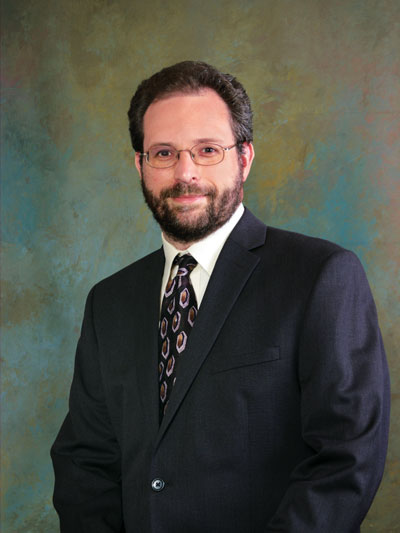
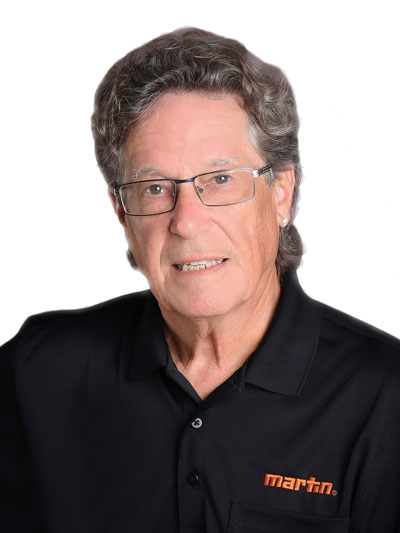
Industry groups and associations, standards-writing organizations, countries, states and cities have issued thousands of pages of performance-based safety regulations.
In many cases, rules within a country contradict each other or are not applicable to the industry to which they are enforced. The effort required for suppliers to comply with the myriad of rules is immense, and these efforts are often negated by the varying opinions of a multitude of inspectors.
Conforming to the complicated assortment of regulations and passing opinion-based inspections becomes problematic at best. But it seems clear that countries with specification-based standards have lower fatality rates.
Understaffed or undertrained personnel
The lack of adequate funding for maintenance is epidemic in the bulk materials handling industry.
Millions of dollars are spent on components, yet these investments are often made without the added maintenance budget needed to keep the components in a sound and safe operating condition.
Generally, the size of a maintenance crew is based on mean time between failure for major pieces of equipment. This is based on the illogical conclusion that workers can maintain all the minor components of the system in their “spare” time.
Production done safely
Most equipment is not designed for easy inspection or safe maintenance.
As a result, during scheduled production outages – which are becoming shorter and less frequent in the false belief that running “flat out” increases production – the maintenance of minor components must often be deferred due to access conflicts, lack of time or budgetary constraints. This further reduces components’ functionality, often to the point where they become both useless and unrepairable.
Conveyor systems are powerful and designed to be rugged and durable to deliver near-constant operation. A belt can be dragged across piles of dirt or inoperative idlers for extended periods of time, as long as the major functions are kept running.
If the components critical to maintaining a clean and safe work environment were made service-friendly and installed with adequate access, much of the beneficial maintenance could be done safely while the conveyor is in operation.
While most maintenance workers are skilled technicians, they rarely understand the conveyor holistically. Conveyors are complex, integrated systems. A change to one component will often have unintended consequences for others, affecting the rest of the system.
Without a complete understanding of how conveyors are designed and the components selected, maintenance becomes an exercise in finding the longest-lasting Band-Aids to treat the symptoms rather than solving the root causes. Before long, an accumulation of bad choices in treating symptoms results in a system that cannot operate at maximum efficiency.
Treating symptoms shortens component life and results in the need for increased spare parts. This, in turn, increases the need for maintenance labor.
Safety pays
A conveyor improvement investment would rarely be justified on safety alone, and current financial analyses do not include safety in a meaningful way.
The industry has reached a point where engineering controls, additional regulations and protective equipment are no longer sufficient to continue the trend of improving safety. Instead, the way conveyor systems are addressed must be changed.
The change must include the way conveyor components are specified, designed, purchased, operated and maintained.
Ultimately, an altered way of looking at accidents financially, a change in design methodology and a change in purchasing methodology will allow conveyor operators to create safer environments, increase efficiency and achieve the goal of “production done safely.”
Todd Swinderman and Daniel Marshall are with Martin Engineering.