The following transcript was edited for brevity and clarity from one of two concurrent Feb. 2 discussions at the 2024 Pit & Quarry Roundtable & Conference. Part 1 of this conversation can be found here.
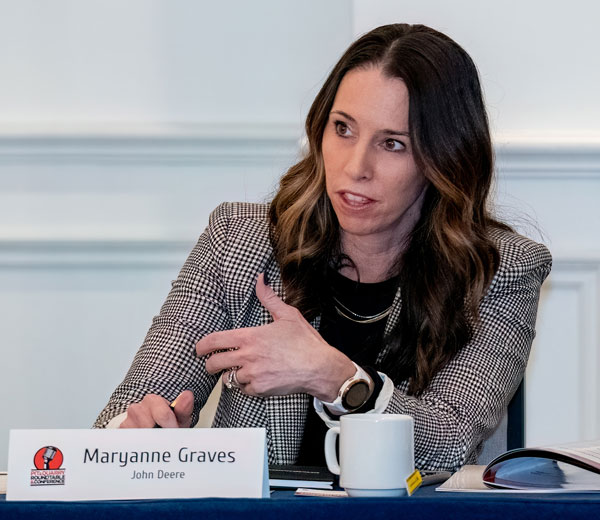
PIT & QUARRY: What impacts, if any, have global conflicts like the Russia-Ukraine war, the Israel-Hamas war and China-Taiwan tensions had on your business to date? What other events or developments outside the industry are you watching that might ultimately affect the aggregate industry?
BRIAN VRABLIC (RULMECA): One thing we should all be aware of is this Red Sea situation. It won’t necessarily slow down the movement of material or change the availability, but what it’s going to do is increase the cost of containers because there aren’t enough containers being built in China or in other parts of the world.
So, when these ships have to go around Africa instead of going through the Red Sea to get to where they need to go in Europe to supply a lot of European manufacturers in here, the cost of the container is going to go up. Maybe it’s a small number, but I think we should all be keeping an eye on that Red Sea situation and how that affects supply chain.
CHARLIE JOHNSON (DSC DREDGE): During the pandemic, I was tasked to find containers. I found out that China was paying double what they were worth in order to get them shipped out. China bought up all the existing containers in the U.S. and right after that happened, our freight costs from China doubled.
JOHN BENNINGTON (SUPERIOR INDUSTRIES): The war in Ukraine affected steel pricing, and I don’t think anybody here isn’t affected by steel costs significantly.
As far as 2024, what we’re anticipating is inflation to stay in that 2 to 2.5 percent range. That’s what we’re hoping for anyway because then it means it won’t affect rates too much. That’s probably a bigger concern for us than anything else in the industry.
NICK PEARMAN (ROGERS GROUP): A lot of the extended lead times on anything electrical are coming out of China or Taiwan – especially processors. That can cause a whole world of burden. If you’re already just recovering from everything from COVID and something sets that off, it’s very hard to operate when you can’t get those electrical components.
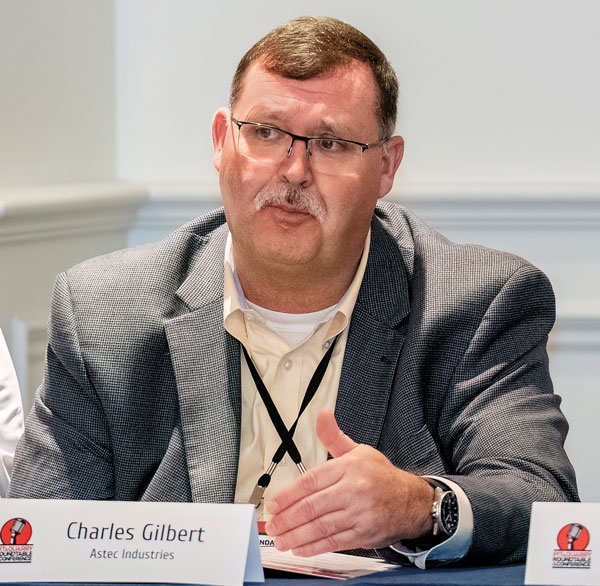
CHRIS WILLIAMS (CAPITAL AGGREGATES): China-Taiwan seems like it may be a major risk to supply chain again in certain segments if anything were to happen there. It’s a point I think we should all pay attention to.
JOHNSON: Our 72-week lead time on Cat engines is chip related for the modules. They couldn’t get the chips or semiconductors for the modules that run the engines. That was what Caterpillar reported to us. It was all centered around chips. All of our touchscreens, all our dredges – we couldn’t get because of the chip issue. It translates into a lot of different components.
PEARMAN: We have to get better, and technology is the way to do it. The reality is a lot of the technology is not robust. It doesn’t stand up in a brutal environment.
When you’re talking about buying equipment where you know there’s a lot of vibration and a lot of risk getting hit with heavy rocks, you start looking at how to tone down the number of sensors and things on it so that it runs. It still has a safety aspect, but it runs more dependent. Challenges in getting chips and other electrical components do play a big part in what we decide to do.
JONATHAN KOLBE (ALLEGHENY MINERAL CORP.): It comes down to the idea of technology for the sake of technology. I don’t think anybody’s going to argue with some additional safety features, but a lot of these sensors are not built to be in quarry applications.
Talking to our shop staff, they would love to rebuild old 980s in lieu of purchasing new equipment just to get away from the electrical issues that they’re having. We hear that time and time again from our shop foreman just because it avoids all of those additional sensors that seem to just plague a drop zone.
CHARLES GILBERT (ASTEC): I hear more of our customers today asking for those sensors [or] fail safes because they need the insurance due to the quality of help they’re able to hire.
It’s a double-edged sword: You want the safety, you want the data, you want the technology, but you don’t want what comes with it. It’s kind of a necessary evil. We don’t have the quality of the people coming into our industry, and we have to protect them. So, we need to invest in all these safety features that include all those sensors, unfortunately.
MARYANNE GRAVES (JOHN DEERE): From a manufacturing perspective, we’re facing the same thing. What are the problems our customers are facing? Jobsite safety and lack of skilled labor. Technology can help us solve those problems if we do it right.
Our testing needs to be robust enough, and we are making those adjustments as the manufacturer. Looking at doing the job right the first time and making customers more productive, it’s those automation things that allow us to do that. We’re making sure we’re balancing the tech with not doing it for the sake of technology. Helping solve the problems you’re all facing on jobsites is really what we’re trying to do.
Related: Major’s Edwards shares market view for 2024
Featured Photo: PamElla Lee Photography