In the hard rock world, producers must keep product moving.
There are a plethora of systems, equipment and components that must be maintained and be operational to make this happen. One component that’s often at the center of discussion is bearings.
Bearings are present in nearly every piece of rotating equipment on-site, including crushers, gearboxes, trucks, pulleys and idlers. Several of these pieces of equipment use mounted bearings with special seal arrangements for regreasing, while others such as idlers may use sealed-for-life components.
In the tough conditions these bearings are placed in, durability and contamination prevention are key. This contrasts with indoor applications using similar bearing products, which see no impact from the environment and minimal impact from other contaminants besides settling dust.
Seals in aggregate applications are intended to prevent ingress of foreign materials at all costs, which typically means increased drag on the rotating shaft. This can be a big deal for idlers on long, overland or slope-belt conveyors. But for in-plant conveyor idlers and nearly all pulleys, bearing seal drag is of little importance.
Digging in
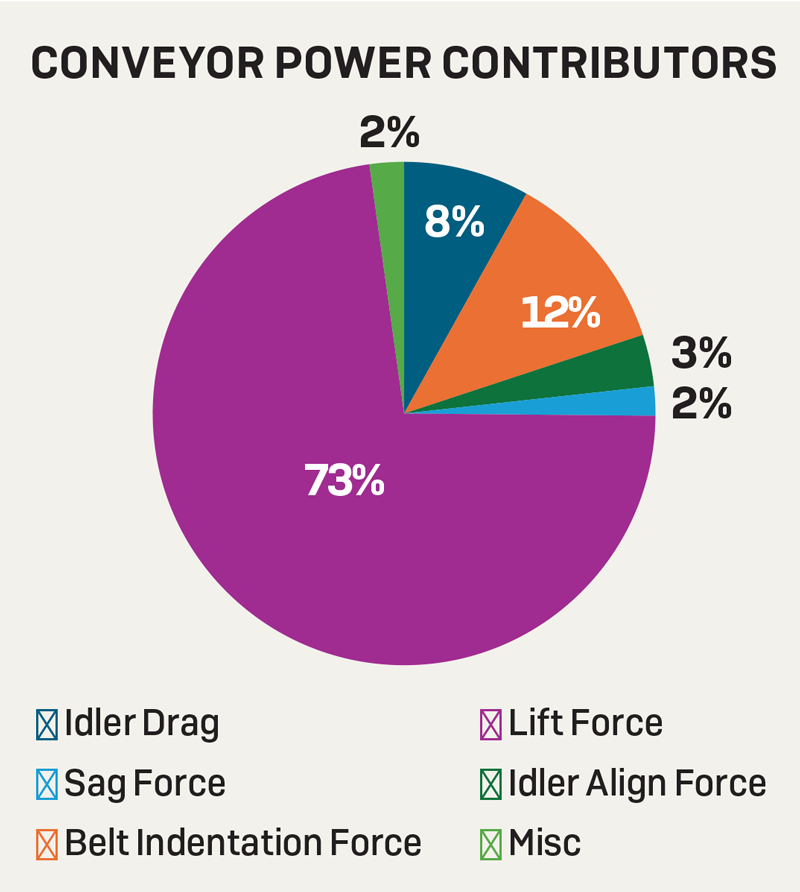
An analysis of even a relatively long conveyor shows the impact of idler drag is still only a piece of the puzzle, with most of the power consumption driven by the lifting force on an inclined conveyor as material is moved around the plant.
Idlers may add up to hundreds of bearings on a conveyor, but mounted bearings like the Type E may only be present on two pulley assemblies. Because of this, the starting force needed to turn the bearings rarely influences the conveyor design or power needs. Consider the following:
• Starting torque. Required to turn the bearing from rest.
• Rolling friction. Friction present during operation.
• Seal friction. Caused by the interference of seals between stationary and rotating components.
Often, bearings are judged by the resistance to turning in an “as manufactured” state. This is the least time-intensive way to sample turning torque, but it also paints an inaccurate picture of the influence a bearing has on the power demands of a conveyor.
It is good practice to perform run-in tests of components to arrive at more accurate, operational values to be useful for power consumption calculations during the design phase of a project, or when troubleshooting in the field.
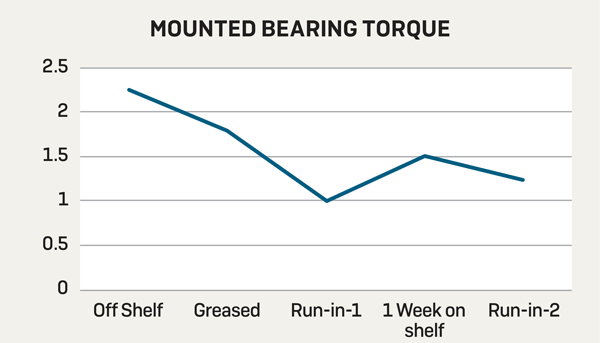
Starting torque can increase from a variety of factors, including high-grease volume, seal lubrication or seal alignment. After bearings are greased and begin to purge, the grease volume reaches its running volume, which can be less than 30 percent by volume. This not only reduces internal rolling element drag, but also the friction under the seal.
It is common for a new bearing to have a much higher drag compared to the true operational conditions. While the drag could be nearly double that during operation, it is still minimal compared to the torque typically put into a pulley via the belt. The high wrap on even a snub pulley (typically 20 to 40 degrees) means the pulley can easily overcome bearing drag contributors.
Other considerations
Consider, too, that grease and seals can impact idler bearing drag.
Industrial applications should always use some type of contact seal on their bearings, as these are wear components and, even when proper greasing intervals are used, dirt can quicky compromise labyrinth or clearance seals.
Yes, the contact seal will increase the power requirements for any bearing, but the small change can usually be accounted for with the same motor size. Plus, the benefits far outweigh the risks for challenging applications.
Taking what we now know, let’s compare the overall pulley and idler conveyor drag contributions.
Pulley bearings can often have high-interference seals. These are made possible by the relatively low rotational speed of a pulley (often less than 150 rpms) compared to idlers (often greater than 500 rpms), as well as the low quantity of these bearings (four to 12 on a 200-ft. conveyor versus 200 or more idler rolls).
Even though the larger pulley bearings may have five to 10 times the turning torque required of an idler roll, the pulley diameter and the low volume of bearings means the total drag force is very low.
For this reason, it’s clear that a well-greased and sealed bearing has minimal impact on power consumption.
Related: Determining types of bearing damage
Jeff Ellis is director of product engineering at PPI (Precision Pulley & Idler).