MINExpo International 2024, which took place across three days in late September, presented an assortment of new conveying and material handling equipment options to the mining industry.
Among the equipment manufacturers to showcase new wares at the Las Vegas Convention Center were ABB, Continental, Flexco and Superior Industries. Here’s a glimpse at what these companies introduced within their respective trade show booths:
Updated impact cradle
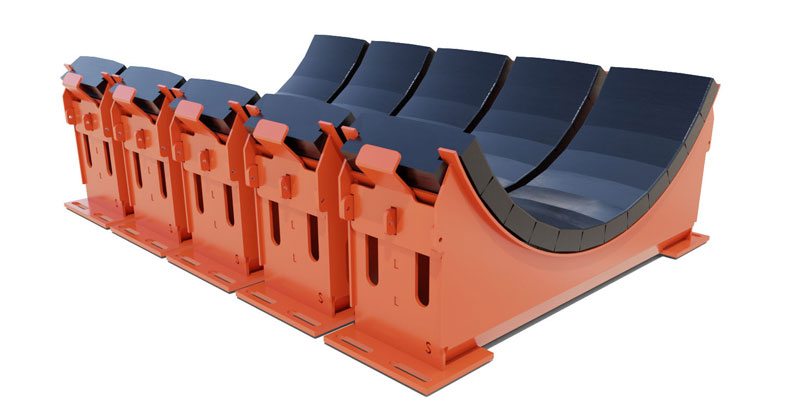
Superior Industries unveiled a revised design of its conveyor impact cradle, showcasing a model at MINExpo.
The new arrangement includes larger pad cartridges to enhance durability and a reinforced point of connection between the pads and the cradle frame.
According to Superior, the new conveyor impact cradle is a modern redesign of the traditional impact bed. While both products absorb the force of falling material to prevent damage to conveyor belts, Superior says its impact cradle is engineered to address common shortcomings associated with the design of traditional impact beds.
Superior’s design, for example, features a curved bed that fully supports belting, leaving no gaps to trap fugitive material. Also, Superior says pads are easy to slide on or off the cradle frame in tight, hard-to-access transition zones.
Additionally, the company says no special tools are required for its impact cradle. Superior’s one-piece pads are made from a special urethane to reduce friction and enhance cushioning.
Superior’s impact cradle is available in two more pre-engineered models: medium and heavy duty. These are available in addition to the standard model, which was first introduced in 2017.
New tools to simplify
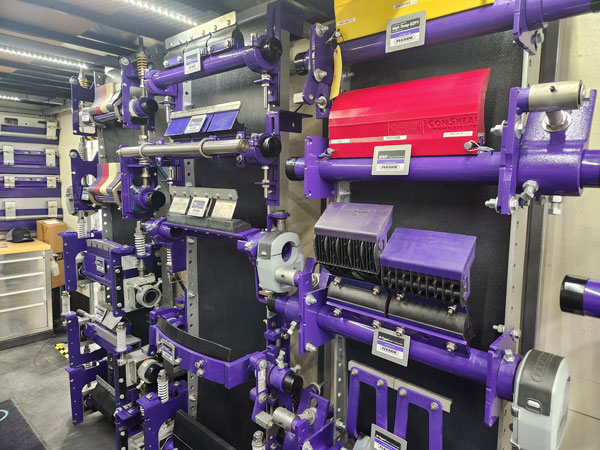
Flexco highlighted a variety of its equipment and technology solutions at MINExpo, including the FXC steel cord belt-fastening system and the 900 Series belt cutter/skiver.
As Flexco describes, the FXC steel cord belt-fastening system addresses a major issue that heavy-duty sites often deal with: unplanned downtime.
“Our team set out to develop a solution that could help,” says Franklin Moore, product manager at Flexco. “That led us to creating the FXC. Overall, the FXC allows users to get their steel cord belts back into operation quickly, drastically reducing the effects of downtime, which helps increase the site’s bottom line.
“We’ve already seen positive results in the field,” he adds.
According to Flexco’s Dominic Filipponi, the FXC is a short-term solution for operators waiting on vulcanization.
“You want them to be able to act quickly and shorten downtime,” says Filipponi, content marketing specialist at Flexco. “Downtime is incredibly expensive. When you’re waiting for vulcanization, you can be forced to wait on weather or a third party.”
Flexco’s soon-to-be-released 900 Series belt cutter/skiver, meanwhile, features a revamped design and other enhancements.
“With updated clamp knobs, a drive handle with manual and powered drill capabilities, and a new design that allows operators to simply slide the belt forward from a cut to skive position, sites can unlock a more consistent, safe and quality mechanical belt-fastening installation process with our latest belt maintenance tool,” says Kevin Fales, product manager at Flexco.