Evaluating employees gives aggregate producers a tool to better prevent accidents and improve performance.
According to a study by Liberty Mutual Insurance, the direct cost of incidents in industrial workplaces is an average of $38,000 per incident. And indirect costs can add up, too. These may include training replacement employees, accident investigation, implementing corrective measures, lost productivity, repairing damaged equipment and property, and costs associated with absenteeism and lower employee morale.
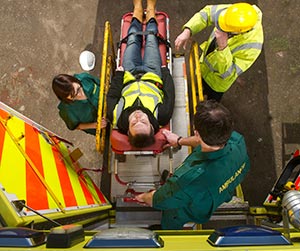
Then there is human error, which may result in up to 90 percent of workplace accidents. Vancouver-based TalentClick monitors various industrial sectors and the percentages at which human factors make up overall accident totals. Operating as a business unit of a larger company from 2010 to 2012, TalentClick was incorporated as a separate company in late 2012. It works in vertical markets, including construction, manufacturing, transportation, natural resources and mining.
Stephen Race, who co-founded TalentClick and specializes in occupational psychology, notes that for half a century social scientists have been researching personality. More recently, research has expanded into how certain personality types are naturally more “safety-oriented” than others.
Race says, “Everybody has a default personality. Some call it hardwiring. Managers can teach people to behave in a certain way for short periods of time, but those employees will always revert back to who they are, especially when faced with unexpected circumstances.”
Risk in five dimensions
TalentClick not only evaluates workers as higher or lower risk, but also applies five additional criteria:
■ Degrees of resistance: Higher-risk employees may disregard authority and rules altogether and be resistant to feedback. By contrast, lower-risk individuals tend to willingly follow guidelines and training, and are compliant with rules.
■ Anxiety factor: Higher-risk individuals may panic or freeze when faced with unexpected safety-sensitive situations, and may even feel unsure about their abilities. The lower-risk workers tend to be confident and steady, as well as calm under pressure.
■ Irritability: Higher-risk individuals may become annoyed by others, particularly under stress, while lower-riskers tend to be less irritable and are easily able to control their emotions when under that same stress.
■ Distractibility: This describes those higher-risk individuals seeking stimulation and variety, thus becoming easily distracted. Lower-risk employees, less likely to seek distraction, are better able to stay focused and alert.
■ Impulsives: These are individuals who tend to seek excitement, to enjoy taking risks and perhaps to underestimate the possible negative consequences of their actions. Lower-risk individuals do not seek excitement and tend to carefully evaluate their options before making decisions.
Change is possible
People can, of course, change their behavior. However, they are still driven by impulses defined by their natural personality. Such impulses are called defaults. Race explains: “By understanding your own defaults, you can leverage your strengths and minimize risky tendencies in order to become a safer and more effective person at home, at work and on the road.” This is where behavioral assessments come in, designed to uncover these defaults through a series of pointed questions.
Assessments provide workplace-relevant information. Some of the most popular assessments include:
■ Work Style and Performance Profile, aids managers in hiring and training top-performing work teams by identifying employees’ natural impulses relating to work (i.e., leadership and competitiveness).
■ Driver Safety Quotient. With mobile phones, in-car entertainment and countless other distractions, driving safely is becoming extremely difficult. The quotient uncovers higher-risk tendencies that lead to unsafe behavior behind the wheel.
■ Safety Quotient (SQ) identifies higher-risk characteristics among workers on industrial jobsites and helps companies hire and develop safer employees. Unlike other personality assessments, Safety Quotient has been validated in industrial settings to impact real change in workers’ behaviors, thereby reducing the overall incident rate of these industrial companies. TalentClick states that Safety Quotient has helped its clients achieve significant decreases in their injury rate. A Safety Quotient assessment takes less than 30 minutes to complete.
TalentClick believes it is the first company in North America to provide Safety Quotient specifically for blue-collar workers operating in industrial work environments. It can be tailored on a client-by-client basis to further improve its accuracy in predicting safety-related outcomes.
The company claims it has been validated for use in industrial workplaces and has been proven to reduce workplace incidents by 25 to 50 percent.
Four steps toward revealing defaults
TalentClick’s behavioral assessments break down into four steps, starting with a survey of roughly 10 to 15 minutes in which participants are asked a variety of questions designed around one specific outcome relating to their work-styles. Responses are based on a sliding scale from “strongly agree” to “strongly disagree.”
Once the participant submits the completed survey, the information is sent instantly to the TalentClick Black Box for processing (step two). TalentClick has a set of proprietary algorithms that determine a person’s risk levels based on the answers submitted.
Next, the participant receives a score, along with a self-coaching report. The employer receives a report geared toward hiring, training and coaching. Finally, step four, the employer and participant use the awareness gained from the report to improve effectiveness in the workplace.
Assessments in mining
A theme TalentClick often hears from mining customers is the importance for workers to be able to keep calm and cooperative and think clearly when under pressure or stress. Aggregate producers do not want employees becoming anxious and irritable where they lose focus on the tasks at hand and rush, panic or engage in conflicts with co-workers.
One source of stress often overlooked but that goes hand in hand with mining is temperature. Extreme heat and extreme cold are both uncomfortable states and they often bring out the worst in workers.

Knowing who can handle the uncomfortable times and remain focused is critical, as well as knowing who might need more attention and coaching when the going gets tough. Knowing this about your workers allows preventative actions to be taken to avoid safety incidents.
Magnet safety information decreases risk of injuries
The Eriez website offers helpful information to educate operators on proper safety precautions and procedures when handling magnetic equipment. This information is provided through Eriez’ Orange University and available on the company’s website.
“Industrial strength magnetic separators play a very important role in facilities across the world. If handled properly, they are a safe, efficient way of removing unwanted ferrous contamination,” says Bill Dudenhoefer, manager – separation products. “If not handled properly, injuries and property damage can occur. Potential injuries include everything from minor pinched fingers to more serious crushed hands and even the loss of extremities.”
In an effort to avoid any magnet-related accidents or damage, the Eriez website provides detailed magnet safety information regarding awareness, proper magnet handling, transportation and storage, medical devices that could be affected while handling magnets, credit-card malfunctions and permanent damage to electronic devices that come in contact with magnets.
The magnet safety information is provided through Eriez Orange University, a comprehensive educational resource that includes Eriez’ mobile training center, literature library, free tools, newsletters, videos, articles, the Eriez Technical Center and more.
Michael Schwartz edited U.K.-based mining magazines before moving to Canada where he is working as a freelance journalist.