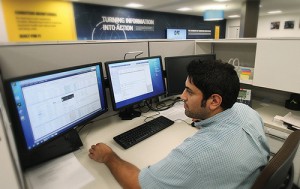
operator safety. Photo: Caterpillar
Caterpillar has launched a 24/7 equipment operator monitoring service designed to provide customers with the ability to see, mitigate and manage operators. Caterpillar can now supply its customers with both machine and operator information with its 24/7 Monitoring Center, where analysts correlate data about the health and productivity of operators and equipment.
“Our customers want better visibility to the interaction between operators and machines, and how behavior impacts safety and productivity,” says Tim Crane, Caterpillar safety services manager. “This innovative solution offers our customers the opportunity to mitigate risk and improve productivity.”
Using Seeing Machines’ Driver Safety Systems (DSS) and Cat Smartbands, Caterpillar is able to determine the status of operators. The DSS includes an in-cab camera and alert system to notify the operator when fatigue or a distraction occurs, while the Smartband captures operator sleep quantity and quality information.
According to Caterpillar, the DSS and Cat Smartband are part of a growing suite of tools that assist customers in improving safety. Data from the DSS and Smartband, along with data from EMSolutions, the Cat MineStar System and the Cat Vital Information Management System, provide insights on fatigue and distraction and their impacts on productivity and profitability.
“Technology alone is not the silver bullet for a safer or more productive operation,” says George Taylor, vice president of the Caterpillar Customer Services Support Division. “In fact, most technologies fail without proper consideration of the organizational culture and a plan to manage change.”