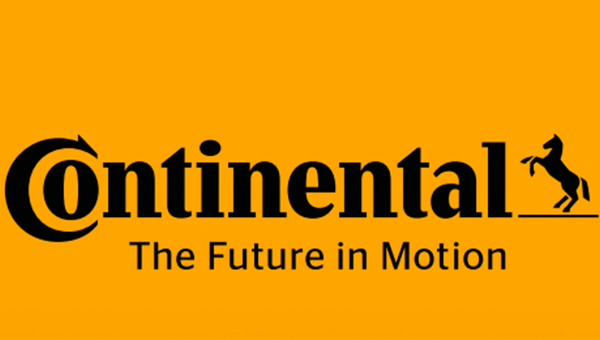
Continental showcased several pieces of equipment and technology at MINExpo, with the company’s solutions encompassing conveying, monitoring, fluid and specialty mining hoses, suspension and power transmission.
Continental debuted Conti+ 2.0, an enhanced version of its app-based service platform that is designed to be simpler, faster and more comprehensive. The technology provides advanced options to manage conveyor systems from anywhere, increasing the efficiency and profitability of operations across all components and processes.
Conti+ 2.0 is available in four modules to better fit customers’ operational needs. The basic module provides quick access to all master data, and an inspection module allows detailed inspection reports to be generated. An IoT module bundles static and dynamic data on one centralized platform, and an engineering module provides support as early as the plant design stage.
Continental says Conti+ 2.0 provides smart support for customers and distributors that is complemented by additional functions, a new structure, a modern design and a user-friendly interface.
Additionally, Continental highlighted its comprehensive conveyor belt services at MINExpo – including installation, maintenance, repair and splicing, and various components.
The company’s fluid hoses and specialty mining hoses, suspensions and power transmission belts, monitoring and other solutions were on display, as well.
“We understand that working in the toughest places on Earth calls for world-class solutions,” says Sven Hlywiak, vice president of customer-engineered solutions of industrial solutions in the Americas at Continental. “From the Phoenecord ST10000 – the strongest belt on the market – to the new Conti+ 2.0 technology that reduces downtime with an at-your-fingertips app, Continental is revolutionizing mining operations for owners and operators.”
Severe-duty motor debuts
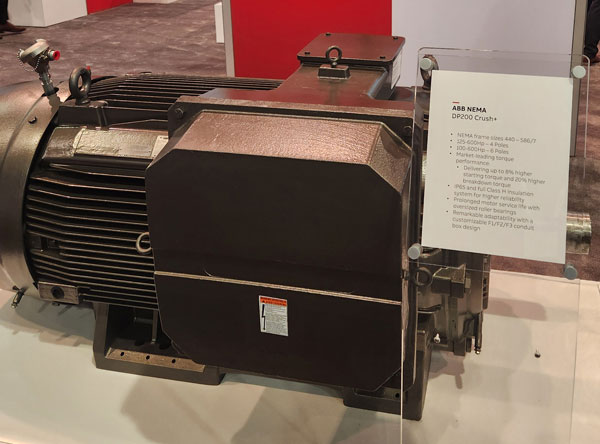
ABB launched a severe-duty motor for use within aggregate operations at MINExpo.
According to ABB, the new DP200 Crush+ motor is designed to excel in the harshest environments. The company says the motor raises the standard for performance and durability in crushers and other applications.
“ABB has designed and manufactured the DP200 Crush+ motor to meet or exceed our customers’ needs for energy efficiency and reliability,” says Oscar Palafox, ABB NEMA motors global portfolio product manager. “The modular design offers a high level of flexibility for our customers and makes it easy to upgrade or retrofit existing systems in the field or implement future equipment designs and requirements.”
Built on the company’s SD200, three-phased motor platform, ABB says Crush+ optimizes performance, efficiency and long-term maintenance costs while delivering high starting and breakdown torque. With a power range of 100 to 600 hp, a cast-iron design, Class H insulation and a multi-position conduit box, the company says Crush+ allows for customization to meet diverse operational needs.
A heavy-duty frame, available in NEMA 440 to 580 sizes, ensures Crush+ can endure harsh operating conditions, the company adds, while a high-strength 4140 steel shaft reduces the risk of damage under high-stress loads. Crush+ is safeguarded against dust, water and other contaminants with IP65 ingress protection and non-contact labyrinth seals, ABB adds.
Crush+ is compatible with the ABB Ability smart sensor for digital powertrain monitoring in hazardous environments. ABB says this enables proactive maintenance to maximize safety and efficiency.
The sensor’s durable enclosure withstands vibration, dust and water and is certified for ATEX, IECEx and NEC500 to meet standards for explosive atmospheres.
Related: Drilling Deeper Episode 25: What you missed at MINExpo 2024