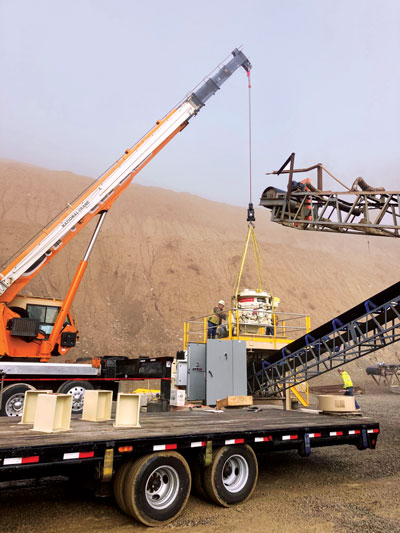
Editor’s note: Part 2 of this series focuses on the maintenance of secondary plants. Part 1, which focuses on primary plants, is available here.
Secondary plants are every bit as critical to aggregate production as primary plants, so it is important to be familiar with the ins and outs of your secondary system.
The secondary is vitally important to about 98 percent of quarry applications, with the exception being riprap or surge-based operations. So, if you have more than a pile of riprap on your site, pull up a seat because this content is for you.
Getting started
The real fun for operators begins after material leaves the primary plant and enters the surge pile.
From the surge pile and feeders to the scalping/sizing screen and the standard crusher, these pieces of the puzzle making up your plant all rely on each other to successfully crush. These pieces create a big picture for your plant, and it is crucial to keep a close eye on all of them. By doing so, you can ensure your plant produces at its optimum capacity to meet the needs of the operation.
Several steps should be taken to ensure your plant is finetuned and runs the way it must. One responsibility of operators is to ensure maintenance and surveillance happens at all levels of the operation.
Take conveyors, for instance. To ensure belts are in their best shape, a few steps should be taken to ensure a “rip and drop” does not occur.
Check equipment every day
Walk your belts daily – even multiple times a day – to look for anything concerning. By walking the conveyors, operators will become more familiar with them and, thus, more easily spot issues before bigger problems arise.
When specifically looking at conveyor belts, check for:
• Snags or small tears along the edge of the belt. It’s incredibly easy for this minor issue to cause a belt to track into the frame and create a rough edge. Within a few days, a rough edge can easily cause a tear.
This should never happen. If an operator sees a belt track into the structure, action should be taken immediately to correct or train the belt back into position.
In the past, I’ve seen seasoned miners use a sharp knife to trim a snag into a smooth transition back into the belt. This helps eliminate a point where a more extensive tear could start. Of course, this is not an ideal practice – and it should only be done when there is no alternative. But if a snag is left, it will find an unforgiving edge and end as a tear – usually sooner rather than later.
Something as simple as a belt tracking off to one side can cause a snag to become a much bigger problem. I have personally witnessed a snag that was not addressed catch an I-beam and rip almost halfway through a conveyor belt. Luckily, we were on the ground watching the belt due to a tracking issue, and we were able to stop the belt before it made another round back to the snag.
• Dry rot. Look for this or for belts that are too worn to stay in production. Sun bleaching will cause dry rot over time. This will change the nature of the conveyor and the work it does.
Sometimes, a judgment call must be made to replace a belt or not. I’ve been to plants that utilize belts that should have long since been replaced. Their rich black color is replaced with an ashy gray, leaving one to wonder how many more passes a belt can take before it rips.
• Rollers. Attention is often placed on head, tail and breakover pulleys while rollers are ignored.
If you have ever worked on the ground in a quarry, you know one thing pulleys have that rollers do not: grease fittings. Rollers are typically a sealed bearing system that can work great for many years. But, like everything else in a quarry, the bearings will eventually fail. And when they do, that “can” will stop rolling.
When that happens, it doesn’t take long for the thin metal body of the roller to be eaten away and develop a razor-sharp edge – with rubber continuously sliding over it.
You can imagine that this creates a ticking time bomb for a bad situation to develop. So, watch the rollers.
Fortunately, it is easy to spot a non-functioning roller. If it’s not rolling, it’s time to address it.
Still, be cautious when changing rollers out. They can be sharp. Also, once a hole is worn into a roller, they like to hold material. This can make them heavy and hard to manage when changing them out. So, again, do this carefully.