Inspection & monitoring
Some manufacturers offer conveyor inspections and cleaner maintenance as part of a managed service relationship.
Their monitoring systems can track component wear and update the service technician and operations personnel about upcoming service needs. There are some new systems that can even adjust belt cleaner tension automatically. The technology will send an alert through a mobile app in the event of upset conditions.
Factory-trained service technicians provide an added set of eyes on conveyors, traveling to and from the equipment to be serviced and logging details in their reports. Because they see so many different applications, they can often alert to problems that maintenance personnel don’t see – or ones they’ve become accustomed to ignoring.
With factory-direct managed service, the responsibility for maintenance falls on the manufacturer, allowing the staff to focus on other priorities.
Safety
A trained belt cleaner service technician is aware of hazards involved with maintaining belt cleaners.
The indirect costs of an injury or accident can be significant. In-house maintenance and cleaning are two job classifications that are exposed to significant potential for muscular or skeletal injuries. These tasks are typically involved in more than half of reportable lost-time accidents. Having a trained provider that focuses on safety – but at the same time is more productive than in-house maintenance – can be a significant benefit.
Additionally, keeping a shutdown to a minimum is important to meet process availability goals. There are specialized systems to service belt cleaners – ones where a belt runs 24/7 and cannot be shut down, yet virtually all other cleaner maintenance must be performed following lockout/tagout/blockout/testout procedures.
Return on investment
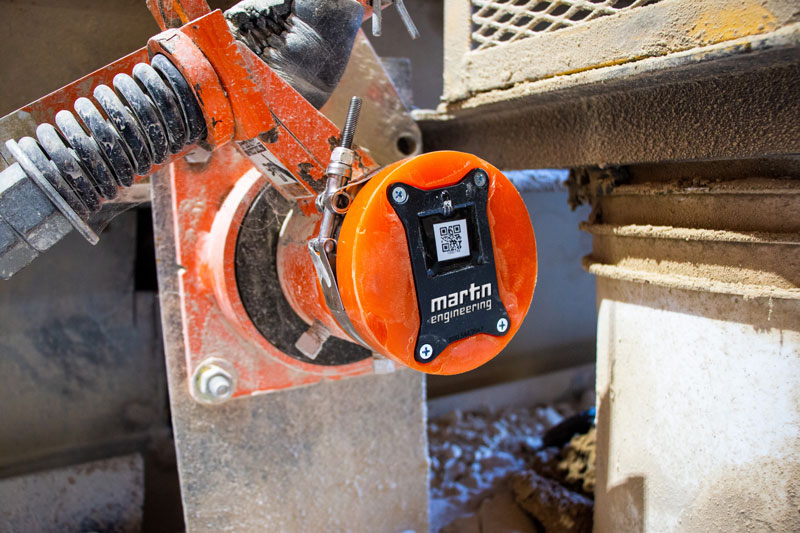
A “run ‘til broke” philosophy means more than broken machinery. It can exacerbate financial issues and affect worker morale, too.
In the rush to patch things together, maintenance workers are tempted to take shortcuts and work around established procedures, exposing themselves to greater potential for injury.
When calculating the return on investment for professionally installing and maintaining belt cleaners, an analysis can be done over the life of the belt cleaner assembly using a net present value calculation. Many spreadsheet apps have a net present value function.
For example, if the cost of capital is 10 percent, the initial investment is $5,000, cleaning labor savings is $6,000 per year, and service and parts are $2,000 per year, then the net present value of the cash flow (discounted by the cost of capital) is $15,163. Subtracting the initial investment and the managed service cost, this example generates more than $10,000 in free cash flow over the life of the equipment without considering all other potential savings.
A typical belt cleaner assembly should last five years with minimal frame or tensioner repairs. Inspections should be done regularly, and any problems should be addressed immediately. Some manufacturers with factory-direct service offer free replacement and upgrades of frames and tensioners as part of their managed service offerings.
Blade wear will vary based on the blade material and abrasiveness of the bulk materials, along with several factors such as correct cleaning pressure. Belt wear from the cleaner is typically about 2 percent per cleaner, so concerns over blade type and cover wear are usually unfounded.
The cost of safety is minimized by reducing the frequency and hours of manual cleaning and, therefore, the exposure to injuries.
Conclusion
Allowing a blade to wear past its limits, having the wrong tension or installing a cleaner system that is hard to access creates hazards for workers. It can lead to excessive downtime.
Automated tensioning and monitoring equipment mitigates some of the issues with blade wear, providing data and alerts when blades need servicing. This can lower labor costs and improve safety through fewer inspections and proactive maintenance.
Belt cleaner maintenance can be time-consuming and pull workers from other essential tasks, so it’s important to choose a supplier with trained and experienced service technicians who know the equipment and safety procedures.
Considering a managed service program can make safety and productivity sense and improve profitability with additional positive cash flow.
Related: Prioritizing conveyor safety, training and parts replacement
Alan Highton and Todd Swinderman are with Martin Engineering.