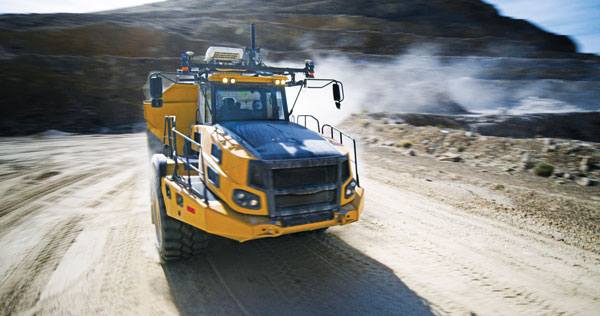
For Pronto, the name of the game is minimizing the space required to operate an autonomous fleet.
Whereas larger fleets need large control rooms with anywhere from five to a dozen people managing the fleet, Miller says Pronto aims to provide a reduced physical footprint for smaller mining operations.
“A typical quarry application is going to have three to five trucks,” Miller says. “Some of the larger quarries might have a dozen trucks. What has to be offered into the smaller mine operations is a way to have a reduced control room impact or no control room at all.
“[We] envision implementing the control room in a mobile device,” Miller adds. “So an iPhone, for instance, manages most of the fleet interaction. From the iPhone interface, you’re able to dispatch trucks to the loading tool or to their destination, whether it’s a waste dump, a crusher bin, a long-term stockpile or a short-term stockpile. That’s all done through a mobile device rather than a control room.”
Pronto also allows operators to save programmed routes and share them with other haul trucks within a fleet.
“Take one of the trucks driving along the route, record that route and then that route becomes available,” Miller says. “Imagine [the route is] a dog bone. In the center of the dog bone, that route doesn’t change at all. It might not change for weeks. But on the two ends, whether they’re interfacing with the loading tool or if they’re dumping out a large stockpile, the trucks will dynamically generate a path that gets them underneath the hung bucket of the excavator or front-end loader, or gets them to the assigned dumping point.”
With MineStar Command, human loader operators currently play a role in the performance autonomous haulers.
“Loader operators have a screen where they interface with the system,” says Aaron Donnelli, an engineer manager at Caterpillar. “They set a spot point to position the truck and, once loaded, they tell the truck to depart. The systems on the loader know what materials it just loaded, so the truck knows what material it has.
“The MineStar system will then say: ‘Go to this stockpile,’” he adds. “Or, ‘Go to the crusher.’ The truck then drives itself there.”
Because some parts of quarries are more static while others are more dynamic – like a loading area – Donnelli says operators can update routes as needed. Even if it isn’t for long periods of time.
“You’ve got certain haul roads that don’t change very often,” he says. “We consider those to be more ‘static’ areas. You survey those initially, and maybe they don’t change for weeks, months or years. In a dynamic area, we have a couple of things we can do. The truck can survey the face as it moves through the site, and we can update our GPS data based on that.”
Risk reduction
Miller, who has a PhD in mining engineering from the Colorado School of Mines – with a focus on autonomous hauling safety – says autonomous hauling provides a significant benefit when it comes to mitigating risk on jobsites.
In his estimation, risk can be reduced up to 100 times.
“You’re eliminating exposure to risk by reducing the number of people in your pit [and] removing the drivers,” Miller says. “You’re reducing the exposure to risk and, on top of that, you’re providing a reduction in the in-pit traffic.”
There are several layers of safety that go into protecting workers from incidents involving autonomous haul trucks. The first is situational awareness, which allows vehicles within the autonomous operating zone, or the pit, to know where each other are, their velocities and the direction of their travel.
“They keep the vehicles away from each other and will bring an autonomous truck to a stop,” Miller says. “If you look at all the safety records that show up within Western Australia – they have a very good safety record database – all of the incidents that are logged were stopped by the situational awareness layer. That’s the most protective layer.”
After situational awareness comes object detection. In the case of Pronto, Miller says the company utilizes camera technology and machine learning algorithms to not only identify that an obstacle is present, but to categorize it and make a decision about what should be done for those interruptions.
Yet another layer – one that is not unique to autonomous hauling – is an emergency or “all-stop” button.
“That big red button will bring all the trucks in the fleet to a stop,” Miller says. “If you look at many of the powered haulage incidents which have occurred in the U.S., typically the person involved in the fatality was attempting to get out of the way of the truck. There’s quite a bit of time between when the collision occurred and when the risk was presented to the truck.”
But the safety benefits of autonomous hauling extend beyond just those three layers, according to Miller.
“If you look at a total autonomy package, you have a stack of layers – maybe five of them, honestly – that aren’t presented in a typical manned-only fleet,” he says. “You’re coming in with a really significant risk reduction by putting in autonomy.”
Editor-in-chief Kevin Yanik contributed to this article.