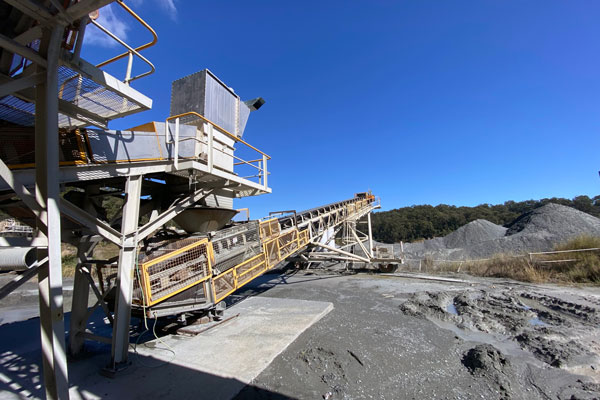
WAM’s dust collectors, including the WAMAIR model, are designed to manage and control airborne dust particles, making them a choice as an engineering control method for compliance with the Mine Safety & Health Administration’s final respirable crystalline silica rule. As the company describes, its self-cleaning filtration system, combined with high-tech filters that are water and oil resistant, are second to none. The company says its integrated air jet pulse cleaning system will only clean filters when they are needed, reducing energy consumption and increasing filter life.
Tracked crushing plants feature diesel-electric power
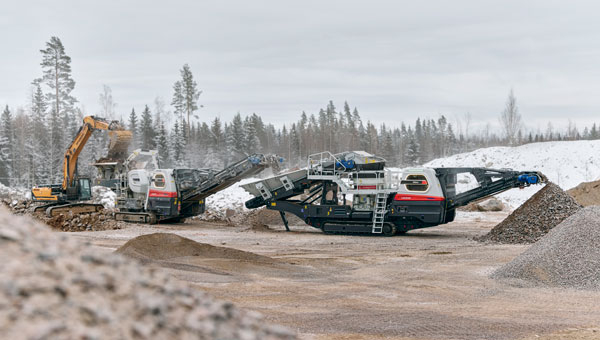
Metso’s Lokotrack EC range brings a new diesel-electric power line to aggregates. The range’s process functions are electric, the company says, reducing the use of hydraulic oil needed in crushing operations. All Lokotrack EC units can be powered with external electricity. Specifically, Metso launched the first two products of its EC range: the Lokotrack LT400J and the Lokotrack LT350C. The LT400J is a 68-ton mobile jaw crusher designed for the primary crushing of hard rock and recycled aggregates. The LT350C is a 50-ton mobile cone crusher for secondary and tertiary crushing. The LT400J relies on the Nordberg C120 jaw crusher, while the LT350C is equipped with the new Nordberg HP350e cone crusher. Both units can be utilized together.
Plant designed for coarse material from the start
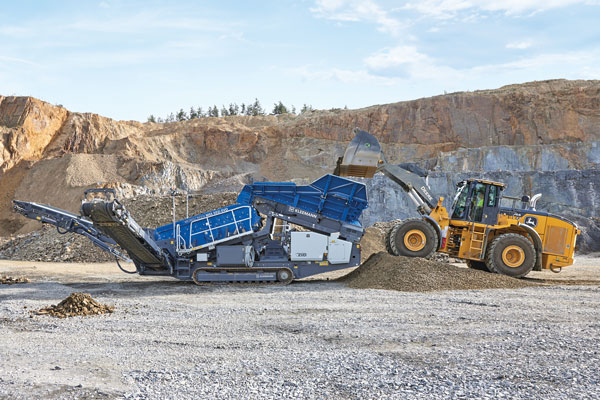
The new Mobiscreen MSS 502(i) EVO is a compact screening plant from Kleemann that’s optimized for feed capacities up to 350 tph. As Kleemann describes, the Mobiscreen MSS 502(i) EVO features a generously dimensioned feed hopper, a screening surface of 5.4 sq. meters and a wide crusher discharge conveyor. The wide setting range of the screen casing angle (15.4 to 20 degrees) makes a high screening capacity possible along with a high product quality. The screen decks of the Mobiscreen MSS 502(i) EVO can be covered to match an individual application case. A mixed covering of screen decks is also possible.
