Another high-energy AGG1 came together this year in Nashville, where several manufacturers showcased their latest developments in crushing.
From stationary crushers and portable plants to tech that can elevate operations, AGG1 presented a variety of developments for aggregate producers to consider. Here are a few that surfaced on the trade show floor.
New two-in-one plant
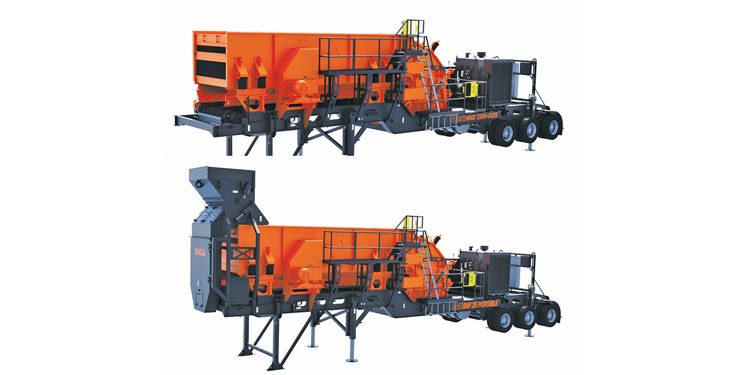
The 1200-OCSS (top) can be turned into the MaxRap 25 portable (bottom) by adding actuated chutework to the plant. Photo: Eagle Crusher Co.
One crushing product that emerged is from Eagle Crusher, which introduced a two-in-one plant.
The new Eagle Crusher plant can be converted between the UltraMax 1200-OCSS (open-circuit secondary system) and the MaxRap 25 portable plant. Both feature the company’s UltraMax 25 impactor, which offers a high-reduction ratio and a North American lifetime rotor warranty.
The 1200-OCSS features a 6-ft. x 20-ft. triple-deck horizontal screen for screening before crushing, as well as screening options for multiple spec products. The 1200-OCSS includes discharge conveyors for second and third decks, as well as for fines. The side-discharge conveyor transports crushed material to other equipment for further processing, stockpiling or to another conveyor for recirculation back to the plant.
By adding actuated chutework to the 1200-OCSS, the plant becomes the MaxRap 25 portable.
According to Eagle Crusher, the MaxRap 25 provides the same precision crushing as the stationary MaxRap, enabling operators to crush reclaimed asphalt pavement (RAP) at multiple locations with ease.
The plant’s side-discharge conveyor can be used for stockpiling, or it can be positioned to return material to another conveyor for recirculation back to the plant.
Additionally, both plant options include a hydraulic lift and leveling system that enables quick setup and teardown by using hydraulic run-on legs. The plant can also run on either diesel/electric or all-electric power in either configuration.
Elsewhere in portable plants
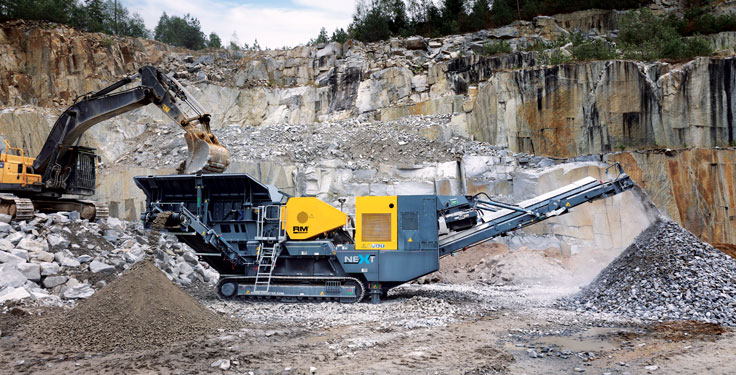
Also at AGG1, Rubble Master highlighted a selection of equipment it plans to release in 2024 and beyond.
Among the equipment to expect from Rubble Master is a new jaw crushing plant – plus expansions to the company’s crushing and screening portfolios.
