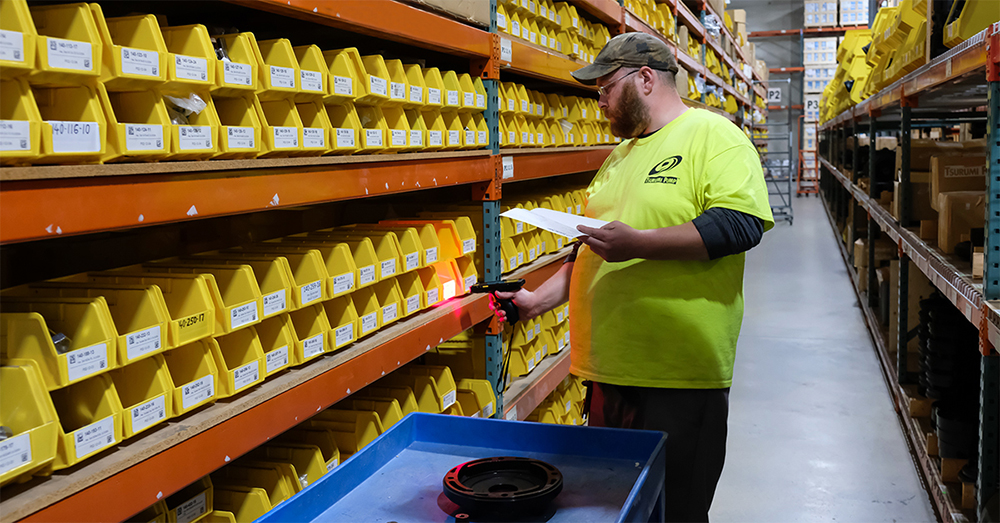
A well-maintained pump ideally won’t malfunction.
Still, an attentive operator will hustle to diagnose the issue at hand when one does go down.
Sometimes, the issue involves a faulty part. In such an event, quick access to a replacement becomes critical so the operation can resume as normal.
To alleviate issues like this one, some pump manufacturers have invested in their own parts inventories of late. Schurco Slurry, for example, promotes how it stocks thousands of items regionally, as well as in its primary inventory in Jacksonville, Florida. Dealers are key to Schurco’s strategy, as well.
Similarly, Tsurumi Pump touted late last year how it’s made investments to enhance its inventory management and parts network to improve service for customers across North America.
Tsurumi says it implemented these measures by adding inventory management and supply chain planning software – not only to optimize inventory levels across its distribution network, but to ensure fast delivery times for end users.
“By maintaining a well-stocked inventory of products and spare parts, Tsurumi ensures fast response times and helps customers minimize downtime for maintenance repairs,” says Lisa Ferguson, inside sales representative at Tsurumi. “This approach not only reduces costly downtime but also builds lasting trust in Tsurumi’s reliability. Our customers need to know they can count on us to provide the parts and products they require to keep their operations running smoothly.”
Technology focused
Lately, manufacturers in the pumps space have focused on increasing their own production capacities while incorporating technology into equipment that gets ahead of operational issues for end users.
“We are integrating technology into our equipment solutions,” says Sarah Smith, district manager at Xylem during a discussion at the 2024 Pit & Quarry Roundtable & Conference. “I think with the generational shift in workforce you are seeing that desire for technology.”
Remote monitoring is among the capabilities now available to pump operators. While this tech can reinvent how operations manage equipment, Smith says it must be easy to use if it’s ultimately going to be adopted.
“We are trying to make sure that the data presented is easy to digest and so it’s easy to understand how to respond to it,” she says. “We are trying to integrate it that way from either smartphones or monitoring condition devices.”
Xylem’s approach to remote monitoring is two-fold, though.
“We also are taking it to another step of having our own internal teams being able to monitor field-smart technology, where we can then reach out to the customer to say: ‘We’ve been monitoring your equipment, and X, Y, Z is going to happen. You need to address that right away.”