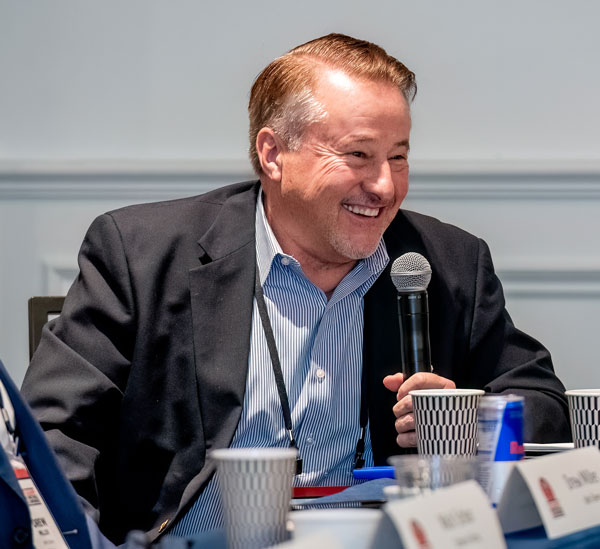
PIT & QUARRY: Our industry obviously values and prioritizes safety. That’s evolved as a value over the last 40 or 50 years into priority No. 1 for our industry. That said, we saw 40 fatal mining accidents take place last year. So, how are you evolving your safety approach?
STEWART PETROVITS (ROUTE 82 SAND & GRAVEL): We have a really good safety record. It’s terrific. But you want to know what concerns me? It’s drugs.
In New York, marijuana is legal now. We can’t test as part of DOT testing for drivers. We can’t test pre-employment for anybody. We can’t measure it post-accident. At the same time, we’re expected to improve our safety activities. The government is legalizing things that make jobsites inherently unsafe to some degree.
We don’t have a drug problem, really, and I think rigorous hiring procedures are helpful. But I think it’s only going to get easier to evade detection or easier to obtain drugs or substances.
To me, that’s my biggest concern: someone having an incident on the jobsite and injuring an innocent person or a pedestrian because of the availability of the drugs that are in society today.
DAMIAN MURPHY (PECKHAM INDUSTRIES): We had 37 incidents in our business in 2021 [with] 1,200 employees. We’ve taken that down to nine this past year.
What we’ve done is have a Peckham engagement policy, charging everybody in a managing role and an industry role to get out to the sites and do an observation on the site with an employee; have a conversation with the individual; and focus on their responsibilities. It’s not about what they see and what the subject of the conversation was; it’s restating the message constantly – over and over again – that it’s up to you as the individual to be safe.
We’re providing the training. We’re providing the resources. You have to provide the action. They have to own their safety.
SCOTT ALEXANDER (SUMMIT MATERIALS): Over the years, I have seen a tremendous amount of emphasis put on the safety side of our industry – and certainly within our company. I found that [our] recordable rate went down 25 percent this year, year over year. That’s a great reduction.
We did multiple things there, but at the end of the day it really depends on your hiring and your workforce. We’ve gotten a lot more selective. I mean, the industry is short [on people]. We hear it all day about how we don’t have enough people, so it’s very tempting to just put somebody in there. But there’s a direct correlation with your safety incidents.
Regarding the minimum for training, we’ve taken that and tripled the amount of time [dedicated], assigning mentors for each new employee. I went to a plant that had no incidents and no recordables. I got everybody $50 gift cards. Totally unexpected. They were super excited.
But I asked the manager there: ‘These are great safety results for the plant, but why is that?’ He looked at me and pointed at all of his workers. He said: ‘I have had no turnovers. Everybody is watching each other’s back. They know about our culture within the company and how we don’t just say safety is important. We live it.’
We have got to have the leadership in the field, but it also boils down to your hiring and who you have on your team.