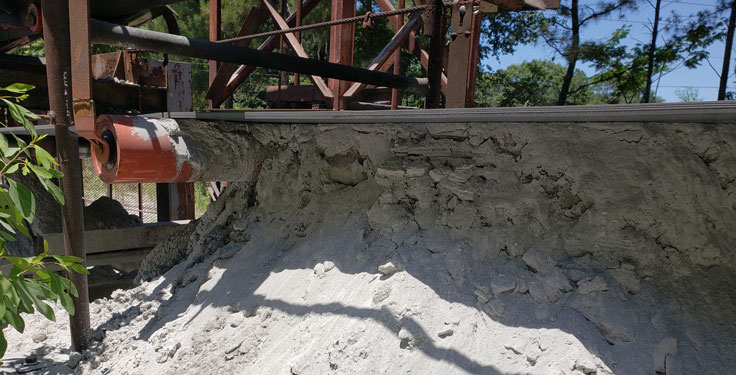
Nearly every customer I visit asks me the same question: “What is the best, most cost-effective [part] I can buy for my system?”
This is one of the most practical questions they can ask. Whether they’re looking for a conveyor belt, a scraper, troughing rollers or pulleys, the answer comes down to a few questions.
1. What material are you processing?
This can be a simple answer for many: rocks. Still, more details are needed.
What type of rock? What is the weight, shape and size? Are there chemicals or oils present? All of this affects which components can be used in the system.
For example, a belt with a higher impact/tensile rating is best for a shale rock with sharp points. But if any oils are present, you will need oil resistance.
Knowing the specific material mix can be crucial in applications such as garbage and waste. Understanding that the material is “garbage” is not enough information to identify a best option.
For example, I have a customer with facilities in multiple states. These facilities have duplicate OEM-built conveyors, running nearly the same tonnage of garbage. When I visit one of their facilities in the East and compare the materials processed to facilities in the West, I see significant differences. As noted in our on-site surveys, one system runs more organics or sand, while the other runs more car parts and heavy steel.
2. What is your maintenance schedule?
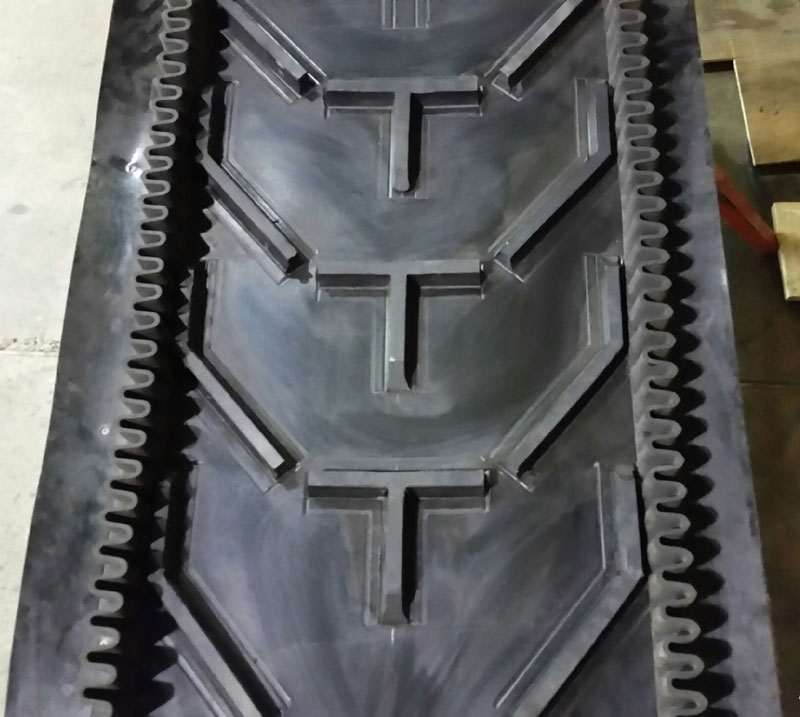
The reasoning behind a maintenance schedule may sound obvious, but in the heat of production this is something that is often sacrificed.
Preventive maintenance is vital, and skipping or using a quick fix often turns into lost time. Some parts are easy to predict and visually monitor. Some have built-in monitoring systems, and others are just built to survive neglect.
Like conveyors, trucks can be used for various jobs and optimized for peak performance with small adjustments. For example, by changing the tires on your truck, you can get better gas mileage, enjoy a quieter ride and increase traction on muddy off-road trails. Knowing your terrain and the goals for your truck will affect what your local tire distributor suggests.
The same goes for a conveyor system. Different components require different levels of attention. Knowing your production goals and your availability for maintenance will help determine the components that will work best for you.
3. What else are you willing to change?
One component change could impact how the other components work in a system, so an immediate follow-up question is: “What is your budget?”
Back to the truck scenario, you may want to go off-roading and rock crawling. But changing from your standard-size all-terrain mud tires to 48-in. mudders will take a bit more adjustment than buying and installing. The truck’s power, gearing and suspension must be able to handle the larger tires.

In terms of conveyors, a bigger, stronger belt will typically need larger pulley sizes, heftier troughing and idler rollers, and more power to move heavier items.
As an example of this change, a facility customer needed to get more material up an incline conveyor. He spoke with a local distributor who explained he needed to increase the cleat height. The customer ordered this new style, but soon after installation it was discovered that the original return idlers and scrapers were not designed for the larger cleats.
The customer then called our team for help and direction. After a full survey of the system, it was determined he needed to replace all idlers and obtain a new scraper compatible with the larger cleats. The facility customer didn’t want to return to the original-size cleats because he was getting more production and less fallback down the conveyor. He hadn’t realized the cost would be much more than investing in a new belt.
Food for thought
You can research the best scraper in the business, the best conveyor belt or the best troughing idler. But all those questions are missing “for your application.”
A distributor can point to nearly every scraper that is the best – in the right application. A distributor cannot tell you which scraper is best for you without having that vital information.
For optimal results, work with a qualified, trusted supplier to thoroughly evaluate your system and product.
Related: How to correct common belt maintenance errors
Jason Crain, who has been in the conveyor belt and systems industry for more than 27 years, is manager of regional operations at Motion Conveyance Solutions.