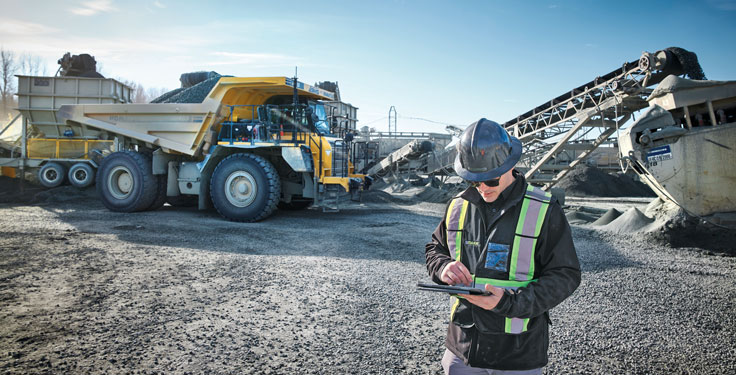
Screen media is often an afterthought for mineral processing operations.
In the car world, an equivalent would be tires. When purchasing a new vehicle, buyers are often focused on larger, flashier components such as the exterior, the engine or the latest electronic bells and whistles over more standard parts such as tires.
Still, just as tires are essential to a vehicle’s overall performance, so too is screen media for machinery in the aggregate industry.
Tires come in different varieties – similar to screen media. Beyond standard wire screens, many operations choose between polyurethane and high-vibration woven wire.
Each has its strengths and weaknesses depending on application.
Weighing polyurethane and high-vibration screen media against application, durability, efficiency and maintenance can illuminate which is the best choice for production needs.
The true cost behind cost per ton
Price is often a motivating factor when selecting screen media, but the full story of productivity can’t be summed up by just looking at either screen media panel cost or the cost of production per ton.
Much like a scale, the amount of output must be weighed against end product quality.
Because of its durability and longer wear life, synthetic media such as polyurethane is often selected as a lower-cost option because it requires fewer replacements than high-vibration screens. Its durability is also effective when used to handle high-impact material screening such as dewatering, or when processing large amounts of minerals with little risk of pegging or blinding.
Polyurethane panels, however, trade durability for less open area. And they’re much more rigid, therefore relying on the vibrating screen to do most of the work. The static movement of the screens limits vibration to 800 to 900 cycles per minute, which can decrease throughput and invite blinding and pegging with finer minerals.
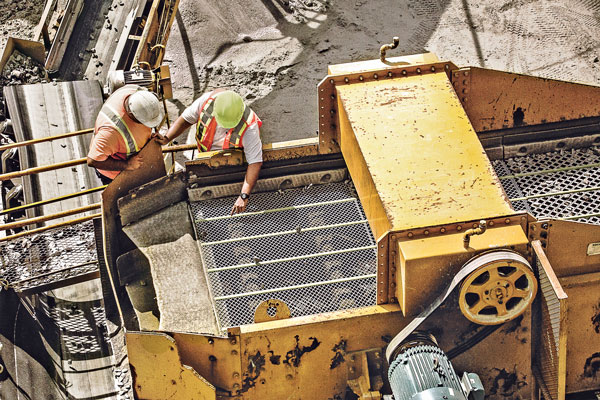
In comparison, high-vibration screen media has as much as 50 percent more open area than polyurethane, which allows more material to be sized accurately in less time.
This result is achieved through the high frequency of its wires – 8,000 to 10,000 cycles per minute – that adds to the vibration of the screen box to speed up material separation and passing.
This performance requires more changeouts of screens because unprotected woven wire breaks more easily than polyurethane. The trade-off to more frequent replacements is that the increased screening action improves material throughput, virtually eliminates pegging and clogging across the top and bottom decks, and yields a better-quality product. With high-vibration screen media, a higher investment upfront can lead to greater production gains down the road.
While polyurethane screens currently outlast a wire product, the gap has been closing. The inclusion of polyurethane strips within the design of high-vibration wire boosts its durability without sacrificing open area. This addition means high-vibration panels can withstand harsher screening conditions with the most abrasive materials, such as granite and basalt.
In some applications, the strengths of polyurethane and high-vibration screens can complement one another. In cases where the top deck receives heavy material with a high impact and requires a longer wear life, using a synthetic screen would be best. Once the polyurethane has taken the impact and the material is spread out more easily on the lower deck, a high-vibration screen can be used to overcome the limitations of the open area of the synthetic screen and produce more throughput.