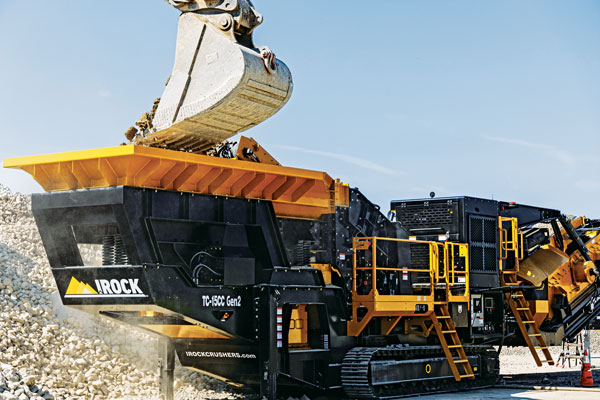
Another manufacturer, IRock Crushers, displayed a TC-15CC mobile impact crushing plant in its AGG1 booth.
In addition to highlighting the TC-15CC, IRock representatives detailed their approach to plant engineering and design. While IRock values some of the technology finding its way onto plants industrywide, the company stresses that functionality must remain at the core of every crushing plant.
“[Machines] seem to be getting more complex, adding features to the machines,” says Paul McCaffrey, director of product development and applications at IRock. “The serviceability tends to take a hit or suffer because you’re adding bolt-on pieces that are on top of everything that’s required underneath all of that.
“We’re trying to keep a focus on the end user being able to operate and maintain the machines,” he adds.
If key areas of a machine aren’t accessible, McCaffrey argues that maintenance may ultimately be neglected.
“We’ve seen philosophies before where they’re trying to make machines look slick and hide hosing and electrical wires way back in behind the chassis,” he says. “We’re not of that philosophy. We’re trying to make it easy to get to if there’s an issue or you need to replace something.”
Additionally, IRock’s Nate Russell says technology should add value to machine performance – not take away from it.
“What I see and hear from a sales perspective in the market is when you start adding all of these sensors and wirings in a very dusty, dirty environment, it only takes one hiccup and [an] operation is down,” says Russell, director of sales at IRock. “With Paul’s designs, we’re going to have sensors to protect the machine and have [it] run effectively. But they’re in the background and they don’t put the unit down, in theory.”
In some instances, Russell says technology is interfering with crushing operations.
“[If] a tail pulley sensor goes on a rock crusher because [an operator is] walking the machine and he hits a rock – and that tail pulley sensor is out – that machine is now down over a little sensor,” Russell says. “What does that cost while you wait for that little sensor to come in?”
As McCaffrey says, IRock’s customers are interested in tech advancements. They, however, put more stock in plant uptime.
“Fundamentally, the first thing they want is a machine they can start in the morning, run it all day and shut it down in the evening,” McCaffrey says. “That’s all they’re really looking for. If you have things that can add value – feedback information at the office – that’s all great. But, fundamentally, it’s got to run first. The reliability is the most important thing over the technology.”
Tech rollout & crusher coming
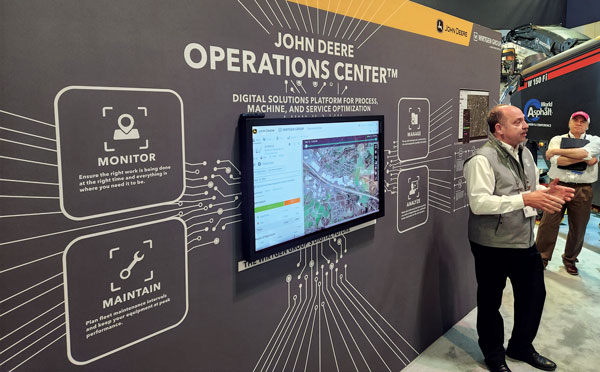
Separately, technology emerged as a topic during a Wirtgen Group press conference at AGG1, where company representatives touched on the John Deere Operations Center.
According to Wirtgen Group, which is a John Deere company, the John Deere Operations Center is a platform that’s been utilized in agriculture for years. Now, it’s being integrated into roadbuilding.
“Fleet management systems are not new,” says Matt Graves, director of marketing communications at Wirtgen Group. “[They] started out with the trucking industry back in the ‘80s. The difference is you’ve taken management, monitoring and maintenance, and rolled it into analysis.”
According to Graves, the John Deere Operations Center provides actionable information for end users.
“It takes all of the incoming data and turns it into an actionable force,” he says. “That’s really the difference between this and just a generic fleet maintenance service.”
In addition to showcasing the technology platform, Graves provided details about the new MR 100 NEO – a mobile impact crushing plant from Kleemann – that will soon make its way to the U.S.
“It’s currently in sale and in production in Europe,” Graves says. “It is going to be launched here in the U.S. in May. We’re going to be bringing our first ones in May. We’re going to do our dealer reveal in June.
Right after that, it’s going to be available to everyone for sale. It’s really exciting.”
The target market for the MR 100 NEO is asphalt recycling, according to Graves.
“It’s [for] a smaller market, because what we’re finding is there’s a niche market for an impact crusher for asphalt recycling on-site,” Graves says.
The MR 100 NEO is manufactured with two drives: a D-Drive or an E-Drive.
“A D-Drive is the diesel drive [and] an E-Drive is the electric drive,” Graves says. “Kleemann has been hybrid for quite some time. Because the diesel engine drives the generators that drive all the systems, we can also typically hook most of our crushers up to line power. Almost everything in our crushing lineup can be set up where a diesel generator can set off; we hook the generator to line power; and then you’re off and running – completely CO2-free in that environment.”