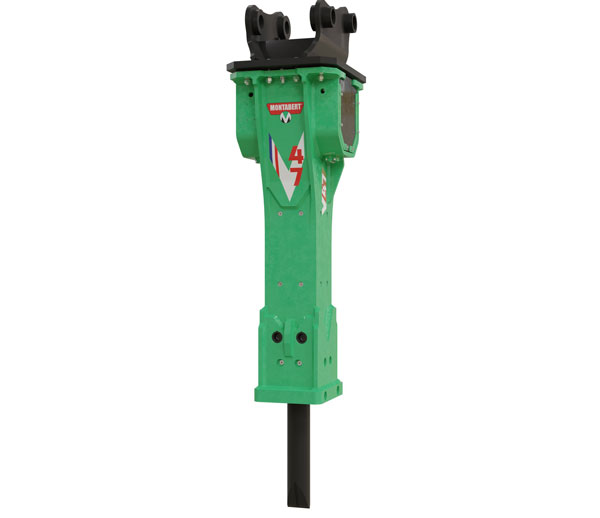
Montabert upgraded its line of variable-speed breakers with three new models that offer higher performance and lower operational and maintenance costs than their predecessors – most notably using repairable components. According to the company, the new breaker housings provide enhanced ergonomics, increased safety and greater durability. Named for their automatic variable-speed technology, Montabert says its variable-speed breakers are built for use in the harshest conditions, as they sense changes in material hardness and adjust the breaker’s impact energy and striking rate. The result is increased productivity, depending on the application, and reduced blank firing.
Optimizing performance through digitalization
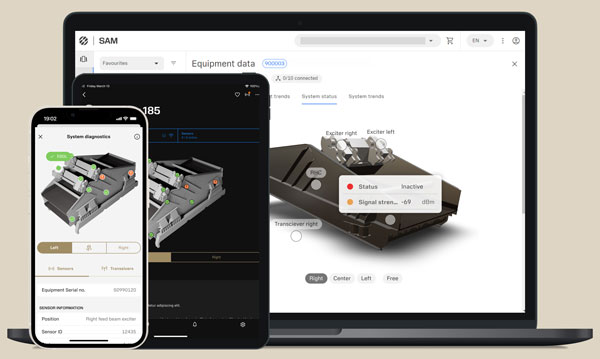
The latest models in the Sandvik 800i cone crusher series feature the new ACS-c 5 automation system. With ACS-c 5, Sandvik says plant operators and maintenance personnel gain access to valuable operational insights that enable smoother operations. Both ACS-c 5 and the ACS-s condition monitoring system are seamlessly integrated with SAM by Sandvik, the company’s cloud-based digital assistant that supports operational excellence in crushing and screening plants. SAM captures data from all connected Sandvik equipment, offering a comprehensive overview of the entire operation. Operators can monitor equipment status, communicate across teams, receive alerts and notifications, and proactively order spare parts – all from a centralized platform.
Static jaw offers equipment longevity, minimized maintenance
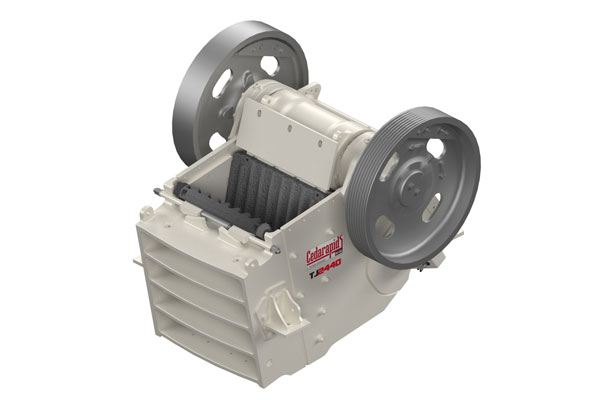
The TJ2440, which is part of the Cedarapids static jaw crusher series, features a 24-in. inlet gape by a 40-in. inlet width. The single-toggle jaw crusher is engineered for tight closed-side settings, keeping an aggressive nip angle and crushing stroke that results in maximum productivity. As Cedarapids describes, the robust design ensures reliable operations with minimal downtime, supplying smooth and efficient crushing. Typical applications for the TJ2440 single-toggle jaw crusher are mining, quarrying and recycling.
Crushing plant features diesel-electric drive
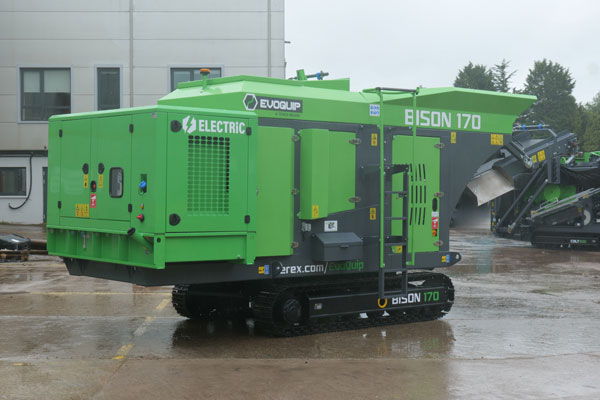
The Bison 170 jaw crushing plant featuring a 27.5-in. x 19.6-in. jaw chamber is suitable for both natural rock and recycling applications, according to EvoQuip. The Bison 170 has a range of environmentally friendly features offering customers value, high performance, ease of use and maneuverability, the company says. The Bison 170 utilizes a diesel-electric drive system with an onboard generator to power the plant. It can be plugged in and driven from an external power source such as mains power, which allows for zero emissions processing.