Crushing & scalping plants go electric, debut at show
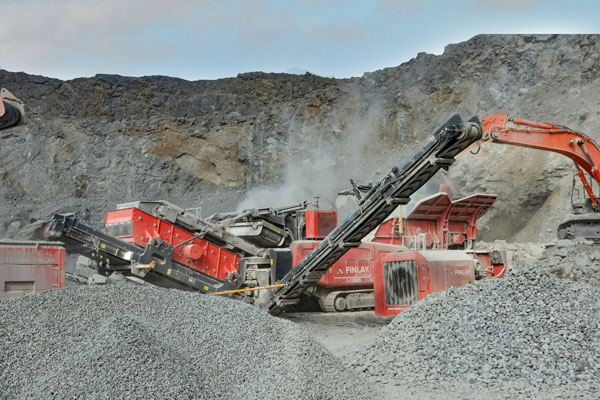
Finlay planned to unveil electric variants of its I-120RS impact crushing plant and the 883+ scalping screen plant at Hillhead 2024. As Finlay describes, the electrification of the plants represents an ongoing effort to offer environmentally friendly solutions without compromising on performance or reliability. According to Finlay, the electric I-120RS provides the flexibility of a mobile impact crushing and screening plant on one platform. For applications not requiring recirculation of materials for further processing or stockpiling, Finlay says the complete screening and recirculating system can be quickly detached from the plant. The electric 883+ heavy-duty scalper, meanwhile, is designed to work in primary and secondary screening applications such as quarrying.
Maximize tire life while reducing cost of ownership
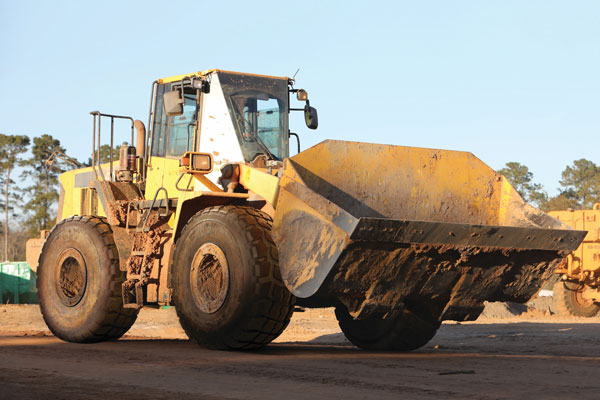
The V-Steel Z Traction (VZT) construction tire is Bridgestone Americas’ latest 25-in. product innovation for loader and grader applications. Bridgestone says the VZT is designed to maximize tire life and help reduce total cost of ownership. According to the company, the VZT is made up of advanced tread compounds that were engineered to help improve heat, cut and tear resistance while increasing total tire life by up to 15 percent compared to a previous generation product. A new tread pattern design offers 9 percent improved traction, Bridgestone adds, and optimal sidewall shape and protectors help to minimize damage and enhance defense against tears and cuts.
Domestically made thruster brake ideal for draglines
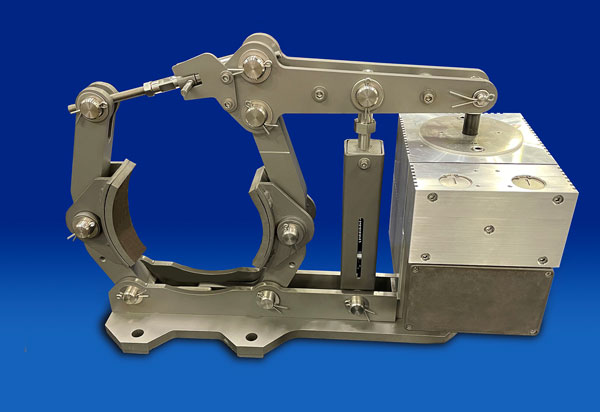
Force Control Industries debuted an AC thruster brake that meets BABAA (Build America, Buy America Act) requirements. Force Control’s HT series of thrusters, which are used in mining draglines and other equipment, are designed for 8- to 16-in. frames with force ratings between 50 and 180 pounds and various stroke ratings. In addition to thruster actuators, Force Control offers weldment and cast brake frameworks. Force Control says it has improved upon shoe brake technology with a pair of slotted arms that eliminate shoe drag and ensure brake pads wear evenly. Shoe drag is a common problem with other thruster brakes, the company says, resulting in one brake pad wearing out prematurely and, thus, requiring replacement of both brake pads – plus the downtime for service.