The RM J110X tracked jaw plant is the first piece Rubble Master intends to release this year. The plant with a 44-in. x 28-in. crusher is set to debut in the U.S. in the second quarter following an international launch in Austria.
According to Rubble Master, the RM J110X will incorporate the company’s new high-efficiency drive concepts and other features. The company says the plant will expand the application range of Rubble Master crushers, open new opportunities in the market, and support the company’s growth path.
Additionally, Rubble Master says it has several product developments in the works that will expand its portfolio of crushers and broaden its offering of screens. Rubble Master plans to enhance its screen production alongside a partner in Northern Ireland in response to increasing demand for the company’s screen line internationally.
Rubble Master also indicates that measures are being taken at its Austrian site, where additional production lines are being built to increase capacity for crushers.
Reconfigured for recycling
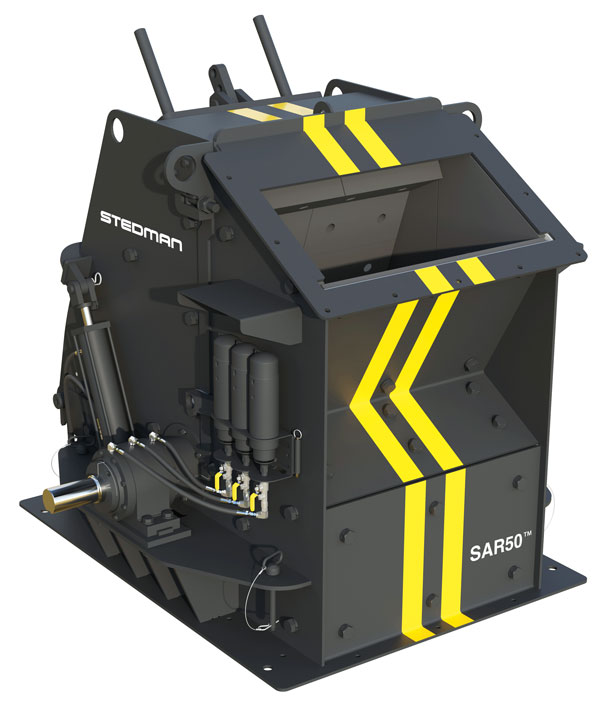
Known for its Grand-Slam impactors and other crushing and pulverizing products, Stedman Machine Co. debuted a Grand-Slam model at AGG1 that opens a door for the company and those seeking equipment solutions in asphalt recycling.
According to Stedman, the new Grand Slam asphalt recycler is designed to preserve the robust features of the company’s secondary impactor yet eliminate the parts not needed in asphalt recycling.
“The [asphalt recycler] has a reduced part count, a reduced weight and a smaller footprint, but it preserved all of the features that do the crushing,” says Eric Marcotte, director of unit and systems sales at Stedman.
As Stedman president Chris Nawalaniec describes, the company’s newest development combines the best of the aggregate and asphalt equipment worlds.
“Our customer profile that will buy multiple of this will be customers who usually have quarries and batch plants – those who have a paving business,” Nawalaniec says. “These go right at the batch plants.”
Stedman realized an opportunity to venture into asphalt recycling after ConExpo-Con/Agg 2023.
“We went to California after ConExpo-Con/Agg and leant [a customer] the cage mill model that we have at the show every year,” Nawalaniec says. “A light bulb went off that impact crushing is used in less than half the states for aggregate producers. For hard rock, you use cone and jaw.”
But asphalt recycling, unlike aggregates, is one and the same across the nation.
“I realized we have 50 states that we can sell this in versus like 26 states,” Nawalaniec says. “Plus, this is such a good machine for uptime. We have one customer who has bought 20 of these. They used to do a centralized RAP pile. They were trucking RAP back to a central location and crushing it in a big expensive portable plant.
“Well, they don’t need to do that anymore,” he adds. “They buy a machine like this, put it right at the batch plant, and they’re ready to use this and make tons of money.”