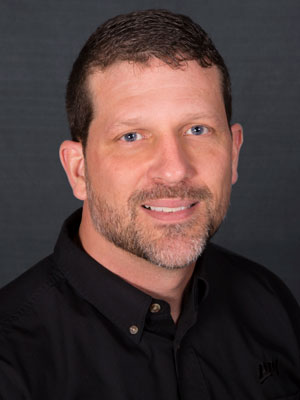
When it comes to conveyors in aggregate applications, the maintenance requirements can be overwhelming.
Heavy demands are placed on equipment, and this leads to high wear and frequent maintenance.
Today’s workforce challenges make it increasingly difficult to keep up with considerable workloads. As a solution to this challenge, many aggregate producers have made efforts to purchase equipment and components that provide extended life intervals to reduce the burden on maintenance crews.
Case in point
One time-consuming job that has the potential to cause unplanned work stoppages is replacing conveyor drum pulleys with worn-out lagging.
The difficulty of replacing these pulleys varies greatly depending on a number of factors. The position on the conveyor, accessibility and pulley size are a few things that determine how difficult the job is. The time required on the job can range from a couple of hours in the easiest changeouts to a day or more in the most difficult cases.
It is often assumed that worn-out lagging is no big deal and that conveyors can function fine even if the lagging is worn through to the steel pulley rim. In some instances, this may be true. But lagging may play a more crucial role in conveyor performance than is often realized.
Lagging provides several benefits, including increased traction to drive the belt and less material buildup in sticky applications. When the drum is lagged, it protects the steel rim from wear.
If too much rim wear occurs, it can cause a sudden catastrophic failure. Also, it can be difficult to recognize just how much rim wear has occurred in these instances.
As lagging in the center of the pulley wears down, it diminishes pulley crown. This diminished crown has an impact on how well the conveyor belt tracks.
The challenge, then, becomes how to make the lagging last longer so changeouts are less frequent. The tire industry struggles with similar challenges, and conveyor component manufacturers are benefiting from what they’ve learned.
Lessons learned
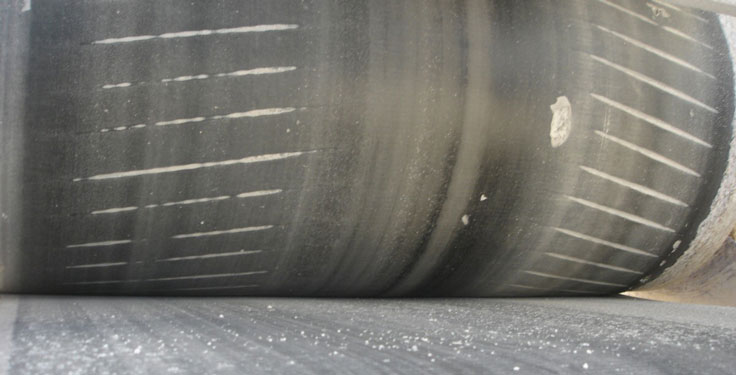
Tire manufacturers have spent a lot of time and effort developing rubber compounds that are more resistant to wear, punctures and tearing while maintaining traction levels. By implementing some of this technology, special abrasion-resistant (AR) lagging compounds can be selected that can have a dramatic impact on pulley life.
Testing has shown results of up to double the life of traditional lagging compounds in high-wear applications. Aggregate producers who deal with some of these highly abrasive materials may get used to dedicating considerably more time to maintenance operations than typical producers.
Still, the financial impact becomes clear when you start assigning costs to this accelerated wear. For instance, let’s assume an abrasive material is being crushed and it is typical to only get 18 months of service life from standard styrene-butadiene rubber (SBR) lagging, whereas AR lagging extends that service life to 36 months.
In three years, a producer would have consumed two standard lagged pulleys but only used one of the AR lagged pulleys. That is one entire changeout that was not necessary.
Let’s say this pulley requires eight hours to replace with a crew of three people for a total of 24 hours. The AR lagging material change would save eight maintenance hours each year. When multiplied by the total number of lagged pulleys in an operation, the savings really add up.
Final thought
Imagine what could be possible if your maintenance crew had more time to make real operational improvements that could drive production instead of trying to stay one step ahead of failing parts.
Related: How to avoid, overcome drive pulley slippage
Chris Long is senior product development manager at PPI (Precision Pulley & Idler).