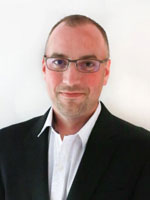
Slip, trip and fall (STF) events continue to represent the majority of recordable injuries in the industries I’ve supported.
A common misconception is that a simple trip event won’t result in a major injury. This could not be further from the truth.
I have investigated broken ribs and a collapsed lung from a simple trip on a communication cable in a scale house. I have investigated a similar injury from someone slipping and landing on a fuel tank, breaking ribs and puncturing lungs.
Ground level STF events can result in serious injuries. Falls from greater heights can also be catastrophic, including ones from ladders, aerial lifts and fixed platforms, as well as when accessing and egressing mobile equipment.
STF events are entirely preventable. With some foresight in assessing risk and taking appropriate actions, STF events can be eliminated. Some of the things you can review with your team are housekeeping, guardrails, three points of contact, footwear, procurement assessments and “ladders last.”
Housekeeping
The intentional act of keeping things orderly and organized will result in a habit of walkways and work areas being clear of trip hazards. This goes for the plant, scale house and any facilities supporting the operation.
One thing to consider is managing material spillage from conveyor belts. Left unmanaged, spillage will create STF hazards, and it may negate the effectiveness of guardrail systems.
Guardrails
Relative to STF events, guardrails must be intact. Also, using ladders near a guardrail will likely make it ineffective. You may need additional fall protection.
Three points of contact
When climbing ladders – fixed or portable – or accessing mobile equipment, you always want to maintain three points of contact. This means your hands are free to support you. It may also mean hoisting materials to the level you’re working on rather than carrying them.
In addition to maintaining three points of contact, you want to control your descent speed and force in a controlled manner. I have investigated incidents where three points of contact were maintained, yet team members still came down too hard – causing damage to knees.
Footwear
Additionally, footwear should be in good condition, supportive and appropriate for the work. Those located in a northern climate may need slip-resistant footwear to contend with snow-removal activities.
For those contending with snow and ice, the best practice is to manage the terrain by removing snow and treating surfaces with sand or salt. Footwear can help, but proper management of ground conditions is the most effective.
Procurement assessments
As you purchase items or invest in capital expenditures, you should always assess for STF hazards and control them early. Mobile equipment, plant improvements and construction, and any other “thing” you may bring into your location should be assessed.
It is often possible to engineer out the need to access heights in the first place – for example, piping in lubrication points so they can be managed at ground level.
‘Ladders last’
Many emergency department doctors stay busy because of injuries associated with ladders. Here are a few things you can do to avoid those sorts of visits:
1. Attempt to eliminate the need to access heights with engineering controls.
2. Replace ladders with stairs.
3. Use aerial lifts if possible (and if trained)
4. If ladders are still needed, secure them if possible by ratcheting them to structural steel and maintaining three points of contact.
I recently interviewed John Rankins, safety manager at Pike Industries, who adds some clarity to the concept of “ladders last.”
“At Pike Industries, our safety committees are actively engaged in removing ladders and replacing them with stairs – or removing the need to attain height completely,” Rankins says. “The committees across New England have removed dozens of ladders over the past five years.”
Final thought
The suggestions presented within this article are just a few ways to eliminate STF events.
For the supervisors reading this, I’d encourage you to review this article with your team and engage them in how to reduce STF events. After all, it takes the whole team to tackle STF hazards.
Steve Fuller has worked over the past 20-plus years with a variety of industries – including aggregates – in operational and safety leadership roles. Now representing Steve Fuller Company, he can be reached at steve@stevefullercompany.com.