as much as we can toward the concrete sand.”
The Scamardo Plant’s dewatering screens were key components of the equipment selection, too.
“Our dewatering screens have some flexibility [in terms of] what to do with the filtrate sand,” Carlson says. “There are some settings to play around with on that very finest portion of the sand. Do you want it in the fine sand? Do you want it in the concrete sand? Or, where do you want to put it?”
When visited in October 2023, Knife River was producing about 110 tph on the aggregate side of its plant and about 250 tph on the sand side.
“At one point, we got to playing with the plant and hit 400 tph,” Worley says. “But we backed it down. We’re looking to upgrade a screen media, so we’re probably going to average about 350 tph.”
The use of a “flexible” media on one dewatering screen was proving beneficial in 2023.
“Those screens came outfitted with standard modular media,” Carlson says. “With modular media, when you’re trying to screen fine, you have issues with pegging. It’ll plug up their screen. But one of their (CDE) representatives had mentioned they were trying an R&D experiment with flexible media. We told them we’d like to try that on one of the screens.”
Knife River found the flexible media performed well.
“You can see the difference on the screens that are modular,” Carlson says. “They have water building up and the water doesn’t go through as easily. When the water doesn’t go through, that means the fine sand’s not getting through it as well, either.
“The side-tensioned (flexible) media they converted us over to flows extremely well,” he adds. “It’s not pegging or blinding on us, so it’s been a success. We should be able to get more tons per hour by converting those screens over to a side-tensioned flexible media.”